2025 Autor: Howard Calhoun | [email protected]. Ostatnio zmodyfikowany: 2025-06-01 07:14
Kierownik każdego przedsiębiorstwa, bez względu na dziedzinę działalności, marzy, aby zyski rosły, a koszty produkcji pozostały niezmienione. W osiągnięciu tego wyniku pomaga system „5S” w produkcji (w wersji angielskiej 5S), który opiera się wyłącznie na racjonalnym wykorzystaniu rezerw wewnętrznych.
Ten system nie został stworzony od zera. Coś podobnego pod koniec XIX wieku zaproponował Amerykanin Frederick Taylor. W Rosji zrobił to naukowiec, rewolucjonista, filozof i ideolog A. A. Bogdanow, który w 1911 r. wydał książkę o zasadach zarządzania naukowego. Na podstawie zawartych w nim przepisów ZSRR wprowadził NOT, czyli naukową organizację pracy. Ale najdoskonalszy był system 5C zaproponowany przez japońskiego inżyniera Taiichi Ohno i wprowadzony przez niego w produkcji w fabryce Toyota Motor. Co to jest i dlaczego japoński system stał się tak popularny?
Faktem jest, że opiera się na prostej zasadzie, która nie wymaga kosztów. Składa się znastępny - każdy pracownik, od sprzątacza po dyrektora, powinien maksymalnie zoptymalizować swój udział w całym przepływie pracy. Prowadzi to do wzrostu zysku całej produkcji i wzrostu dochodów wszystkich jej pracowników. Teraz pałeczkę wprowadzenia systemu „5C” przejęły przedsiębiorstwa na całym świecie, w tym w Rosji. W tym artykule postaramy się przekonać sceptyków, że japoński know-how naprawdę działa i to w absolutnie każdej dziedzinie działalności.
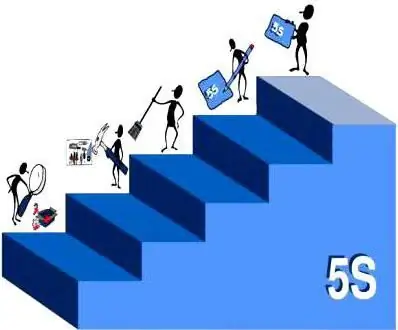
System "5C" w produkcji, co to jest
International 5S oznacza pięć kroków („krok” w języku angielskim „krok”). Część ekonomistów i propagatorów nowego podejścia do pracy tłumaczy tę nazwę pięcioma japońskimi postulatami konsekwentnie realizowanymi w systemie 5S: seiri, seiton, seiso, seiketsu i shitsuke. Dla nas bliższe i bardziej zrozumiałe są nasze rodzime „5C” - pięć kolejnych kroków, które należy wykonać, aby osiągnąć prosperity naszej produkcji. To jest:
1. Sortuj.
2. Utrzymanie porządku.
3. Utrzymanie czystości.
4. Standaryzacja.
5. Ulepszenie.
Jak widać, system „5C” nie wymaga niczego nadprzyrodzonego w produkcji. Być może dlatego wciąż można spotkać się z nieufnością i frywolnym stosunkiem do niej.
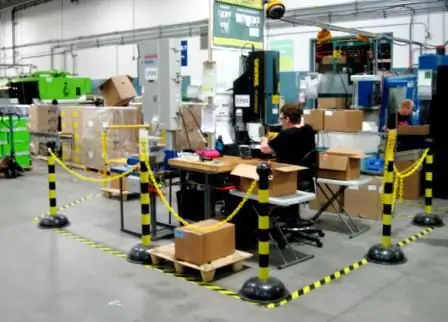
Etapy tworzenia systemu
Mądry Japończyk Taiichi Ohno, któremu dzięki wprowadzeniu swoich metod w fabryce Toyoty udało się wyrosnąć zinżynier do CEO, zauważył, jak wiele strat powstaje z powodu różnych niespójności i nakładek. Na przykład niektóre małe ślimaki nie zostały włożone na przenośnik na czas, w wyniku czego cała produkcja została zatrzymana. Lub odwrotnie, części były dostarczane z marżą, okazały się zbędne iw efekcie jeden z pracowników musiał je odwieźć do magazynu, co oznaczało marnowanie czasu na pustą pracę. Taiichi Ohno opracował koncepcję, którą nazwał „just in time”. Oznacza to, że na przenośnik dostarczono dokładnie tyle części, ile potrzeba.
Można podać inne przykłady. W produkcji systemu „5S” pojawiło się również pojęcie „kanban”, co po japońsku oznacza „znak reklamowy”. Taiichi Ohno zasugerował dołączenie tak zwanego znacznika „kanban” do każdej części lub każdego narzędzia, w którym podane były wszystkie niezbędne informacje o części lub narzędziu. Zasadniczo dotyczy wszystkiego. Na przykład do towarów, leków, folderów w biurze. Trzecią koncepcją, na której opiera się system 5S w produkcji, jest koncepcja „kaizen”, czyli ciągłego doskonalenia. Powstały również inne koncepcje, które nadawały się tylko do wysoko wyspecjalizowanych procesów produkcyjnych. W tym artykule nie będziemy ich rozważać. W wyniku wszystkich przetestowanych w praktyce innowacji powstało 5 kroków, które mają zastosowanie do każdej produkcji. Przeanalizujmy je szczegółowo.
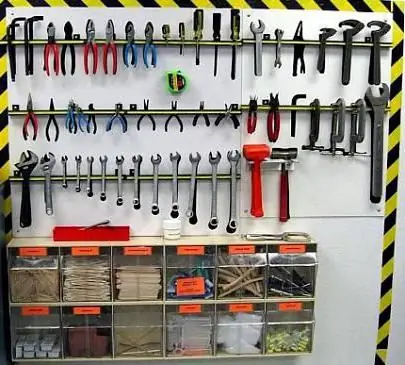
Sortowanie
Wielu z nas ma na swoich pulpitach elementy, które ww zasadzie nie potrzebne. Na przykład stare formularze, nieużywane teczki, szkice obliczeń, serwetka, na której stała filiżanka kawy. A wśród tego chaosu mogą znaleźć się niezbędne akta lub dokumenty. Podstawowe zasady systemu „5S” to optymalizacja pracy, czyli upewnienie się, że nie marnujesz czasu na szukanie właściwych rzeczy wśród gruzów niepotrzebnych. To jest sortowanie. Oznacza to, że w miejscu pracy (w pobliżu maszyny, na stole, w warsztacie - w dowolnym miejscu) wszystkie przedmioty są ułożone w dwóch stosach - niezbędnym i niepotrzebnym, które należy wyrzucić. Ponadto wszystko, czego potrzebujesz, rozkłada się na następujące stosy: „używane często i stale”, „używane rzadko”, „prawie nieużywane”. To kończy sortowanie.
Utrzymanie zamówienia
Jeśli po prostu zdemontujesz przedmioty, nie będzie to miało sensu. Należy ułożyć te przedmioty (narzędzia, dokumenty) w takiej kolejności, aby to, co jest stale i często używane, było widoczne lub aby można było je szybko zabrać i łatwo odłożyć. To, co rzadko używane, można wysłać gdzieś w pudełku, ale trzeba do niego dołączyć tag kanban, aby po chwili można go było łatwo i dokładnie znaleźć. Jak widać, system 5S w miejscu pracy zaczyna się od najprostszych kroków, ale w rzeczywistości okazuje się bardzo skuteczny. A poza tym poprawia nastrój i chęć do pracy.
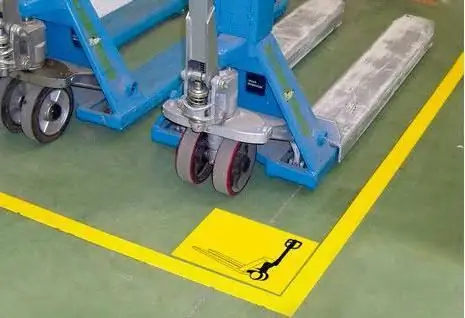
Utrzymanie czystości
Ten trzeci krok jest dla wielu najbardziej logiczny. Uczymy się być czystymi od dzieciństwa. Naw produkcji jest również niezbędna, a nie tylko stoły pracowników biurowych czy szafki w zakładach gastronomicznych, ale również maszyny, pomieszczenia gospodarcze środków czyszczących powinny być czyste. W Japonii pracownicy dbają o swoje miejsca pracy, są sprzątani trzy razy dziennie - rano przed pracą, w porze lunchu i wieczorem, na koniec dnia pracy. Ponadto ich przedsiębiorstwa wprowadziły specjalne oznakowanie obszarów, które pozwalają im obserwować porządek w produkcji, to znaczy obszary gotowych produktów, przechowywanie niektórych części itd. są oznaczone różnymi kolorami.
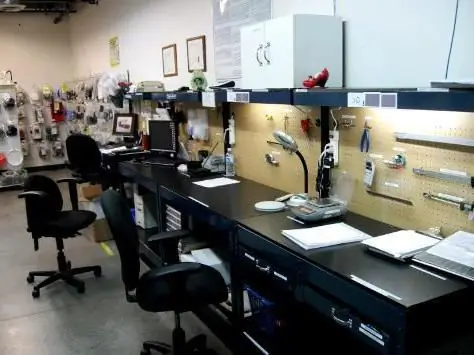
Standaryzacja
Zasady standaryzacji zostały wymyślone przez Taiichi Ohno. Są również szeroko stosowane przez nowoczesny system 5S. Zarządzanie produkcją dzięki standaryzacji otrzymuje wspaniałe narzędzie do kontrolowania wszystkich procesów. Dzięki temu przyczyny opóźnień z harmonogramu są szybko eliminowane, a błędy, które prowadzą do wydania produktów o niskiej jakości, są korygowane. W zakładzie Toyota Motor standaryzacja wyglądała tak: brygadziści sporządzali dzienne plany pracy, precyzyjne instrukcje były wywieszane w miejscu pracy, a pod koniec dnia pracy specjalni pracownicy sprawdzali, jakie odchylenia od planu wystąpiły w ciągu dnia i dlaczego. To podstawowa zasada standaryzacji, czyli precyzyjnych instrukcji, planów pracy i kontroli nad ich realizacją. Obecnie wiele przedsiębiorstw, np. zakłady ENSTO w Estonii, wprowadza system premiowy dla pracowników, którzy ściśle przestrzegają przepisów systemu 5C i na tej podstawie zwiększają swoją produktywność, coto świetna zachęta do przyjęcia tego systemu jako sposobu na życie.
Poprawa
Piąty krok, kończący produkcję systemu „5S”, opiera się na koncepcji kaizen. Oznacza to, że wszyscy pracownicy, niezależnie od zajmowanego stanowiska, powinni dążyć do usprawnienia procesu pracy w powierzonym im obszarze. Filozoficzna esencja kaizen polega na tym, że całe nasze życie z każdym dniem staje się lepsze, a ponieważ praca jest częścią życia, nie powinna też pozostawać z dala od ulepszeń.
Pole działania tutaj jest szerokie, ponieważ doskonałość nie ma granic. Według koncepcji Japończyków sami robotnicy powinni chcieć usprawnić swój proces produkcyjny, bez instrukcji i przymusu. Obecnie wiele organizacji buduje zespoły pracowników, którzy monitorują jakość produktów, uczą innych swoich pozytywnych doświadczeń i pomagają osiągnąć doskonałość.
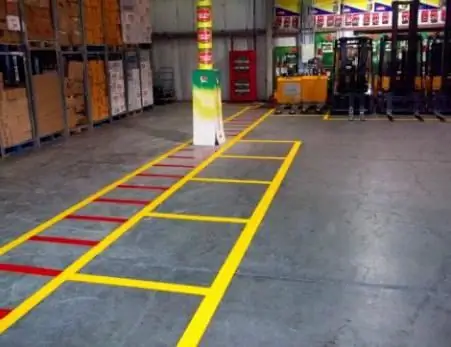
Podstawowe błędy
Aby system „5C” zaczął działać, nie wystarczy zorganizować go lub zatrudnić pracowników, którzy zmuszą do jego wdrożenia swoich kolegów. Ważne jest, aby ludzie zdali sobie sprawę z użyteczności tej innowacji i zaakceptowali ją jako styl życia. Wprowadzenie do produkcji systemu „5S” w Rosji napotyka na trudności właśnie dlatego, że nasza rosyjska mentalność różni się od japońskiej. Wiele naszych produkcji charakteryzuje się następującymi cechami:
1. Pracownicy, zwłaszcza jeśli nie ma dla nich zachęt, nie dążą do zwiększania zysków przedsiębiorstwa. Pytają,po co próbować czynić szefa jeszcze bogatszym, skoro ma już wszystko.
2. Sami liderzy nie są zainteresowani wprowadzeniem systemu „5S”, bo nie widzą w nim celowości.
3. Wiele dyrektyw „z góry” jest przyzwyczajonych do wykonywania tylko na „tykanie”. W Japonii jest zupełnie inny stosunek do ich pracy. Na przykład ten sam Taiichi Ohno, wprowadzając system „5S”, nie myślał o osobistym zysku, ale o korzyści firmy, w której był tylko inżynierem.
4. W wielu przedsiębiorstwach system 5S jest wprowadzany na siłę. Produkcja odchudzona, która implikuje eliminację wszelkiego rodzaju strat (czas pracy, surowce, dobrzy pracownicy, motywacja i inne wskaźniki), nie działa, ponieważ pracownicy zaczynają opierać się innowacjom na poziomie podświadomości, co ostatecznie redukuje wszelkie wysiłki do zera.
5. Menedżerowie wdrażający system nie do końca rozumieją jego istotę, co powoduje awarie w ustalonych procesach produkcyjnych.
6. Standaryzacja często przeradza się w biurokrację, dobry uczynek przerasta instrukcje i dyrektywy, które tylko przeszkadzają w pracy.
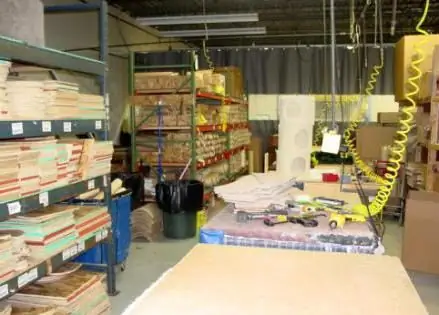
Recenzje
Rosjanie, którzy wprowadzili do produkcji system „5S”, opinie na temat tej innowacji są bardzo niejednoznaczne. Wyróżnione zalety:
- lepiej być w miejscu pracy;
- nie odwracaj uwagi od pracy niepotrzebnymi drobiazgami;
- bardziej przejrzysty przepływ pracy;
- zmęczenie zmniejszyło się pod koniec zmiany;
- nieznacznie zwiększonawynagrodzenie poprzez zwiększenie wydajności pracy;
- zmniejszenie liczby urazów zawodowych.
Odnotowane wady:
- przy sortowaniu zmuszają wszystko do wyrzucenia;
- normalizacja doprowadziła do wzrostu biurokracji;
- Wprowadzenie systemu „5C” nie zaostrzyło problemów we wszystkich obszarach przedsiębiorstwa;
- Umieszczenie systemu 5S na pierwszym miejscu przyćmiło ważne kwestie, takie jak brak części zamiennych.
Zalecana:
"Kanban", system produkcji: opis, istota, funkcje i recenzje
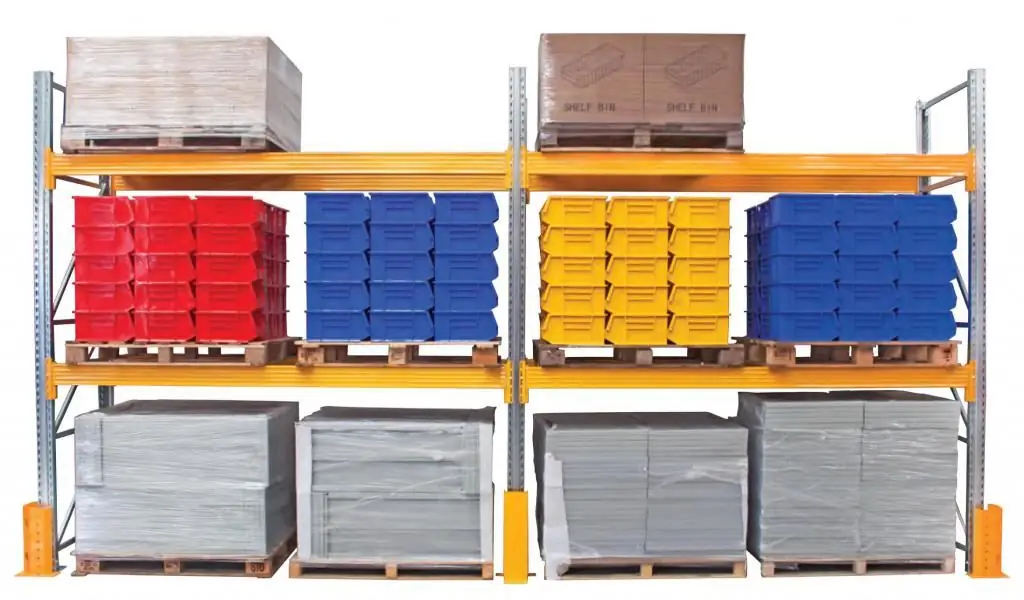
Kanban to najbardziej znana metoda zarządzania produkcją przemysłową w ramach koncepcji Just-in-Time. Przy minimalnych kosztach organizacyjnych może znacznie skrócić czas pracy i koszt zasobów materiałowych
Gęsi włoskie: opis gatunku, cechy pielęgnacyjne, rozmnażanie, cechy charakterystyczne, zasady utrzymania i opłacalność
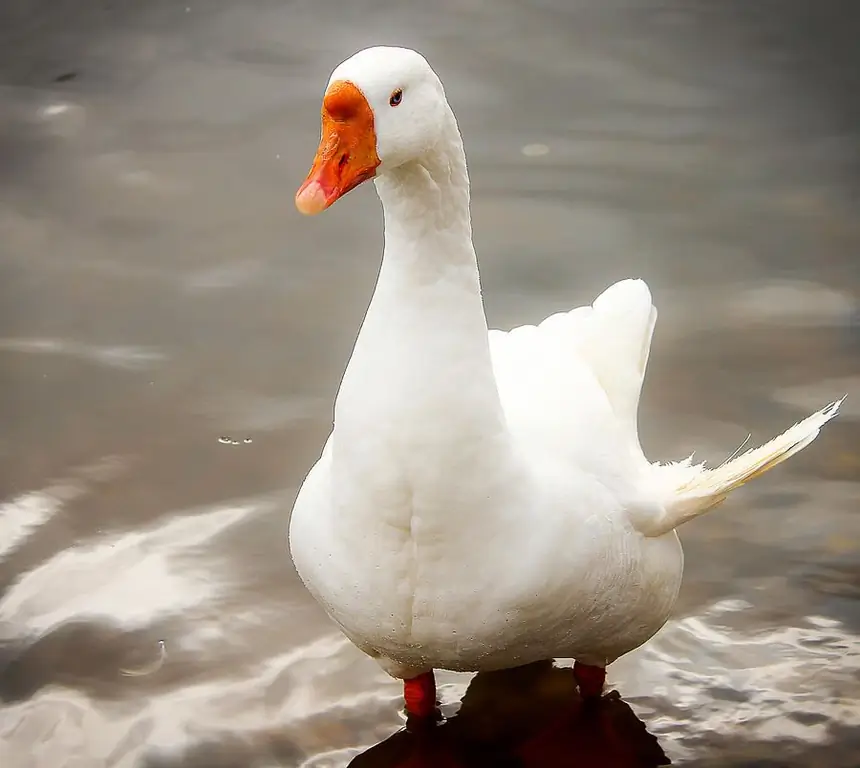
Hodowla gęsi to świetny sposób na zarabianie pieniędzy dla rolnika. Są bezpretensjonalne w opiece, szybko przybierają na wadze i są poszukiwane wśród ludności. Białe włoskie gęsi nie tylko przyniosą dobry dochód, ale także ozdobią swoim wyglądem dziedziniec. Ptaki dobrze przystosowują się do różnych warunków przetrzymywania, mogą być hodowane w dowolnej strefie klimatycznej. Włoskie gęsi – dar niebios dla przedsiębiorczego rolnika
Przepływowe metody organizacji produkcji: parametry, cechy i normy. Potrzeba tej metody w produkcji
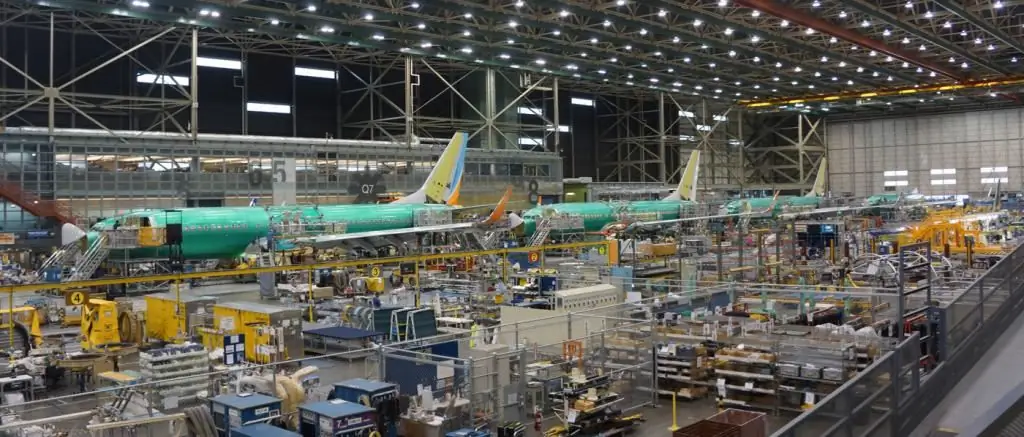
Dziś produkcja in-line jest najbardziej postępową formą organizacji systemu produkcyjnego. Optymalna szybkość pracy, minimalna pracochłonność i maksymalna jakość produkcji - to nie jest pełna lista zalet rozważanej metody
Króliki rasy Strokach: opis gatunku, cechy opieki, rozmnażania, cechy charakterystyczne rasy i zasady trzymania
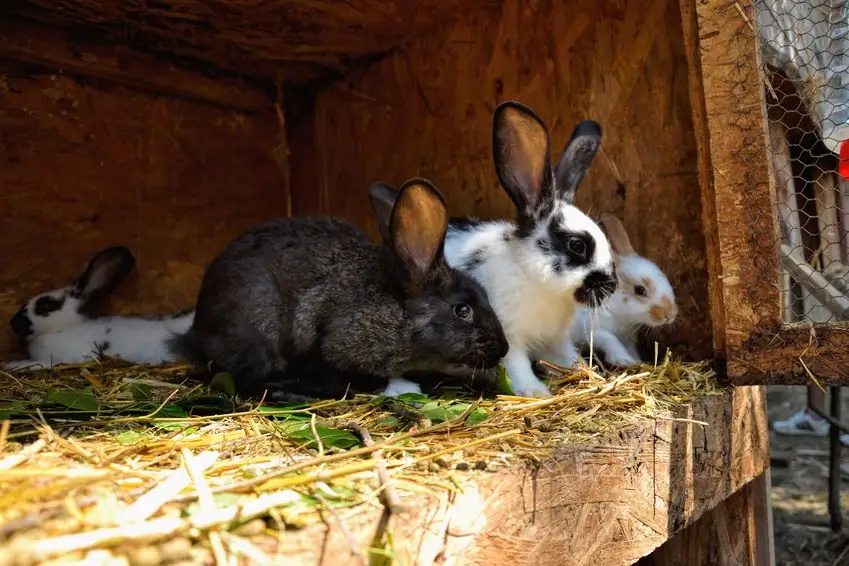
Jeśli ktoś ma na celu hodowanie królików rasy Strokach, to trzeba pamiętać, że najlepiej mieć tylko najsilniejsze i najlepsze osobniki rasy niemieckiej. W przypadku uprawy w domu wielu rolnikom nie zawsze udaje się wyhodować czystą rasę, ponieważ niektóre osobniki są różnorodne lub chorują
Francuskie owce króliki: recenzje, hodowla, pielęgnacja, cechy rasy, zasady żywienia i opis ze zdjęciem
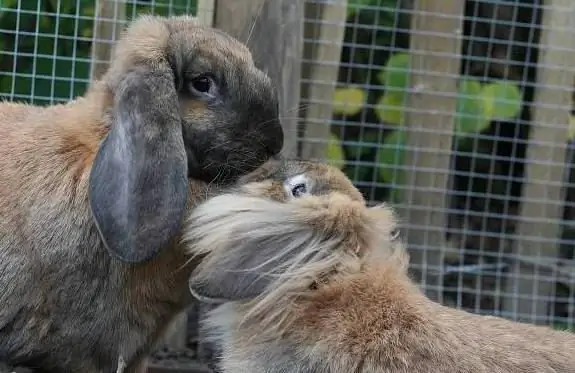
Króliki Francuskie recenzje baranów od rolników zasługują na bardzo dobre. Zwierzęta te, zdaniem właścicieli gospodarstw, są bardzo produktywne, a ponadto dość bezpretensjonalne. Aby uzyskać dobre tempo przyrostu masy, króliki te muszą oczywiście przede wszystkim być odpowiednio karmione i utrzymywane