2025 Autor: Howard Calhoun | [email protected]. Ostatnio zmodyfikowany: 2025-06-01 07:14
System zarządzania Kanban to logistyczna metodologia organizacji przedsiębiorstw przemysłowych. Łatwość wdrożenia, możliwość znacznej oszczędności zasobów materiałowych oraz wzrost ogólnego poziomu kontroli przyczyniły się do jego popularności i popularności.
Historia tworzenia i rozwoju
Początkiem systemu Kanban jest Japonia, gdzie po raz pierwszy zastosowano go w fabryce samochodów Toyota Motors na początku lat 60-tych. Rozwój i wdrożenie wiązały się bezpośrednio z koniecznością minimalizacji strat finansowych poprzez „natychmiastową” kontrolę stanów magazynowych oraz terminową realizację wymaganych zadań. Do chwili obecnej głównym obszarem zastosowania jest produkcja przemysłowa, zwłaszcza przy ciągłych cyklach produkcyjnych (przemysł samochodowy, transport kolejowy itp.). Biorąc pod uwagę prostotę algorytmu osadzonego w rozważanej metodzie, w ostatnich latach jest to jedno z najbardziej efektywnych podejść do zarządzania projektami.
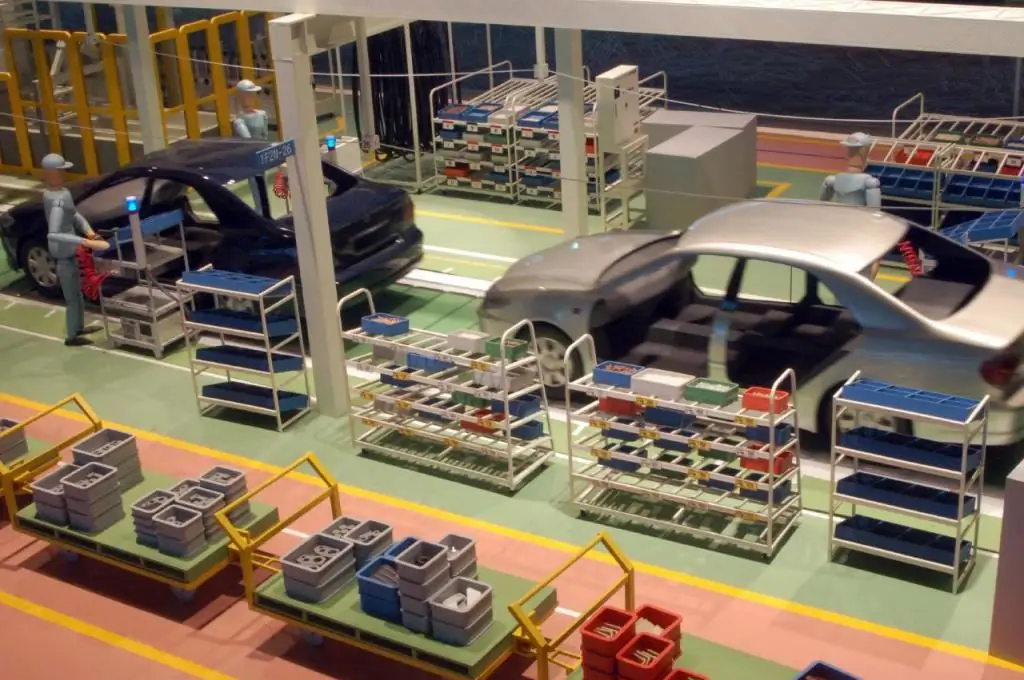
Pchaj czy ciągnij?
Kanban narodził się w wyniku doskonalenia przedsiębiorstwa na czas w celu zmniejszenia ilości odpadów i poprawy jakości produktów. Jednocześnie jego stworzenie i późniejsze wykorzystanie otworzyło nowy rodzaj zarządzania. Jeśli do połowy XX wieku wysiłki badaczy miały na celu głównie usprawnienie mechanizmów produkcji push (czyli takich, które działają pod ścisłym planem), to od momentu zastosowania systemu Kanban pojawiły się przedsiębiorstwa typu pull w logistyce. W takim przypadku zmienia się kierunek przepływu informacji.
W sklepach typu push sygnał sterujący przechodzi od lewej do prawej, faktycznie „przepychając” produkt z jednego obszaru do drugiego zgodnie z przyjętą technologią. W przypadku ściągaczy ostatnia sekcja generuje zapytanie o niezbędne komponenty z poprzednich etapów produkcji.
System produkcyjny Kanban nie jest całkowicie nowym rodzajem produkcji. Ściśle mówiąc, modele zarządzania produkcją, które pojawiły się w ciągu ostatniego półwiecza, stanowią nadbudowę klasycznych przedsiębiorstw przemysłowych. Najbardziej trafnym określeniem zdolności Kanban jest „wydajność”. Ponieważ progresywne metody unowocześniania produkcji mają na celu jej zwiększenie.
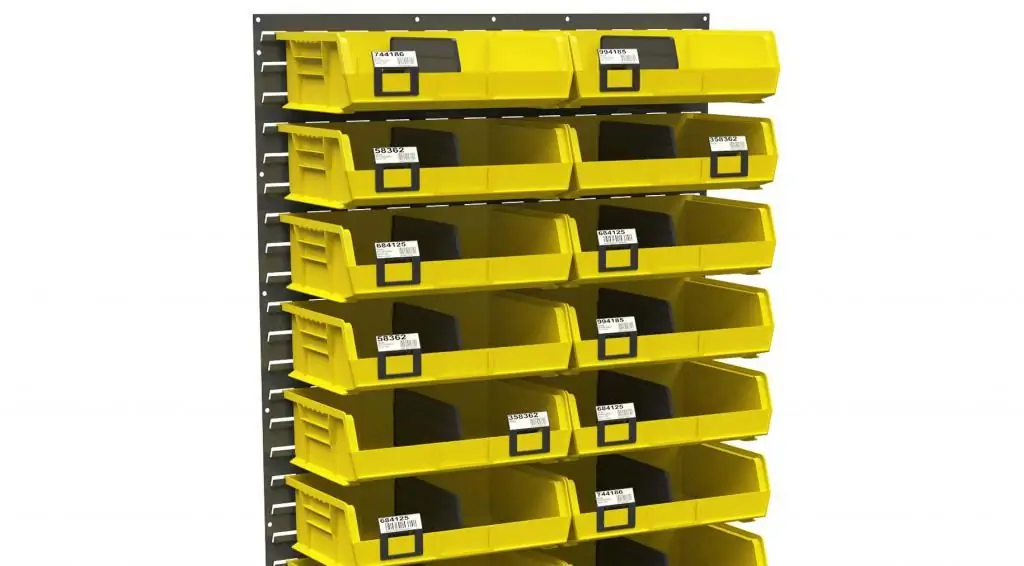
Jaka jest różnica?
Istotą systemu Kanban jest zorganizowanie płynnej realizacji zadań produkcyjnych na wszystkich stanowiskach pracy (miejscach) produkcjiproces. Charakterystyczne cechy to minimalizacja zapasów na wszystkich etapach cyklu życia produktu.
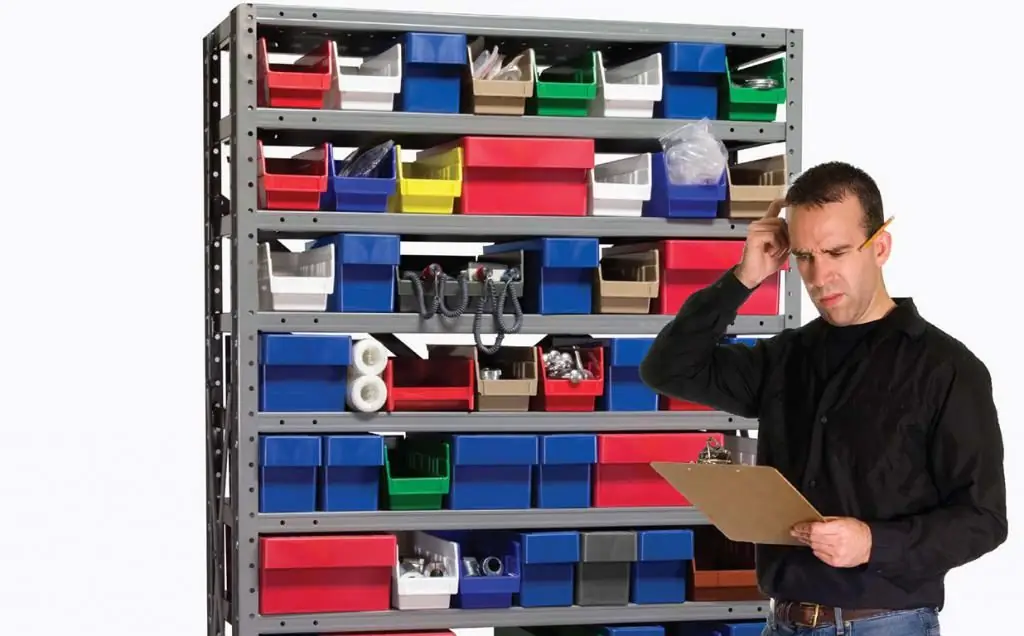
Zapasy materiałów są jednym z wąskich gardeł nowoczesnej produkcji. W praktyce istnieje duże prawdopodobieństwo wystąpienia jednej z następujących opcji:
- niewystarczające zapasy;
- Rezerwa zapasów.
Konsekwencje rozwoju pierwszego scenariusza będą następujące:
- przerwy w rytmie produkcji;
- zmniejszenie produkcji przez pracowników;
- zwiększona liczba części zamiennych i komponentów z powodu późnej konserwacji;
- wzrost kosztów produkcji.
Dla drugiej opcji charakterystyczne cechy to:
- niski obrót;
- spadek produkcji;
- wzrost strat na infrastrukturze pomocniczej (powierzchnia magazynowa, personel, media).
System Kanban zmniejsza ryzyko obu scenariuszy ze względu na przyjęte ograniczenia dotyczące dopuszczalnej ilości zasobów w łańcuchu produkcyjnym. W efekcie pojawia się „przejrzystość” procesów - widoczne są przerwy w pracy urządzeń, rzeczywista ilość małżeństwa, rzeczywista przepustowość miejsc pracy. Efektem wprowadzenia systemu jest podniesienie jakości produktu na tle znacznej redukcji kosztów.
Kluczowe elementy systemu
„Kanban” to kontrola procesów produkcyjnych za pomocą specjalnych sygnałów sterujących. Zwróć uwagę, że dla skutecznegofunkcjonowanie wymaga rozwiniętej infrastruktury interakcji pomiędzy strukturalnymi elementami produkcji, wyrafinowanej technologii wytwarzania, pracy zespołowej personelu. Głównym elementem informacji w łańcuchu produkcyjnym były plastikowe karty o różnych kolorach z różnymi informacjami (znaczenie „Kanban” z języka japońskiego to „karta”). Jego wygląd zależy od rodzaju sterowania.
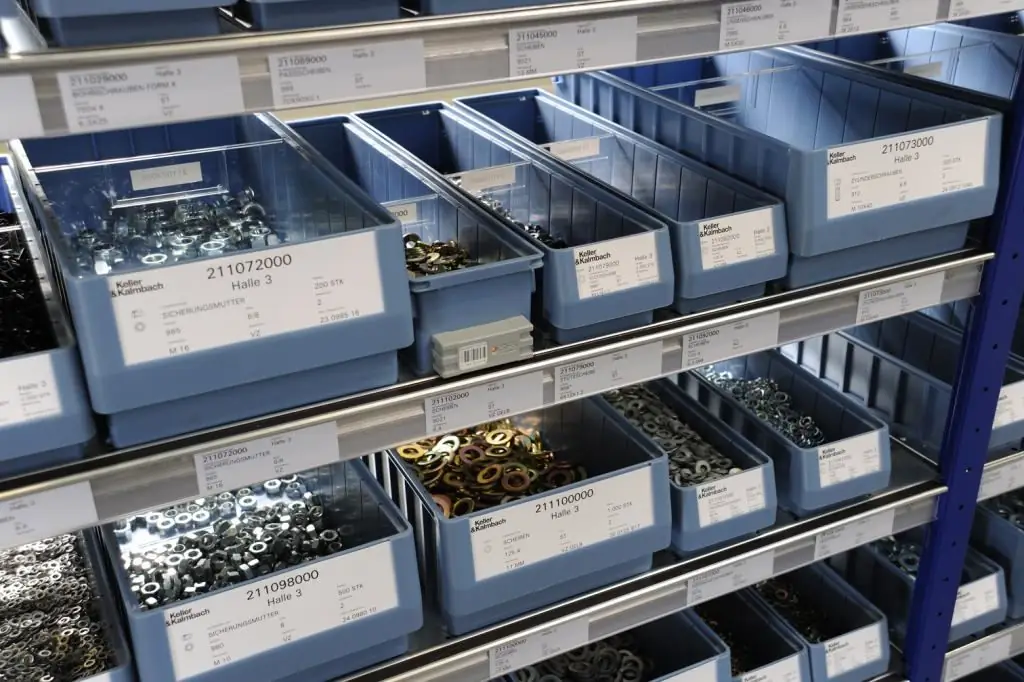
Tare Kanban
Karta danych jest zamontowana na pojemniku. O kolejności produkcji decyduje położenie samego kontenera na regale. Algorytm zamawiania jest realizowany w następujący sposób: gdy ilość części w pierwszym pojemniku z mapą się zmniejszy, zostaje on przeniesiony z pozycji roboczej na jeden z poziomów regału (który służy do składania zamówień i odbierania sygnału z pracownika obsługi transportu) i rozpoczyna współpracę z innym. Przewoźnik odbiera pusty pojemnik, obecność karty kanban wskazuje na konieczność zamówienia materiału u magazyniera lub dostawcy. Główną wadą tego typu kanban jest dodatkowa ilość opakowania dla każdego typu użytej części.
Karta Kanban
Wielokolorowa karta z informacjami o produkcji, kolor określa parametry przestrzenne niezbędnych materiałów eksploatacyjnych. W praktyce karta jest podzielona na kilka segmentów, które pokazują informacje dotyczące nadawcy i odbiorcy.
Istnieją różne schematy używania palety kolorów kart. Od monochromatycznego (białego, czarnego) do wielokolorowego. Ilość kolorów i ich wybór zależą odzłożoność procesów produkcyjnych. W przypadku konieczności wykorzystania sygnałów pomiędzy różnymi roboczymi obszarami funkcjonalnymi można zaproponować następujący schemat:
- kolor niebieski - „kanban produkcyjny” (połączenie między obszarem roboczym a obszarem dostaw);
- kolor czerwony - „kanban magazynu” (połączenie między magazynem a obszarem odbioru);
- zielony kolor - "cross-shop kanban" (komunikacja między różnymi sklepami lub kompleksami).
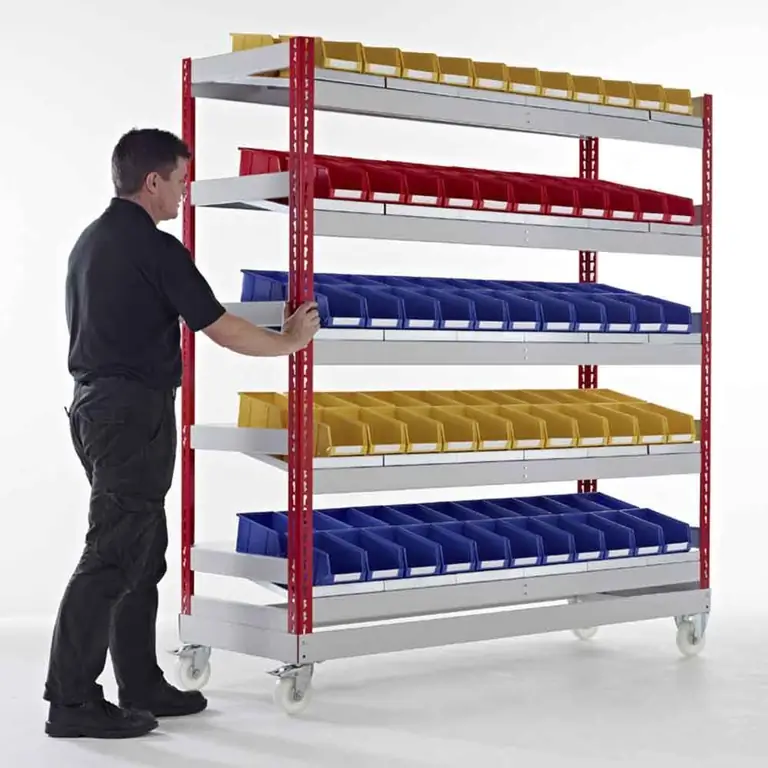
Wady i zalety
System Kanban ma wiele zalet w porównaniu z tradycyjnymi metodami zarządzania produkcją. Potwierdzają to informacje zwrotne od pracowników. Skraca czas realizacji, skraca przestoje sprzętu, optymalizuje zapasy, zmniejsza ilość odpadów, eliminuje WIP, poprawia wykorzystanie przestrzeni, zwiększa produktywność i zwiększa ogólną elastyczność zakładu. Jednocześnie ograniczenia metody są nieuniknione - konieczne jest stworzenie niezawodnego łańcucha dostaw zapasów, nie ma możliwości długoterminowego planowania zadań produkcyjnych. Według menedżerów istnieją wysokie wymagania dotyczące synchronizacji działań pracowników różnych służb.
Reasumując, system Kanban to nie tylko metoda doskonalenia procesów, to filozofia produkcji, która przy systematycznym i ciągłym stosowaniu pozwala osiągnąć wysoką wydajność przedsiębiorstwa.
Zalecana:
System „Rapida”: opis, funkcje i recenzje
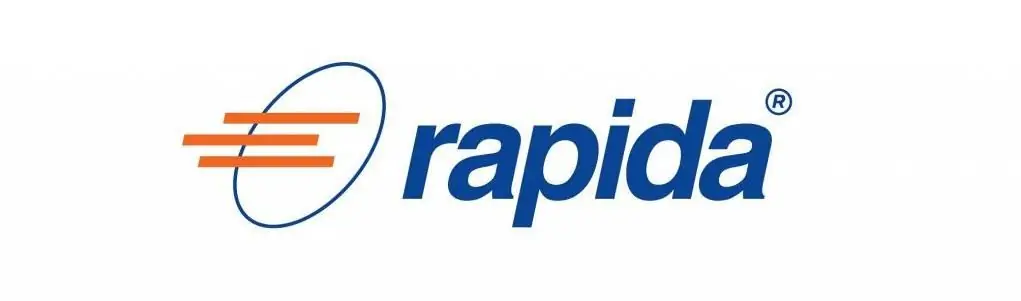
System płatności „Rapida” jest usługą powszechną. Jego usługi są odpowiednie zarówno dla zwykłych użytkowników, jak i właścicieli firm. Rozważ cechy platformy i sposób, w jaki przebiega procedura rejestracji i identyfikacji klientów
Systemy produkcji i produkcji: koncepcja, wzory i ich rodzaje
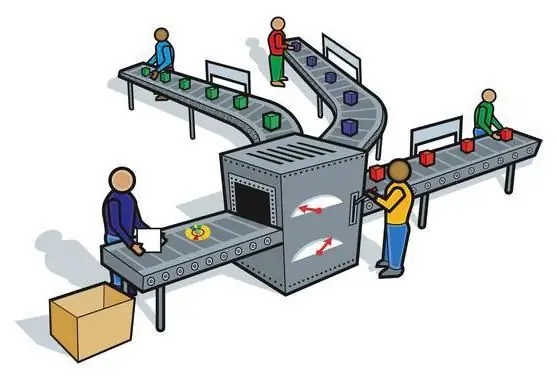
Systemy produkcyjne to struktury, w których pracują ludzie i sprzęt. Pełnią swoje funkcje w określonej przestrzeni, warunkach, środowisku pracy zgodnie z zadaniami
Nowoczesna produkcja. Struktura nowoczesnej produkcji. Problemy nowoczesnej produkcji

Rozwinięty przemysł i wysoki poziom gospodarki kraju są kluczowymi czynnikami wpływającymi na bogactwo i dobrobyt jego mieszkańców. Takie państwo ma ogromne możliwości gospodarcze i potencjał. Istotnym elementem gospodarki wielu krajów jest produkcja
Plan produkcji w biznesplanie: opis, funkcje, treść

Dokument, który nadaje projektowi szczegółowe uzasadnienie, a także możliwość kompleksowej oceny podjętych decyzji i planowanych działań jako wysoce efektywnych i pozwala pozytywnie odpowiedzieć na pytanie, czy projekt jest wart zainwestowania pieniędzy – Plan produkcji. Biznesplan powinien odzwierciedlać prawie wszystkie działania, które będą potrzebne przy zakładaniu produkcji
System „5C” w produkcji: opis, cechy, zasady i recenzje
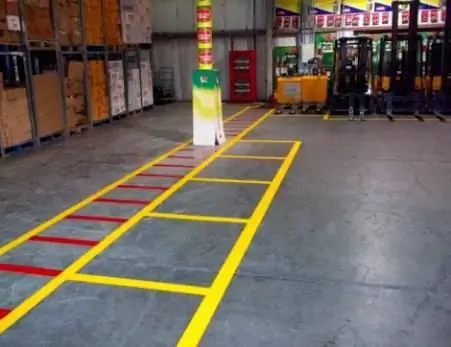
Kierownik każdego przedsiębiorstwa, bez względu na dziedzinę działalności, marzy, aby zyski rosły, a koszty produkcji pozostały niezmienione. W osiągnięciu tego wyniku pomaga system „5S” w produkcji (w wersji angielskiej 5S), który opiera się wyłącznie na racjonalnym wykorzystaniu rezerw wewnętrznych