2025 Autor: Howard Calhoun | [email protected]. Ostatnio zmodyfikowany: 2025-06-01 07:14
Jednostki do opóźnionego koksowania są najczęstszym rozwiązaniem sprzętowym do rafinacji ciężkiego oleju. Ich urządzenie składa się z 2 głównych modułów - reaktora, w którym surowiec jest podgrzewany i koksowany oraz obróbki mechanicznej. Projektowanie instalacji odbywa się etapami i obejmuje obliczenia i dobór wyposażenia technologicznego, określenie wskaźników techniczno-ekonomicznych.
Miejsce docelowe
Technologiczny proces koksowania jest jednym ze sposobów rafinacji ropy naftowej. Jego głównym celem jest pozyskiwanie gruboziarnistego koksu naftowego. W przemyśle stosowane są 3 metody koksowania:
- Okresowo, w kostkach. Surowiec jest ładowany do poziomego aparatu, ogrzewany paleniskiem pod nim, a następnie kalcynowany przez 2-3 godziny. Następnie piec jest schładzany, a gotowy produkt rozładowywany. Ta metoda jest najprostsza i najmniej wydajna.
- Ciągły. Ta metoda jest wciąż na etapie rozwoju przemysłowego.
- Półciągły, aktualnie odbieranynajbardziej rozpowszechniony.
Ultra opóźnione jednostki koksownicze to najnowszy typ wyposażenia procesowego. W nich surowiec jest wstępnie podgrzewany w piecu, a następnie przenoszony do nieogrzewanych komór reakcyjnych, które posiadają warstwę termoizolacyjną dla utrzymania wymaganej temperatury. Ilość i wielkość reaktorów, moc pieców wpływa na wydajność całej instalacji.
Praca pierwszego DCU w Rosji rozpoczęła się w 1965 roku w Ufaneftekhim. Opóźniona koksownia zakładu działa do dziś. Po odbudowie w 2007 r. jej wydajność wynosi około 700-750 tys. ton/rok w przeliczeniu na masę przerabianych surowców.
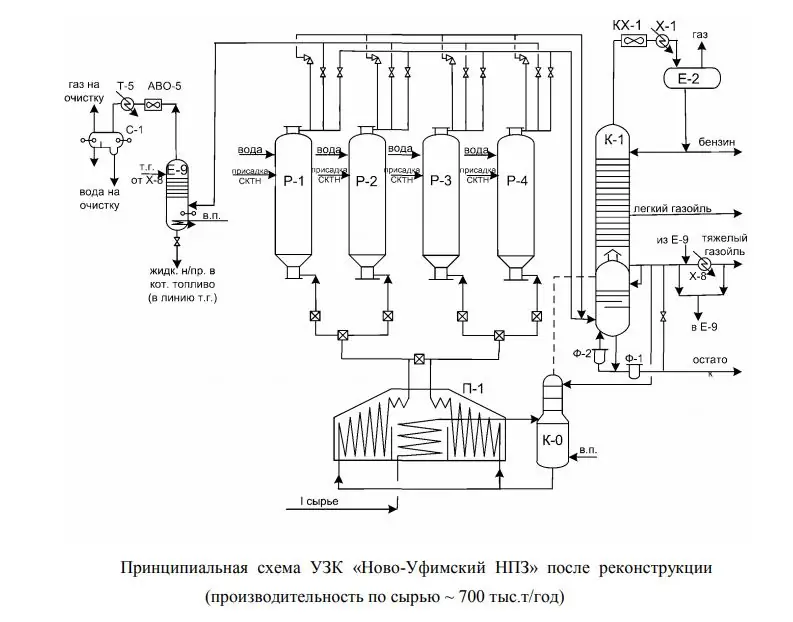
Produkty końcowe
Następujące substancje są otrzymywane podczas badań ultradźwiękowych, z wyjątkiem koksu:
- gazy koksownicze (stosowane jako paliwo technologiczne lub przetwarzane w celu uzyskania frakcji propan-butan);
- benzyna;
- destylaty koksu (paliwo, kraking).
Na domowych maszynach ultradźwiękowych wydajność koksu wynosi 20-30% wagowo. Wskaźnik ten zależy przede wszystkim od jakości surowców. Największe zapotrzebowanie na ten produkt odczuwa przemysł metalurgiczny (produkcja anod i elektrod, aluminium, materiały ścierne, węgliki, materiały węglowo-grafitowe, żelazostopy). Oprócz pierwszego DCU Ufa, w Rosji zbudowano również inne jednostki opóźnionego koksowania: w rafinerii Omsk, rafinerii Nowokujbyszewsk, LLC LUKOIL-Volgogradneftepererabotka, LUKOIL-Permnefteorgsintez, LUKOIL-Permnefteorgsintez, w Angarsk Petrochemical Company, NOVOIL OJSC (Ufa), TANECO PJSC (Niżnekamsk).
Surowce
Materiały spożywcze do koksowania dzielą się na 2 grupy: produkty przetwarzania pierwotnego i wtórnego. Następujące substancje są używane jako surowce w jednostkach opóźnionego koksowania:
- olej opałowy;
- pół smoły;
- tar;
- smoła węglowa;
- asf alt i inne przemysłowe produkty naftowe;
- ciekły osad węglowy;
- ciężka piroliza i smoła łupkowa;
- pozostałości z krakingu termicznego;
- bitum naftowy i oleje ciężkie.
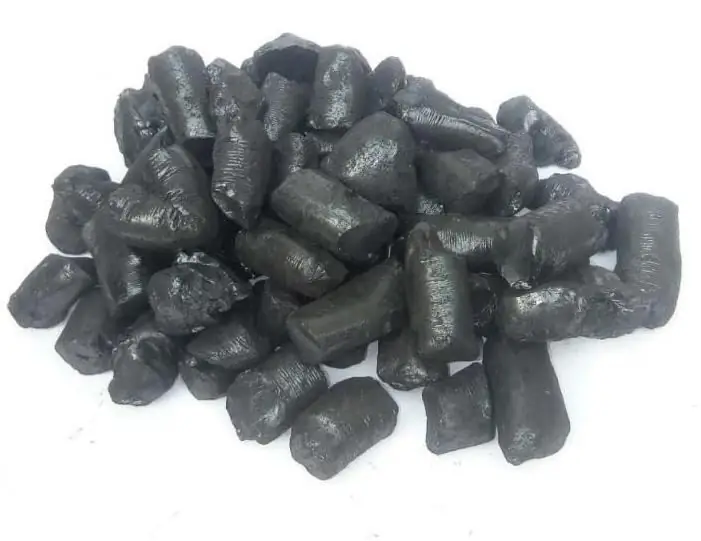
Wysoce aromatyzowane pozostałości oleju są obecnie najpowszechniejszym surowcem.
Wpływ na parametry technologiczne
Następujące parametry koksowni zależą od właściwości materiałów paszowych:
- wydajność komory reakcyjnej;
- jakość otrzymanych produktów;
- wylot koksu;
- warunki procesu.
Najważniejszymi parametrami surowców są:
- Koksowanie, w zależności od zawartości substancji asf altowo-żywicznych. Wartość koksowania powinna mieścić się w zakresie 10-20%. Przy mniejszej wartości spada uzysk koksu, przy większej osady gromadzą się wewnątrz wężownic w piecach. Zdolność koksowania jest określona przez masę stałej pozostałości w tyglu po podgrzaniu znajdującej się w nim próbki produktu naftowego.
- Gęstość.
- Skład chemiczny. ZSzkodliwe zanieczyszczenia, które mają największy wpływ na jakość koksu, emitują siarkę (powinna być nie więcej niż 1,5% wagowo). W zależności od przeznaczenia koksu w procesie technologicznym, preferowane jest stosowanie różnych rodzajów surowców. Tak więc, aby uzyskać włóknistą strukturę produktu końcowego, stosuje się materiały na bazie parafiny.
Uzysk koksu jest proporcjonalny do gęstości paszy i zawartości asf altenów.
Etapy koksowania
Proces technologiczny w jednostkach opóźnionego koksowania jest długi i ciągły, od dostawy surowców do rozładunku gotowego produktu. Konwencjonalnie dzieli się na 3 etapy:
- Reakcje rozkładu, tworzenie frakcji destylacyjnych, produkty pośrednie, kondensacja.
- Znaczne zmniejszenie zawartości nienasyconych węglowodorów w gazach, wzrost masy cząsteczkowej składników pozostałości, reakcje cyklizacji.
- Wzrost zawartości asf altenów w pozostałości do 26%, redukcja ilości żywic i olejów. Przekształć płynną pozostałość w stały koks.
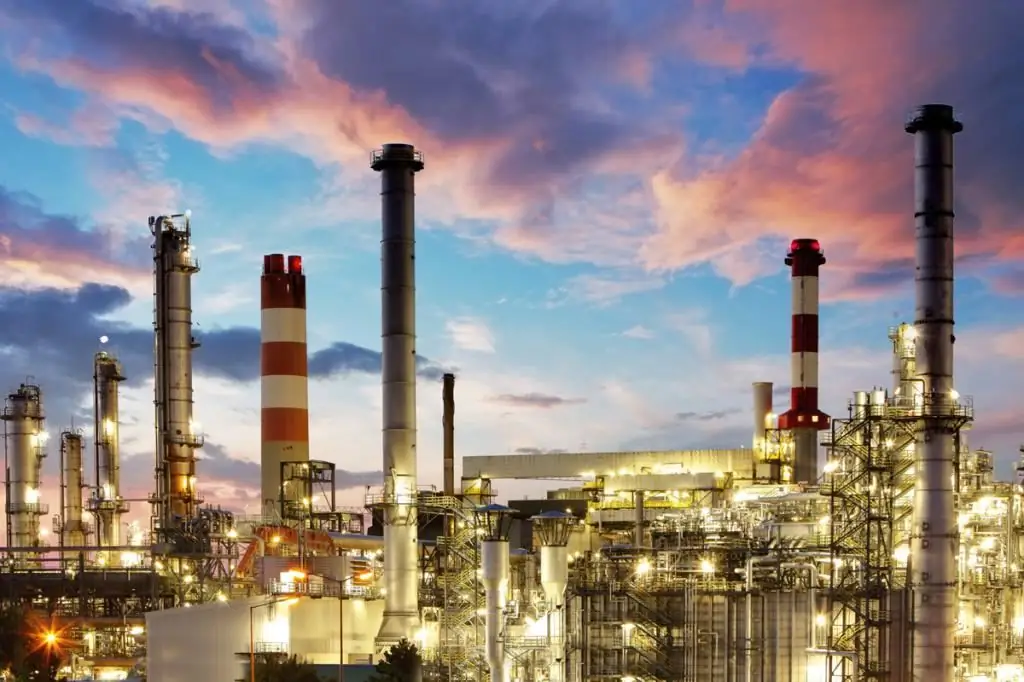
Klasyfikacja
Istnieją 2 główne typy jednostek opóźnionego koksowania zgodnie z ich układem: jednoblokowe i dwublokowe.
Wśród instalacji dwublokowych istnieją 4 typy, które charakteryzują się następującymi cechami konstrukcyjnymi i technologicznymi:
- Wewnętrzna średnica komór koksowniczych - 4,6 m. Namiotowe piece grzewcze, cztery komory pracujące parami. Do ogrzewania wykorzystuje się naftę i olej napędowy otrzymywane w procesie koksowania.
- Kokskomory Ø 5,5 m. Surowiec - oleje opałowe z destylacji z wprowadzeniem wysokoaromatycznych węglowodorów, które zwiększają uzysk produktu wysokiej jakości.
- Reaktory ze stali stopowej Ø 5,5 m, wysokość 27,6 m, piece rurowe z palnikiem wolumetrycznym, zawory górne o zwiększonym przekroju, wskaźniki poziomu radioaktywnego umożliwiające rejestrację miejsca separacji fazy koksowo-pianowej. Najnowsza innowacja pomaga lepiej wykorzystać użyteczną objętość reaktora. Dostawa turbulatorów z dodatkami detergentowymi zmniejszającymi koksowanie wężownic, chłodzony olej gazowy w głowicach.
- Komory reakcyjne Ø 7 m, wysokość 29,3 m. Osiowe wprowadzanie surowca do reaktorów, układ hydrauliczny do wyładunku koksu ze zdalnym sterowaniem, dźwigi elektryczne, magazyny z magazynami typu piętrowego.
Sprzęt stosowany
Sprzęt wyposażony w instalacje tego typu dzieli się na następujące grupy w zależności od przeznaczenia:
- Technologiczne, bezpośrednio zaangażowane w proces koksowania (piece, wyposażenie kolumn, wymienniki ciepła, komory reaktorów, kostki, lodówki, pompy, rurociągi, oprzyrządowanie, krany i inne zawory odcinające i przełączające).
- Ścieki - gromadzenie i uzdatnianie wody w celu powrotu do cyklu roboczego (chłodzenie i ekstrakcja koksu).
- Sprzęt do rozładunku koksu z komór (kostek). W nowoczesnych instalacjach zmechanizowanych może być typu mechanicznego i hydraulicznego (zawiesia, wciągarki, grzebienie, przecinaki, pręty, wieże, tuleje gumowe).
- Urządzenia do transportu i obróbki gotowego produktu (zsypy i rampy odbiorcze, dźwigi, przenośniki, podajniki, kruszarki, magazyny).
- Maszyny i urządzenia do mechanizacji pracy.
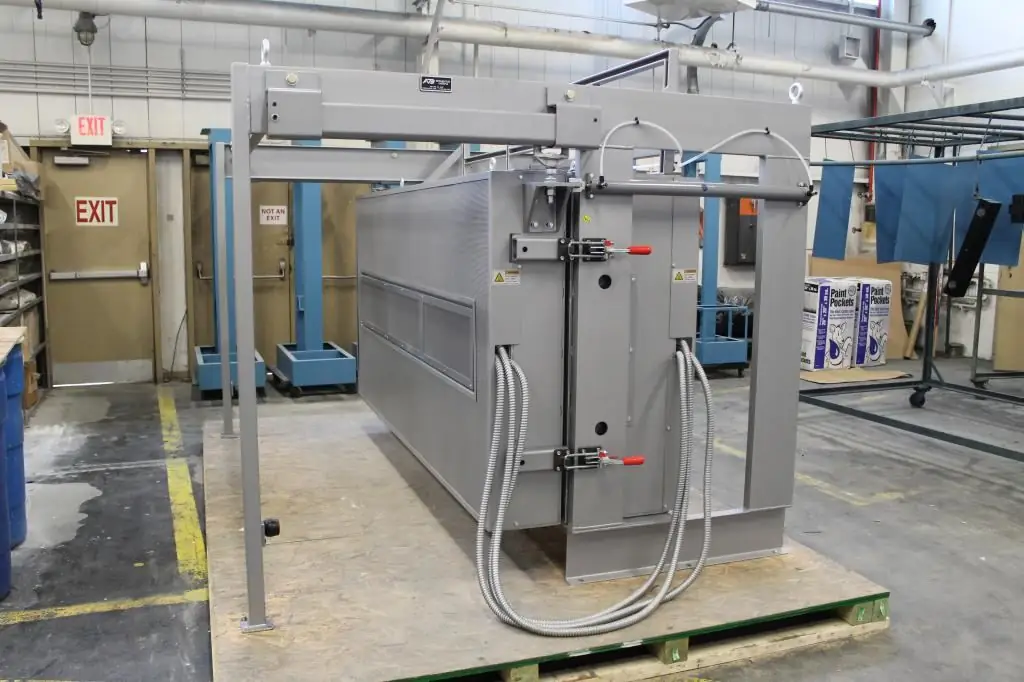
Projektując opóźnione koksownie należy dokładnie przemyśleć konstrukcję komór reakcyjnych i pieców, ponieważ czas trwania cyklu pracy zależy od niezawodności ich działania.
Parametry procesu
Główne parametry technologii koksowania to:
- Wskaźnik recyrkulacji, zdefiniowany jako stosunek całkowitego obciążenia cewek reakcyjnych pieców do obciążenia całej instalacji pod względem surowców. Wraz ze wzrostem jego wartości rośnie uzysk wysokiej jakości koksu, gazu i benzyny, natomiast spada ilość ciężkiego oleju napędowego.
- Ciśnienie w komorze reakcyjnej. Jej zmniejszenie prowadzi do wzrostu uzysku oleju napędowego, spadku uzysku koksu i gazu oraz wzrostu pienienia.
- Temperatura procesu. Im jest większy, tym wyższa jakość koksu pod względem ilości substancji lotnych, jego wytrzymałości i gęstości. Wartość maksymalna ograniczona jest ryzykiem zakoksowania pieca i rurociągów, co zmniejsza trwałość wężownic. Każdy rodzaj surowca ma swoją optymalną temperaturę.
Budowa instalacji opóźnionego koksowania wiąże się z wysokimi kosztami kapitałowymi. Dlatego najczęściej przeprowadzana jest przebudowa już funkcjonującego kompleksu urządzeń. Osiąga się to poprzez skrócenie cyklukoksowanie, wprowadzenie nowych komór reakcyjnych lub zmniejszenie stopnia recyrkulacji.
Zasada działania
Jednostki opóźnionego koksowania składają się z jednej lub więcej sparowanych grup komór, w których jedna komora pracuje na etapie produkcji koksu, a druga na rozładunku lub w stanie pośrednim. Proces rozkładu materiału wyjściowego rozpoczyna się w piecu rurowym, gdzie jest podgrzewany do 470-510°C. Następnie surowiec trafia do nieogrzewanych komór, gdzie jest głęboko zakoksowany pod wpływem ciepła, które mu towarzyszyło.
Gazowe i ciekłe węglowodory są odprowadzane do frakcjonowanej separacji w kolumnie destylacyjnej. Koks trafia do działu obróbki mechanicznej, gdzie jest rozładowywany, sortowany i transportowany. W warstwie gotowego produktu wierci się studnię i umieszcza się w niej przecinak hydrauliczny. Jego dysze pracują pod ciśnieniem do 20 MPa. Kawałki oddzielonego koksu spadają na platformę drenażową, z której odprowadzana jest woda. Produkt jest następnie kruszony na mniejsze kawałki i rozdzielany na frakcje. Następnie koks trafia do magazynu.
Główny schemat badania ultradźwiękowego pokazano na poniższym rysunku.
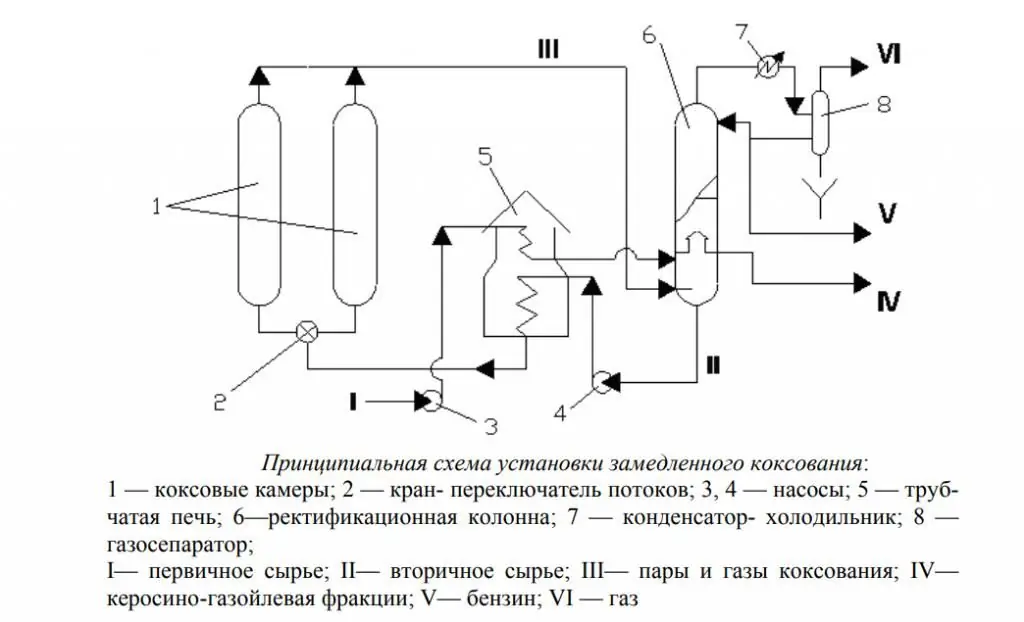
Komory koksownicze
Komory są reaktorem, który jest podstawą całej instalacji. Cykl pracy komory to zwykle 48 godzin, jednak w ostatnich latach zaprojektowano urządzenia ultradźwiękowe pracujące w trybach 18- i 36-godzinnych.
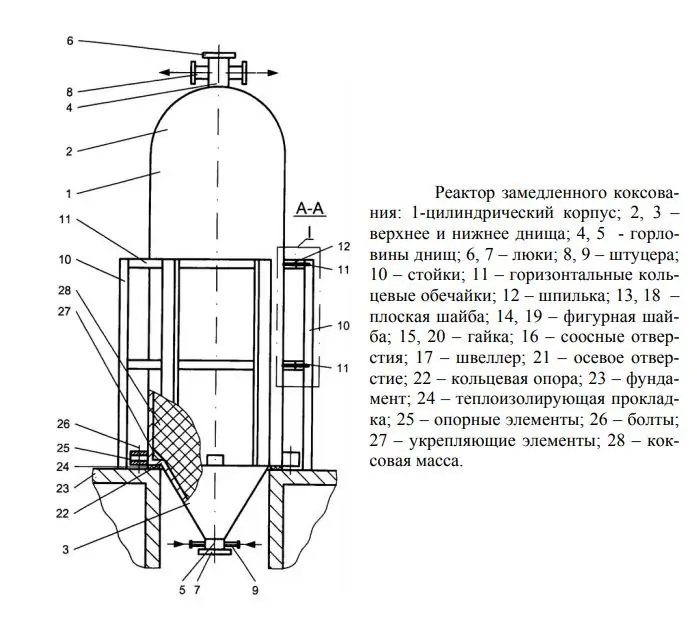
Jeden cykl pracy reaktora składa się z następujących operacji:
- ładowanie surowców, proces koksowania (1 dzień);
- wyłączone (1/2 godziny);
- obróbka hydrotermalna (2,5 godziny);
- Chłodzenie produktu wodą, usuwanie wody (4 godziny);
- rozładuj produkt (5 godzin);
- uszczelnianie włazów, próby ciśnieniowe gorącą parą (2 godziny);
- ogrzewanie oparami oleju, przejście do cyklu pracy (3 godziny).
Projekt
Projekt jednostki opóźnionego koksowania jest rozwijany w następującej kolejności:
- określenie wymaganej wydajności, t/rok;
- analiza bazy zasobów;
- sporządzanie teoretycznego bilansu materiałowego procesu koksowania dla różnych rodzajów surowców;
- określenie głównych przepływów materiałów;
- opracowanie koncepcji instalacji;
- uzasadnienie wielkości i liczby reaktorów;
- określenie czasu napełniania jednej komory koksem i jego obliczenia hydrauliczne, opracowanie harmonogramu pracy reaktora;
- obliczenia obciążenia temperaturowego komory;
- obliczanie komór konwekcyjnych i radiacyjnych;
- opracowanie układu linii produkcyjnej;
- obliczenia technologiczne innych głównych urządzeń (kolumna destylacyjna, piece, lodówki itp.);
- opracowanie systemu monitoringu i sterowania, wybór narzędzi automatyzacji;
- opis systemów ochrony awaryjnej;
- rozwój aspektów środowiskowych i środków bezpieczeństwa;
- określenie wskaźników ekonomicznych (koszty kapitałowe, liczba pracowników obsługi, płace,koszty produkcji surowców i materiałów pomocniczych, roczny efekt ekonomiczny, kosztorysowanie produktu).
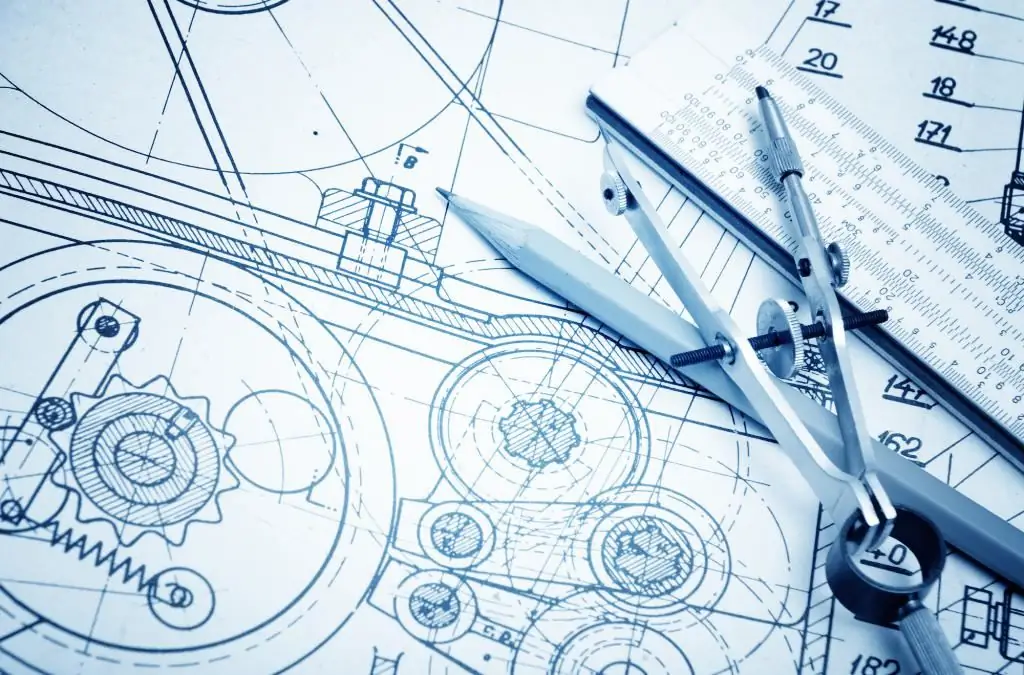
Obliczanie wydajności instalacji opóźnionego koksowania w ujęciu rocznym odbywa się według wzoru:
N=P x t, gdzie P jest wydajnością zakładu, t/dzień;
t to liczba dni roboczych w roku.
Wydajność produktu w kategoriach fizycznych zgodnie z opcjami podstawowymi i projektowymi jest określana na podstawie bilansu materiałowego instalacji.
Zalecana:
Obliczanie wakacji: wzór, przykład. Obliczanie urlopu rodzicielskiego
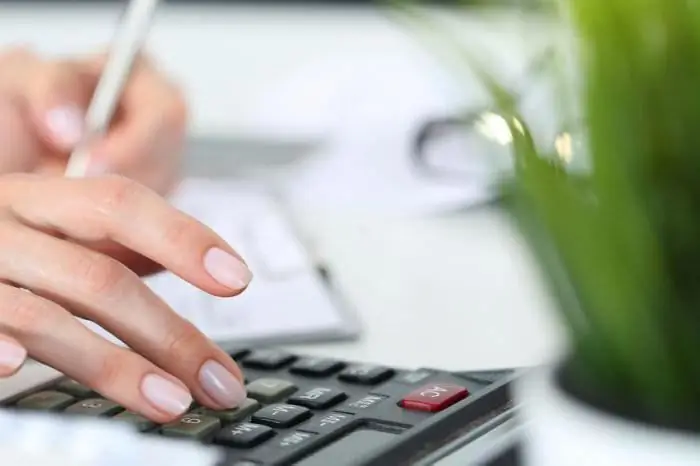
W ramach tego artykułu rozważymy podstawowe zasady obliczania wynagrodzenia urlopowego dla pracownika, w tym w różnych interpretacjach: na urlopie macierzyńskim, na opiekę nad dzieckiem, po zwolnieniu, a także za szkodliwe warunki pracy
Lokomotywa elektryczna 2ES6: historia powstania, opis ze zdjęciem, główne cechy, zasada działania, cechy działania i naprawy
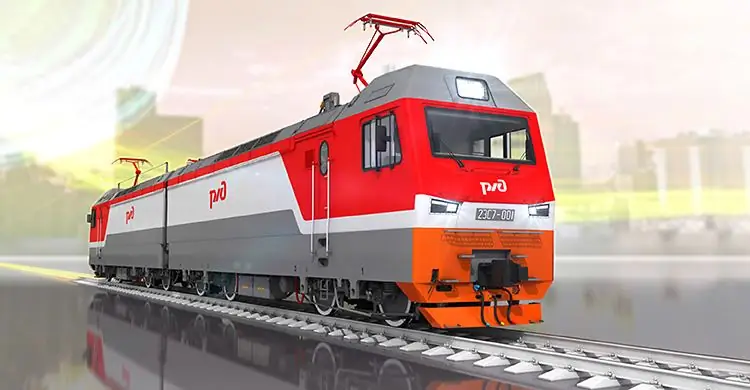
Dziś komunikacja między różnymi miastami, transport pasażerski, dostawa towarów odbywa się na różne sposoby. Jednym z tych sposobów była kolej. Lokomotywa elektryczna 2ES6 to jeden z obecnie aktywnie wykorzystywanych rodzajów transportu
Co to jest moc bierna? Kompensacja mocy biernej. Obliczanie mocy biernej
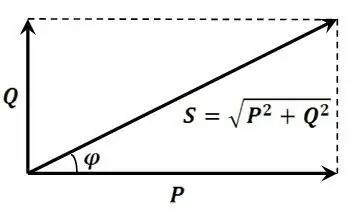
W rzeczywistych warunkach produkcyjnych dominuje moc bierna o charakterze indukcyjnym. Przedsiębiorstwa instalują nie jeden licznik elektryczny, ale dwa, z których jeden jest aktywny. A za nadmierne wydatki na energię „gonioną” na próżno liniami energetycznymi, odpowiednie władze są bezlitośnie karane grzywnami
Sieć trójfazowa: obliczanie mocy, schemat połączeń
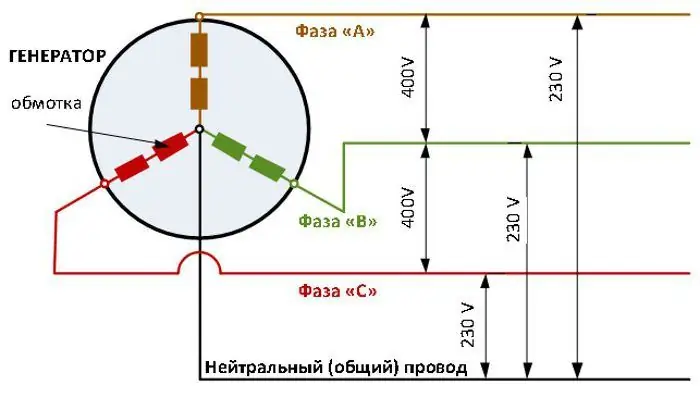
Właściwie zaprojektowana i konserwowana sieć trójfazowa jest idealna dla prywatnego domu. Umożliwia równomierne rozłożenie obciążenia na fazy i podłączenie dodatkowych odbiorników energii, jeśli pozwala na to sekcja okablowania
Grzejniki niskociśnieniowe: definicja, zasada działania, parametry techniczne, klasyfikacja, konstrukcja, cechy działania, zastosowanie w przemyśle
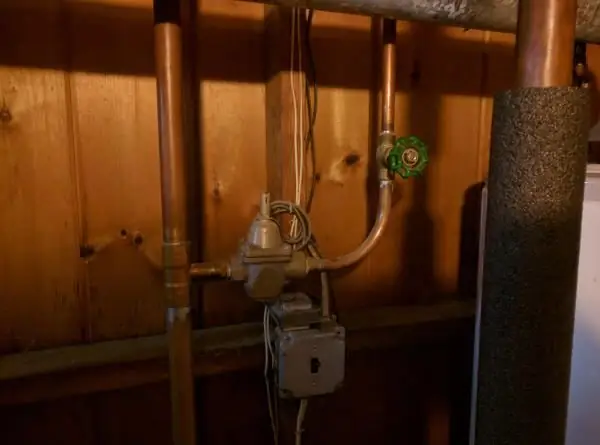
Grzejniki niskociśnieniowe (LPH) są obecnie używane dość aktywnie. Istnieją dwa główne typy, które są produkowane przez różne zakłady montażowe. Oczywiście różnią się również charakterystyką działania