2025 Autor: Howard Calhoun | [email protected]. Ostatnio zmodyfikowany: 2025-06-01 07:14
Złącza cierne mają wysoką nośność i są mniej pracochłonne niż złącza spawane. Dzięki temu znajdują szerokie zastosowanie w produkcji metalowych konstrukcji budowlanych. Uzyskanie niezbędnych sił tarcia w złączu odbywa się na różne sposoby - poprzez obróbkę strumieniowo-ścierną i obróbkę płomieniową, a także przy użyciu kompozycji adhezyjnych.
Opis i zastosowanie
W inżynierii mechanicznej istnieją 2 rodzaje połączeń śrubowych w zależności od charakteru przenoszenia siły w nich:
- Odporny na ścinanie. Najczęściej projektuje się je na śruby o zgrubnej, normalnej i podwyższonej dokładności (rzadko o dużej wytrzymałości). Siła dokręcania nie jest kontrolowana. Obliczenia uwzględniają wewnętrzne naprężenia rozciągające, ściskające i ścinające, ale nie uwzględniają sił tarcia.
- Tarcie (odporność na ścinanie). Siły zewnętrznej przeciwdziałają siły tarcia powstające w płaszczyznach styku łączonych części. Tarcie wynika z wstępnego obciążenia śrub mocujących, które powinno być maksymalne. Dlatego w takich połączeniach wysokowytrzymałe okucia z termicznymprzetwarzanie.
Ostatni typ jest podzielony na 2 podkategorie: połączenia cierne i cierno-ścinające, w których jedna część sił jest przenoszona przez tarcie, a druga przez zgniatanie.
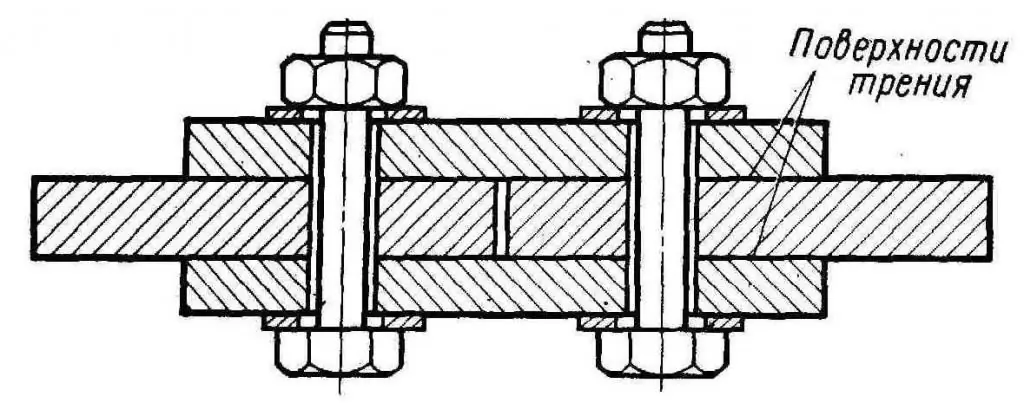
Wadą tych połączeń jest wysoki koszt elementów złącznych. Z drugiej strony zastosowanie połączeń ciernych na śrubach o dużej wytrzymałości poprawia niezawodność i zmniejsza liczbę spoin w terenie. W związku z tym złożoność montażu zmniejsza się prawie 3 razy. Ten rodzaj połączenia jest stosowany w budowie budynków przemysłowych, w budowie mostów, dźwigów i innych konstrukcji kratowych, które podlegają wibracjom lub obciążeniom dynamicznym.
Obiecującym kierunkiem rozwoju tego konstruktywnego rozwiązania jest zastosowanie usuwalnych powłok konserwatorskich oraz zastosowanie technologii wytwarzania „blokowej”, gdy montaż i malowanie powiększonych jednostek odbywa się w zakładzie, a tylko montaż odbywa się na placu budowy.
Współczynnik chropowatości
Wymaganą chropowatość powierzchni, która zapewnia obliczoną siłę tarcia, uzyskuje się przez ścierniwo, obróbkę płomieniową współpracujących powierzchni lub przez zastosowanie specjalnych powłok. Współczynnik tarcia do obliczeń pochodzi z poniższej tabeli.
Typ przetwarzania | Współczynnik tarcia |
Brak konserwacji | |
Szczotkowanie | 0, 35 |
Śrutowanie | 0, 38 |
Wytnij płomień | 0, 42 |
Śrut lub piaskowanie | 0, 58 |
Śrutowanie, czyszczenie obu części, nagrzewanie płomieniem do 300°C wokół otworów na śruby. Obszar obróbki cieplnej - nie mniejszy niż rozmiar podkładki |
0, 61 |
Z późniejszą konserwacją | |
Pierwszy szczegół - piaskowanie lub śrutowanie, konserwacja klejem. Druga część krycia - szczotkowana, bez dalszej konserwacji | 0, 5 |
Rodzaj obróbki musi być wskazany na rysunkach. Powierzchnie współpracujące są całkowicie wolne od lodu, śniegu, oleju, kamienia, rdzy i innych zanieczyszczeń przed montażem śruby.
Piaskowanie
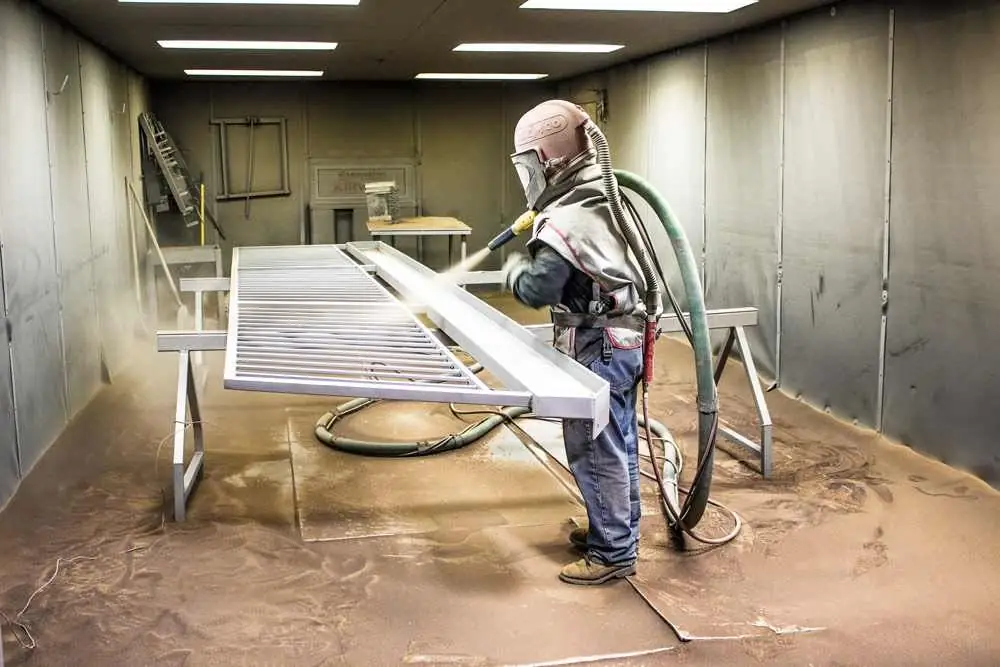
Do czyszczenia konstrukcji metalowych ze złączami ciernymi przy użyciu technologii piaskowania obowiązują następujące wymagania:
- chropowatość przygotowanej powierzchni - nie więcej niż Ra 6, 3;
- całkowita eliminacja tlenków i rdzy (drugi stopień oczyszczenia zgodnie z GOST 9.402-2004);
- stopień odtłuszczenia powierzchni - pierwszy (czas przerwania filmu wodnego - ponad 1 minuta, brak plam oleju na bibule filtracyjnej);
- wstępne czyszczenie sprężonego powietrza wchodzącego do piaskarki z oleju i wilgoci (kontrolowane co najmniej 1 raz na zmianę);suszenie piasku kwarcowego do wilgotności nie większej niż 2%.
Po piaskowaniu należy usunąć kurz z powierzchni przedmuchując powietrzem lub przecierając czystą szmatką.
Leczenie płomieniem
Płomień tlenowo-acetylenowy jest używany podczas czyszczenia części palnikiem gazowym. Produkty spalania (tlenki) są następnie usuwane za pomocą szczotek drucianych. W takim przypadku nie można nadać metalu połyskowi. Czyszczenie płomieniowe można stosować tylko do części o grubości co najmniej 5 mm, aby uniknąć ich wypaczenia termicznego. Przetwarzanie odbywa się w następujących trybach:
- ciśnienie tlenu - 0,6 MPa, acetylen w butlach - 0,05 MPa;
- dopływ tlenu - maksymalny (rdzeń płomienia powinien zejść z dyszy grzałki, ale nie zgasnąć);
- prędkość przesuwu palnika - 1 m/min (dla cienkościennych konstrukcji metalowych 5-10 mm - 1,5-2 m/min);
- następny przebieg powinien zachodzić na poprzedni o 15-20mm;
- kąt palnika do 45°.
Podczas tej operacji technologicznej wykorzystywane są specjalne palniki o szerokim płomieniu.
Czyszczenie śrutem i szczotką
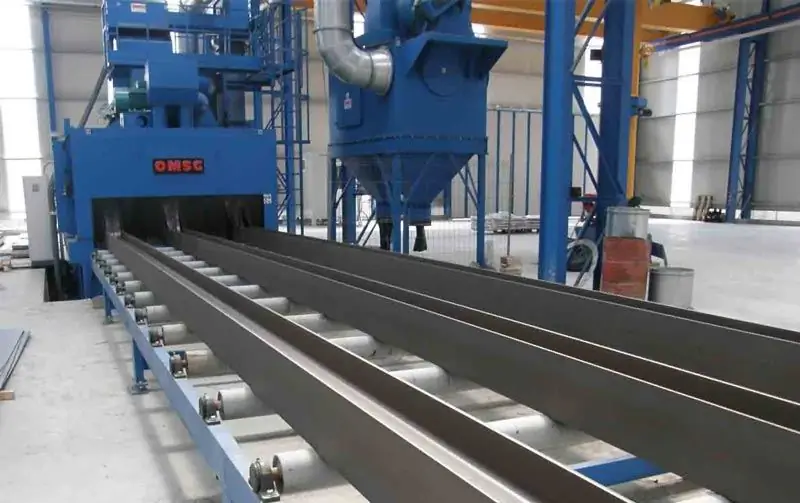
Przed obróbką szczotkami metalowymi (szczotkowanie) farbę usuwa się z powierzchni rozpuszczalnikami lub metodą płomieniową. Niemożliwe jest czyszczenie części do metalicznego połysku, ponieważ uniemożliwia to powstanie odpowiedniego współczynnika tarcia. Praca odbywa się za pomocą zmechanizowanego pneumatycznego lub elektrycznegonarzędzie. Pozostały kurz usuwa się przedmuchując powietrzem lub szczotką do włosów.
Do śrutowania stosuje się śrut stalowy lub żeliwny kruszony (siekany) o frakcji 0,8-1,2 mm. Oczyszczarki strumieniowe wykorzystują śrut żeliwny.
Powłoki
W celu zwiększenia sił tarcia w połączeniach kołnierzowych i ciernych stosuje się również substancje adhezyjne - kleje. Jako powłokę cierną stosuje się kompozycje, których głównym składnikiem jest żywica epoksydowa, a dodatkowymi utwardzacz, rozpuszczalnik, przyspieszacz lub izopropanol.
Prace montażowe prowadzone są w następującej kolejności:
- Wielkogabarytowe elementy konstrukcyjne są czyszczone jedną z metod opisanych powyżej, z wyjątkiem płomienia gazowego, a także odtłuszczane. Odstęp czasu pomiędzy czyszczeniem a klejeniem nie powinien przekraczać 0,5 dnia. Przechowywanie w tym samym czasie odbywa się w warunkach wilgotności nie większej niż 80%.
- Klej jest przygotowywany bezpośrednio przed użyciem.
- Kompozycja klejąca nakładana jest na powierzchnię mniejszych elementów i wypełniana proszkiem węglika krzemu o grubości 2 mm, wałkując metalowym wałkiem. Dozwolone jest sklejenie obu stykających się części klejem. W ciągu 1-2 godzin świeżo przygotowany klej powinien zostać całkowicie zużyty.
- Usuń nadmiar proszku, obracając część i wykonując kilka uderzeń.
- Zachowaj czas do pełnego utwardzenia żywicy epoksydowej.
- Złącze cierne jest montowane na śrubach o dużej wytrzymałości.
Jakość sprzętu
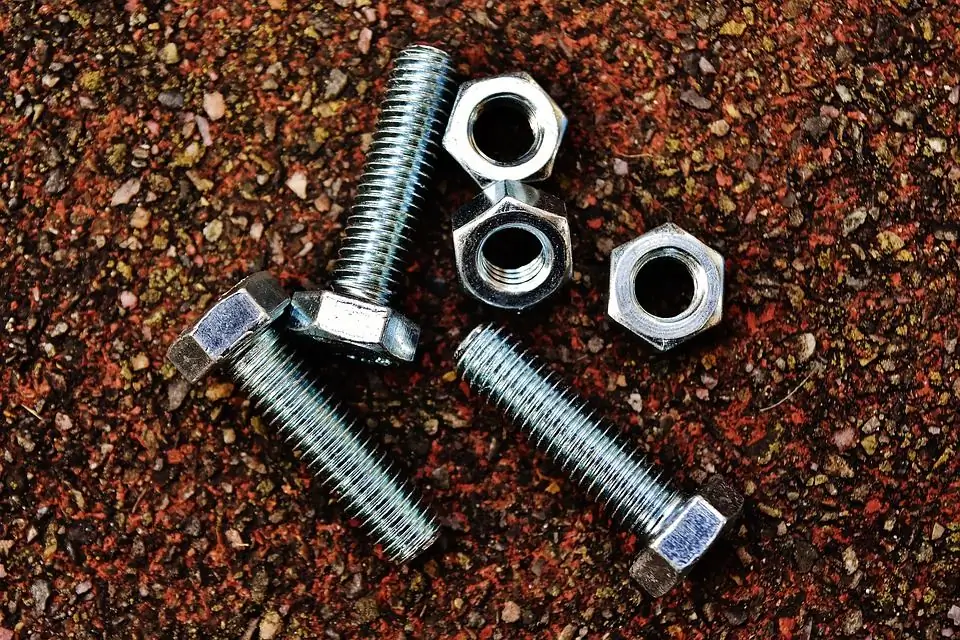
Łączniki do połączeń ciernych muszą posiadać certyfikat jakości. Śruby, podkładki i nakrętki przygotowuje się w następujący sposób:
- czyszczenie smaru konserwującego w roztworze alkalicznym (ekspozycja w pojemniku na 15-20 minut);
- suszenie, przedmuchiwanie sprężonym powietrzem;
- gwintowanie za pomocą kluczy lub na tokarce;
- smarowanie olejami mineralnymi;
- kompletny zestaw śrub z sparowanymi nakrętkami, które były używane podczas pracy;
- przechowywanie do czasu montażu (nie dłużej niż 10 dni).
Obliczanie połączenia ciernego
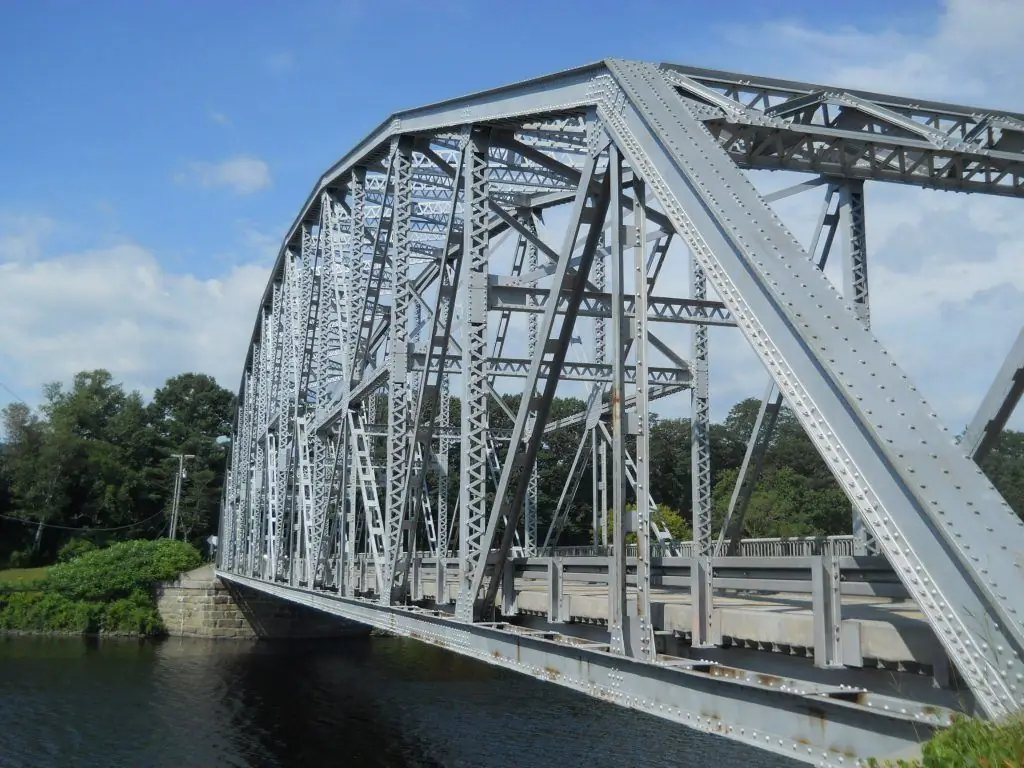
Najważniejszymi parametrami połączenia tego typu są:
- współczynnik tarcia Μ na powierzchniach styku, określony z powyższej tabeli, w zależności od rodzaju obróbki;
- przełożenie momentu obrotowego śrub;
- siła dokręcania śrub;
- moment obrotowy wymagany do uzyskania wymaganej wartości poprzedniego wskaźnika.
Wyliczoną wartość momentu obrotowego można znaleźć według wzoru:
M=K∙N∙dnom, gdzie K jest współczynnikiem momentu obrotowego określonym zgodnie z GOST 22356-77;
N - siła naciągu śruby, kN;
dnom - jego średnica nominalna, mm.
Wartość N jest określona przez wzór:
N=σr∙Sn∙ k,
gdzie σr jest wytrzymałością na rozciąganie materiału śruby, N/mm2;
Sn - pole przekroju śruby,netto, mm2;
k - współczynnik warunków pracy (dla konstrukcji stalowych i mostów drogowych wynosi 1).
Siła generowana w jednym kontakcie śrubowym jest określona wzorem:
N1=N∙Μ/ɣ, gdzie ɣ jest współczynnikiem niezawodności, dobieranym w zależności od liczby śrub w połączeniu.
Minimalna wymagana liczba śrub o wysokiej wytrzymałości jest określana w następujący sposób:
n=P/(k∙N1∙s), gdzie P to działające obciążenie wzdłużne, kN;
s - liczba kontaktów w połączeniu.
Montaż
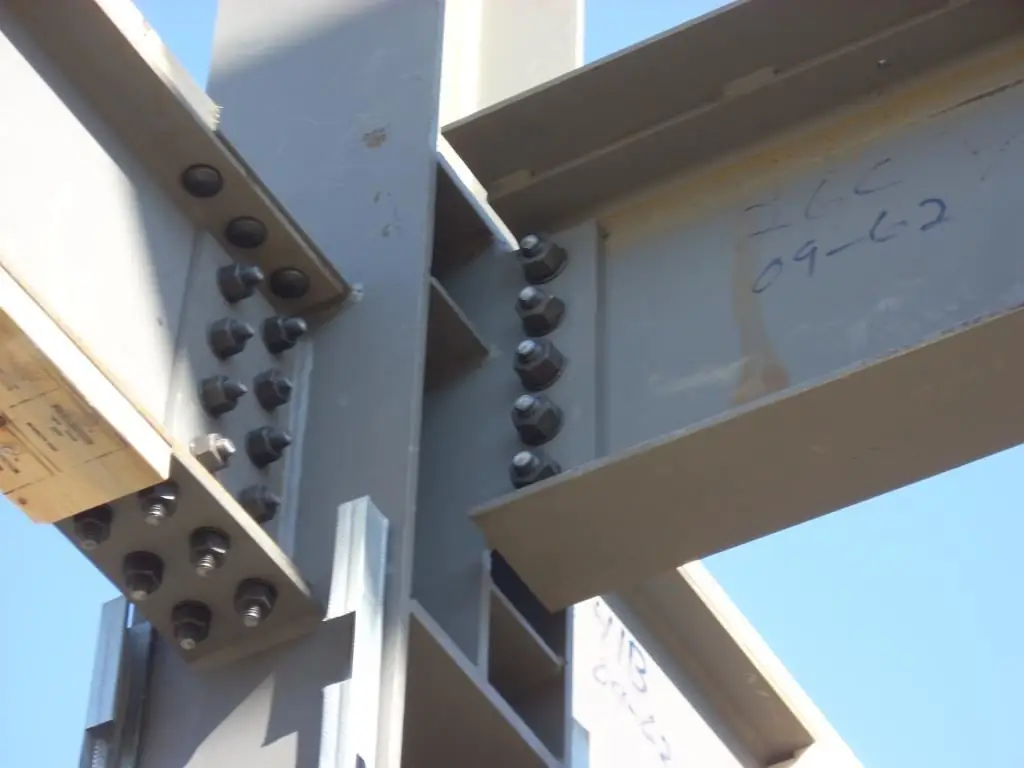
Zasady wykonywania połączenia ciernego muszą być zgodne z następującymi wymaganiami technicznymi:
- Przed montażem konieczne jest przygotowanie powierzchni jedną z powyższych metod (zgodnie z dokumentacją projektową), usunięcie nierówności i zadziorów, które uniemożliwiają dokładne dopasowanie części.
- Podczas transportu i tymczasowego przechowywania części należy wykluczyć zaolejenie lub zanieczyszczenie przygotowanych powierzchni. Jeśli nie można tego uniknąć, konieczna jest druga procedura czyszczenia.
- Na pierwszym etapie montażu części są wyrównane z otworami za pomocą kołków montażowych.
- Zamontuj śruby z podkładkami (nie więcej niż jedną pod łbem śruby i nakrętką), dokręć je nakrętkami o 50-90% obliczonej siły i sprawdź szczelność połączenia.
- Dostosuj obliczony moment dokręcania za pomocą kluczy dynamometrycznych.
- Nałóż kit lub podkład zmieszany zcement, biała glina, kreda. Ma to na celu uszczelnienie połączenia przed wilgocią.
Kontrola jakości
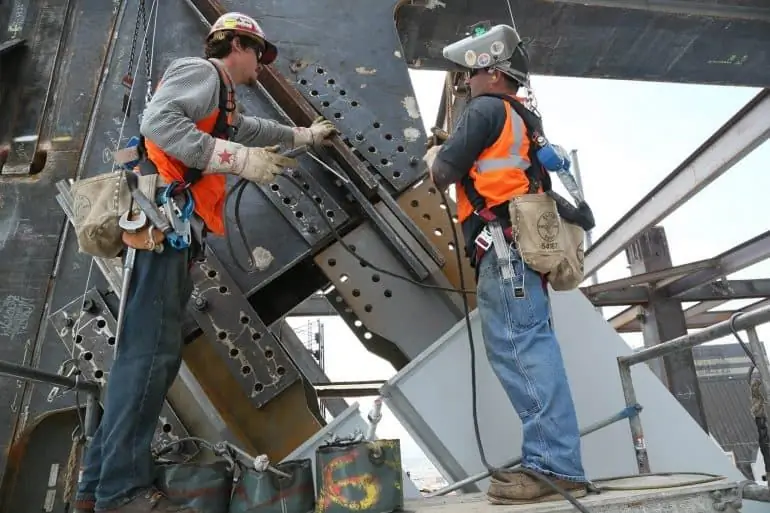
Kontrola jakości przeprowadzana jest na wszystkich etapach przygotowania i montażu. Wyniki kontroli międzyoperacyjnych są zapisywane w dzienniku produkcji połączeń w terenie.
Kompleks takich prac obejmuje następujące operacje:
- przychodząca kontrola jakości surowców, komponentów, zakupionych produktów;
- sprawdzanie stanu narzędzia, tarowanie kluczy dynamometrycznych;
- kontrola czyszczenia powierzchni i przygotowania sprzętu;
- Sprawdzanie gęstości dokręcania połączeń (za pomocą sond);
- selektywna kontrola momentu dokręcania;
- kontrola ciśnienia;
- próbki testowe (zgodnie z wymaganiami klienta robót budowlanych).
Zalecana:
Doradztwo strategiczne w dużej firmie
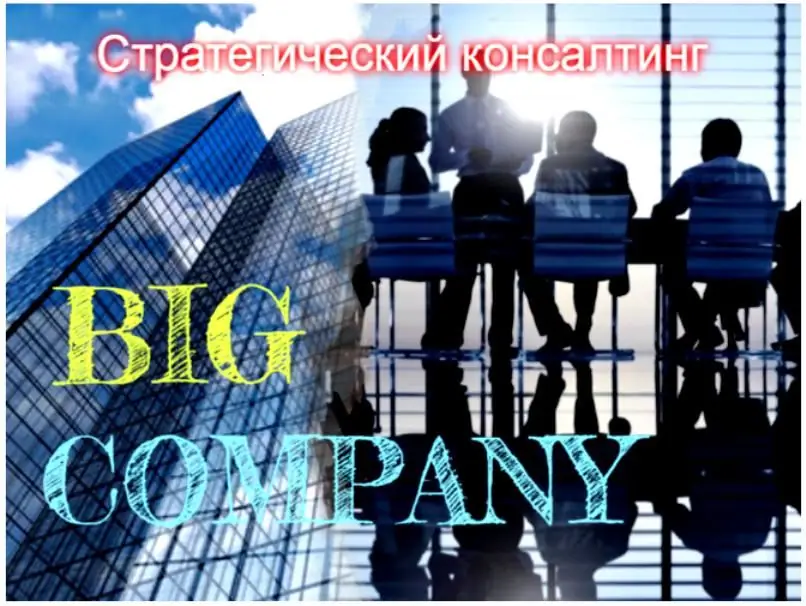
Duże firmy konsultingowe odgrywają kluczową rolę w strategicznym zarządzaniu firmami. Ale wielu jest zainteresowanych nauką, w jaki sposób opracowują strategie, które mogą doprowadzić każde przedsiębiorstwo na stanowiska kierownicze
Sprzęgła cierne: zasada działania, rysunek
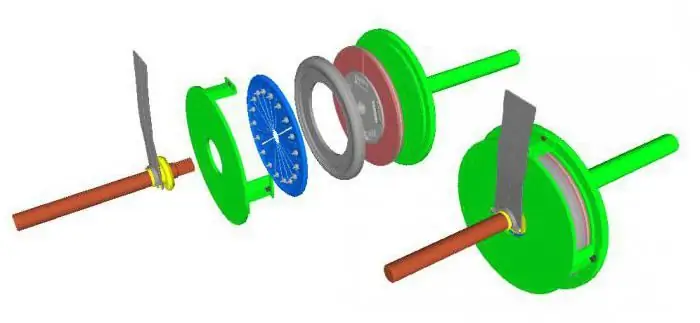
Sprzęgła cierne są używane w mechanizmach sprzęgieł. Urządzenia różnią się parametrami oraz konstrukcją. Istnieje wiele rodzajów sprzęgieł ciernych
Materiały cierne: wybór, wymagania
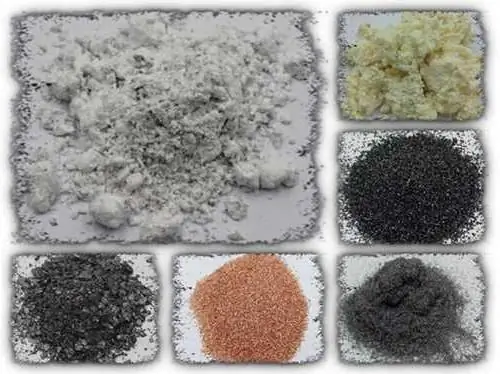
Nowoczesne mechanizmy mają złożoną konstrukcję, duże prędkości. Dlatego używają różnych wysokiej jakości materiałów ciernych. Czym one są, jakie są typy, a także jakie są cechy ich aplikacji, omówiono w artykule
Spawane złącza doczołowe: cechy, rodzaje i technologia
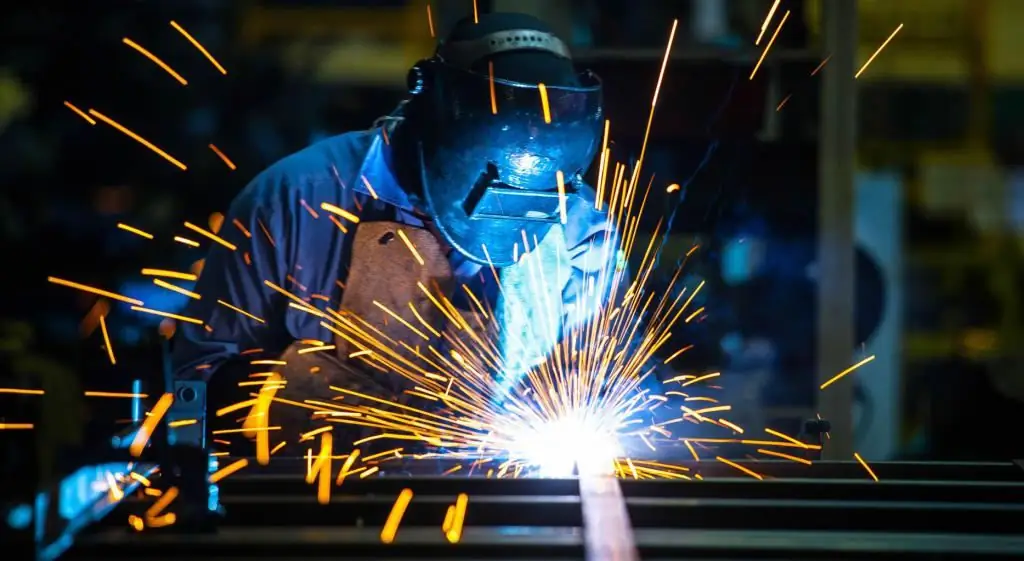
Cechy i rodzaje spawania. Klasyfikacja złączy doczołowych spawanych według różnych parametrów spoiny. Technologia tworzenia złącza doczołowego, w zależności od użytego sprzętu. Środki bezpieczeństwa podczas wykonywania prac spawalniczych
Oznaczanie wytrzymałości betonu: metody, sprzęt, GOST. Kontrola i ocena wytrzymałości betonu
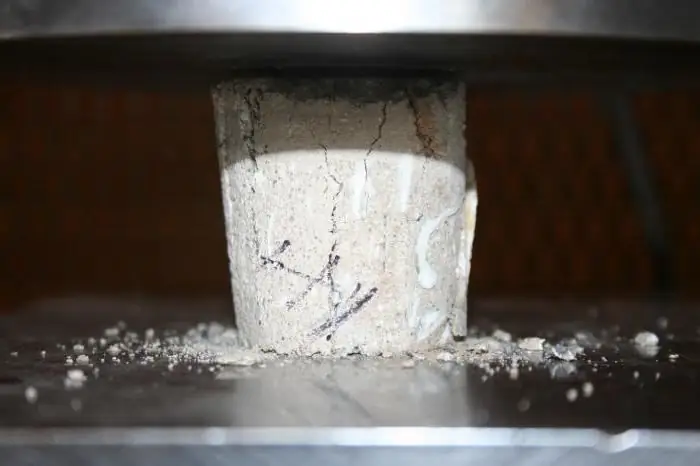
Podczas sprawdzania konstrukcji budowlanych przeprowadza się określenie wytrzymałości betonu w celu określenia ich stanu w chwili obecnej. Rzeczywista wydajność po rozpoczęciu eksploatacji zwykle nie odpowiada parametrom projektowym