2025 Autor: Howard Calhoun | [email protected]. Ostatnio zmodyfikowany: 2025-01-24 13:23
Odlewanie w formach skorupowych jest również nazywane odlewaniem skorupowym. A za granicą ta metoda pracy nazywa się Shell.
Informacje ogólne
W dzisiejszym przemyśle przemysłowym stosuje się wiele różnych metod odlewania. Oprócz odlewania skorupowego stosuje się również odlewanie metodą traconego wosku, a także w formach metalowych i kilka innych metod. Ogólną zaletą tych metod odlewania w porównaniu z formowaniem w piasku jest to, że zapewniają one dokładniejsze materiały końcowe pod względem kształtu i wymiarów. Ponadto zmniejsza się liczba nierówności na powierzchni takich produktów. W rzadszych przypadkach, ale jednak zdarza się, że eliminowana jest konieczność dalszej obróbki po wytopie. Poza tym zastosowanie odlewania w formach skorupowych i innych metod przyczynia się do tego, że proces ten można maksymalnie zmechanizować, w wyniku czego wzrasta również jego automatyzacja. A to oczywiście znacznie zwiększa wydajność każdego obiektu przemysłowego.
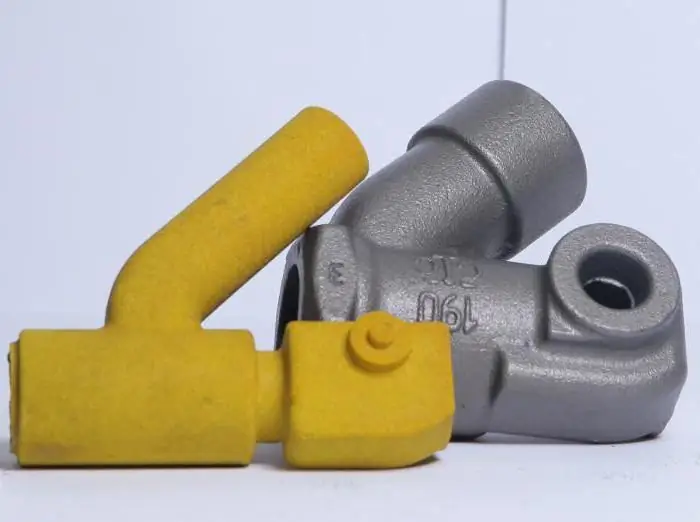
Odlewanie powłoki
Jeśli mówimy o tym konkretniemetoda, po raz pierwszy została wprowadzona w fabrykach w 1953 roku. Obecnie metoda ta jest dość szeroko stosowana. Na przykład odlewanie w formach skorupowych produkuje większość części do ciągnika Kirovets. Wszystkie części produkowane tą metodą są najwyższej jakości ze stali lub żeliwa. Odlewanie muszli to metoda, w której końcowy rezultat odlewania ma kształt składający się z dwóch muszli piaskowo-żywicznych. Również ta metoda wytwarzania części jest stosowana tylko w przypadkach, gdy konieczne jest stworzenie części o małych lub średnich wymiarach, ale jednocześnie z dużą dokładnością. Przykładami zastosowań tej metody odlewania są części silników lub odlewy cienkościenne.
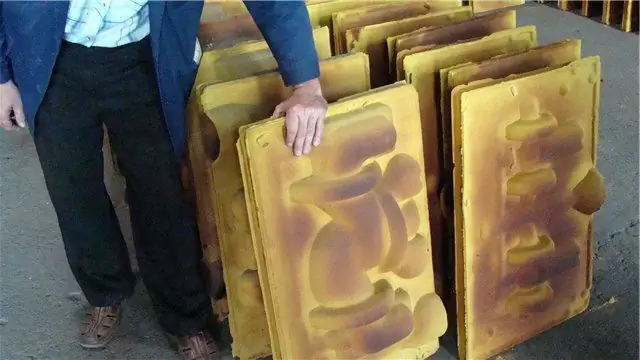
Esencja Drogi
Dzięki tej metodzie pracy możesz uzyskać różne części do wentylatorów, silników, pomp lub maszyn tekstylnych. Jednak maksymalna długość otrzymanego produktu nie może przekraczać 1 metra i nie może być cięższy niż 200 kg.
Istota odlewania do form skorupowych opiera się na pewnych właściwościach żywic termoutwardzalnych, które wchodzą w skład mieszanek piaskowo-żywicznych. Zaletą stosowania takich składników jest to, że żywice te mają tendencję do szybkiego i trwałego twardnienia pod wpływem temperatury 200-250 stopni Celsjusza.
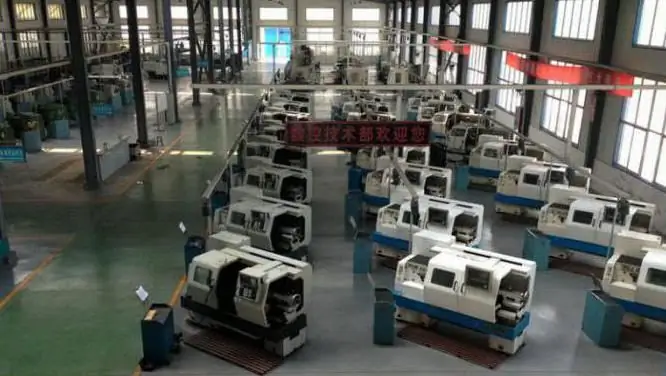
Wykonywanie formy muszli do odlewania
Do wykonania formy do późniejszego odlewania niezbędny jest drobnoziarnisty piasek kwarcowy z dodatkiem żywicy termoutwardzalnej, która jest jej elementem łączącym w celu uzyskania pełnowartościowej formy skorupowej. Materiały te, w szczególności żywica, są wybierane, ponieważ twardnieją po przejściu przez pewną barierę temperaturową. Proces produkcyjny jest następujący. Najpierw żywica jest podgrzewana do 140-160 stopni Celsjusza. Pod wpływem takiego środowiska zamienia się w płynną masę klejącą, która całkowicie otula formę piasku kwarcowego.
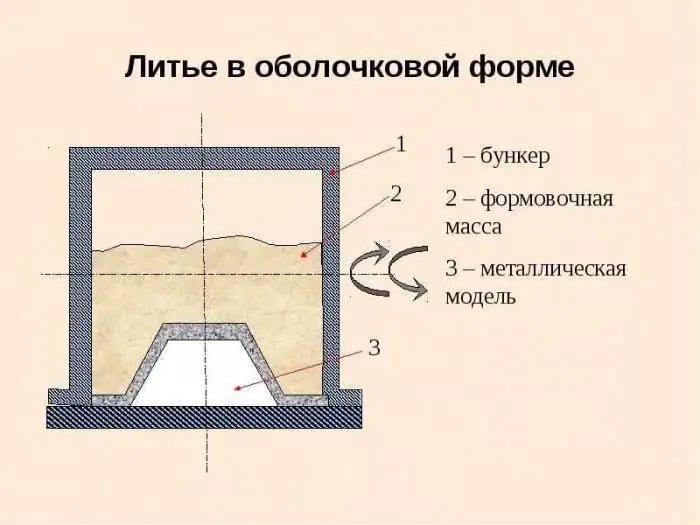
Zakres odlewania w formach skorupowych jest dość szeroki, dlatego też proces wykonywania form jest zautomatyzowany lub zautomatyzowany.
Po całkowitym pokryciu formy żywicą temperatura wzrasta do 200-250 stopni Celsjusza. Ten próg temperatury jest wystarczający, aby masa klejąca nieodwracalnie stwardniała i uformowała się. Ponadto, gdy rozpoczyna się proces odlewania części, to znaczy, gdy stopiony metal wchodzi do formy, temperatura w nim osiąga około 600 stopni. Ten tryb wystarczy, aby żywica nie stopiła się, ale wypaliła, pozostawiając jednocześnie pory na samej formie, ułatwiające uchodzenie gazów.
Zalety i wady odlewania w formach skorupowych
Jak każdy inny proces produkcyjny, ten ma swoje wady i zalety. Jeśli porównamy tę metodę odlewania np. z odlewaniem wzwykłe formy do piasku, ma kilka zalet:
- Pierwszą i dość znaczącą różnicą jest klasa dokładności, która wynosi 7-9. Ponadto poprawia się wykończenie powierzchni uzyskanej części do 3-6. Ponadto zmniejszane są naddatki, które są dozwolone przy późniejszej obróbce powstałej części po odlewaniu.
- Jednym z dużych plusów jest znaczne obniżenie kosztów pracy przy produkcji odlewów.
- Ta metoda odlewania zmniejsza zużycie materiałów do formowania, a także ilość metalu ze względu na fakt, że rozmiar kanałów bramy jest zmniejszony.
- Znacząco zmniejszono ilość wyjścia małżeństwa.
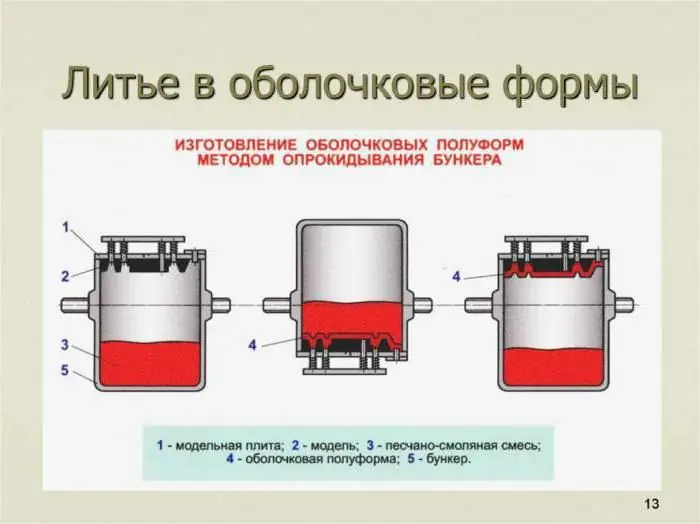
Jednakże są pewne wady odlewania w formach skorupowych. Należą do nich:
- Żywotność formy - 1 odlew.
- Koszt piasku formierskiego jest dość wysoki.
- Wysoki procent szkodliwych gazów.
Proces formowania korpusu
Proces formowania korpusu odbywa się w sześciu etapach:
- Pierwszym krokiem jest wylewanie mieszanki na rozgrzany metalowy model, a także utrzymywanie go przez kilkadziesiąt sekund, aż wokół części utworzy się cienka, mocna skorupa. Najczęściej modele wykonane są z żeliwa, a ich nagrzewanie odbywa się do 230-315 stopni.
- Następnie należy przeprowadzić operację usunięcia nadmiaru masy formierskiej. Grubość skórki powinna docelowo wynosić od 10 do 20mm. Zależy to od czasu przebywania mieszaniny w modelu, a także od temperatury.
- Następnie konieczne jest przeniesienie płyty modelowej wraz z formą do pieca, gdzie będą one znajdować się do końca procesu utwardzania. Pod koniec tej procedury wytrzymałość powłoki powinna wynosić od 2,4 do 3,1 MPa.
- Po wyjęciu z pieca utwardzona skorupa jest odsuwana od płyty. Do tej procedury używany jest specjalny popychacz.
- Następnie dwa lub więcej modeli łączy się ze sobą za pomocą pewnego rodzaju zacisku lub klejenia. Formy te mogą być używane do odlewania w formach skorupowych lub po prostu przechowywane. Prawie nieograniczony okres trwałości.
- Przed rozpoczęciem procesu odlewania w gotowej formie, wlewa się do nich śrut, co pomaga zapobiec lub zniszczyć formę podczas dalszego odlewania.
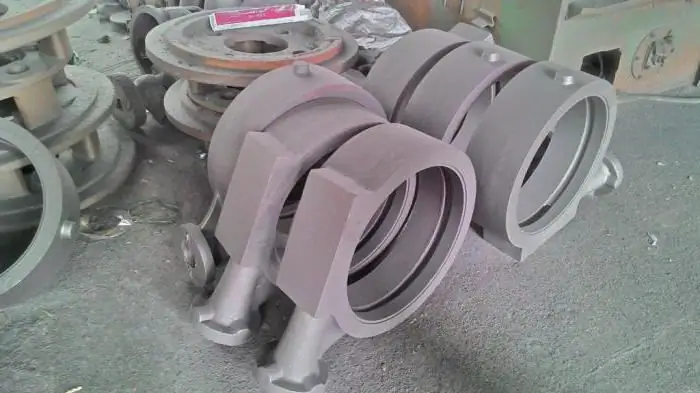
Szczegóły przesyłania
Warto zacząć od tego, że typowe tolerancje, które są dopuszczalne przy wytwarzaniu narzędzi, mogą wynosić 0,5 mm. Chropowatość powierzchni jest dopuszczalna w zakresie od 0,3 do 0,4 mikrona. Takie ograniczenia uzasadnia fakt stosowania piasku drobnoziarnistego. Warto również zwrócić uwagę: zastosowanie żywicy w dużym stopniu przyczynia się do tego, że powierzchnia jest bardzo gładka.
Wielkość produkcji
Aby zająć się produkcją takich form i części, konieczne jest zajęcie się montażem modelu formy. Czas potrzebny na instalację to mniej niż tydzień. Po zakończeniu instalacji ilość wyjściowa możeosiągnąć od 5 do 50 sztuk na godzinę. Takie wielkości produkcji na godzinę są całkiem realne, jednak do tego konieczne jest odpowiednie przygotowanie procesu odlewania. Głównymi materiałami, które będą potrzebne do odlewania, są żeliwo, aluminium, miedź, a także stopy tego rodzaju metali. Kolejnym niezbędnym materiałem będzie stop wykorzystujący aluminium i magnez.
Zalecana:
Strategie Portera: podstawowe strategie, podstawowe zasady, cechy
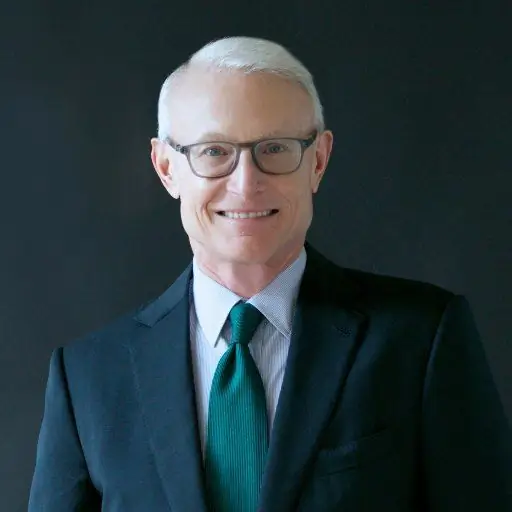
Michael Porter jest uznanym ekonomistą, konsultantem, badaczem, nauczycielem, wykładowcą i autorem wielu książek. którzy opracowali własne strategie konkurencji. Uwzględniają wielkość rynku i cechy przewag konkurencyjnych. Strategie te są szczegółowo opisane w artykule
Tradycyjne i alternatywne sposoby wytwarzania energii elektrycznej
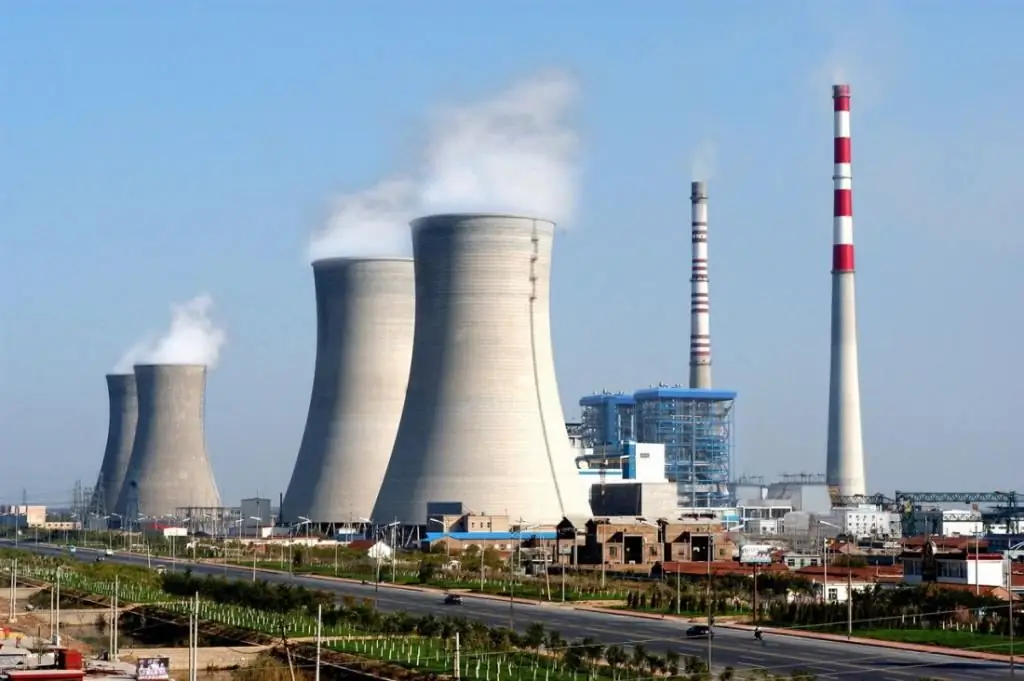
Obecnie ludzkość wykorzystuje wszystkie możliwe sposoby wytwarzania elektryczności. Trudno przecenić wagę tego zasobu. Co więcej, zużycie energii elektrycznej rośnie z każdym dniem. Z tego powodu coraz więcej uwagi poświęca się nietradycyjnym sposobom wytwarzania energii elektrycznej. Jednocześnie źródła te na tym etapie rozwoju nie mogą w pełni zaspokoić potrzeb ludności Ziemi. W tym artykule pokrótce omówiono główne tradycyjne i alternatywne metody pozyskiwania energii elektrycznej
Co to jest środek osuszający - opis, metoda wytwarzania i cechy
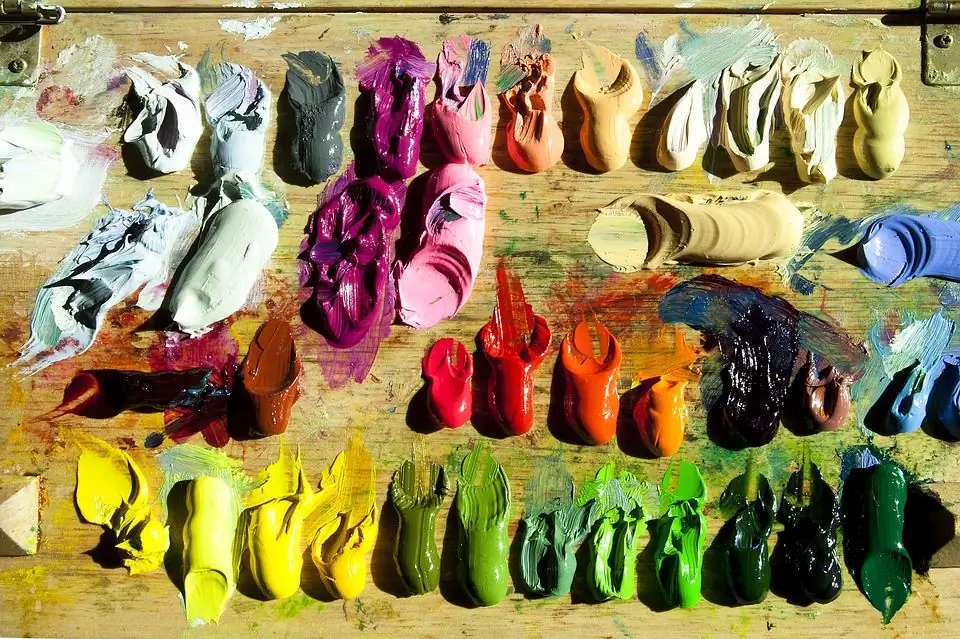
Czas potrzebny do wyschnięcia warstwy farby, na przykład podczas malowania portretu, zależy od ciepła, światła i rodzaju oleju. Istnieją specjalne składniki katalityczne, które po dodaniu do oleju przyspieszają czas schnięcia. Nazywają się suszarkami lub środkiem osuszającym, co to jest? Tak nazywają się substancje specjalne, do których należą sole różnych metali – kob alt, ołów, mangan
Bank komercyjny. Funkcje i podstawowe operacje
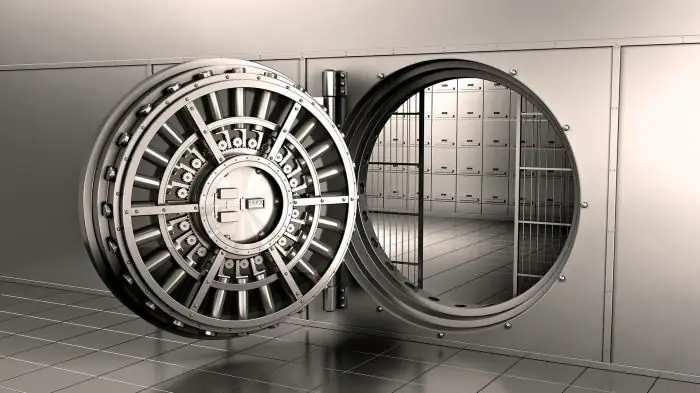
Ważnym ogniwem w systemie bankowym jest bank komercyjny. Funkcje i główne działania tej organizacji mają na celu uzyskanie maksymalnej kwoty zysku
Odlewanie w formie silikonowej: sprzęt. Odlewanie próżniowe w formach silikonowych
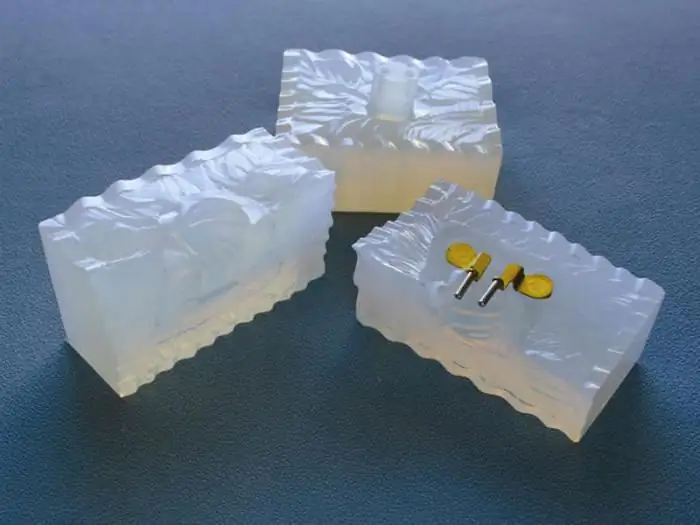
Do produkcji niewielkiej liczby wykrojów z tworzywa sztucznego najczęściej stosuje się odlewanie próżniowe do form silikonowych. Ta metoda jest dość ekonomiczna (wykonanie metalowej formy wymaga więcej czasu i pieniędzy). Ponadto formy silikonowe są wykorzystywane wielokrotnie, co również znacznie obniża koszty produkcji