2025 Autor: Howard Calhoun | [email protected]. Ostatnio zmodyfikowany: 2025-06-01 07:14
W przemyśle wytwórczym i budowlanym badania nieniszczące są jedną z najpopularniejszych metod diagnozowania materiałów. Korzystając z tej metody, budowniczowie oceniają jakość połączeń spawanych, sprawdzają gęstość w niektórych odcinkach konstrukcji, ujawniając głębokie wady i wady. Diagnostyczne defektoskopy magnetyczne mogą wykrywać zarówno uszkodzenia powierzchniowe, jak i podpowierzchniowe z dużą dokładnością.
Urządzenie
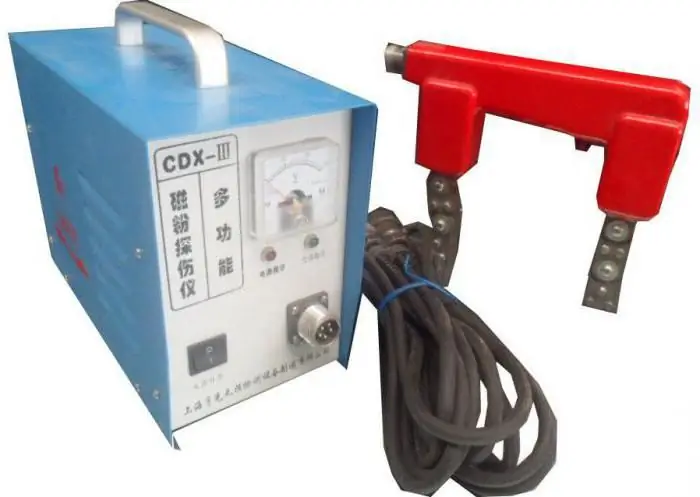
Podstawą segmentu grubościomierzy i defektoskopów magnetycznych są urządzenia ręczne wyposażone w magnesowalne korpusy robocze - najczęściej w postaci cęgów. Zewnętrznie są to niewielkie urządzenia, których wypełnienie stanowi elektromagnes regulujący bieguny działania fali. Klasa średnia pozwala na pracę z przenikalnością magnetyczną, której współczynnik jest wyższy niż 40. Korpus zaopatrzony jest w ergonomiczny uchwyt, dzięki któremu urządzenie może być używane w trudno dostępnych miejscach. Aby dostarczyć prąd elektryczny, przyrządy są również wyposażone w kabel podłączony do stacji generatora (jeśli praca jest wykonywana na zewnątrz) lub do domowej sieci elektrycznej 220 V. Bardziej wyrafinowany sprzęt do badań nieniszczącychposiada stacjonarną bazę podłączoną do komputera. Takie narzędzia diagnostyczne są coraz częściej wykorzystywane do sprawdzania jakości produkowanych części w produkcji. Przeprowadzają kontrolę jakości, ustalając najmniejsze odchylenia od standardowych wskaźników.
Defektoskopy z ferrosondą
Różnorodność urządzeń magnetycznych przeznaczonych do wykrywania defektów na głębokości do 10 mm. W szczególności służą do naprawy nieciągłości w strukturze konstrukcji i części. Mogą to być zachody słońca, muszle, pęknięcia i linie włosów. Do oceny jakości spoin stosowana jest również metoda fluxgate. Po zakończeniu sesji roboczej defektoskopy magnetyczne tego typu mogą również określić poziom rozmagnesowania części w ramach kompleksowej diagnostyki. Pod względem zastosowania do części o różnych kształtach i rozmiarach urządzenia praktycznie nie mają ograniczeń. Ale znowu nie należy zapominać o maksymalnej głębokości analizy konstrukcji.
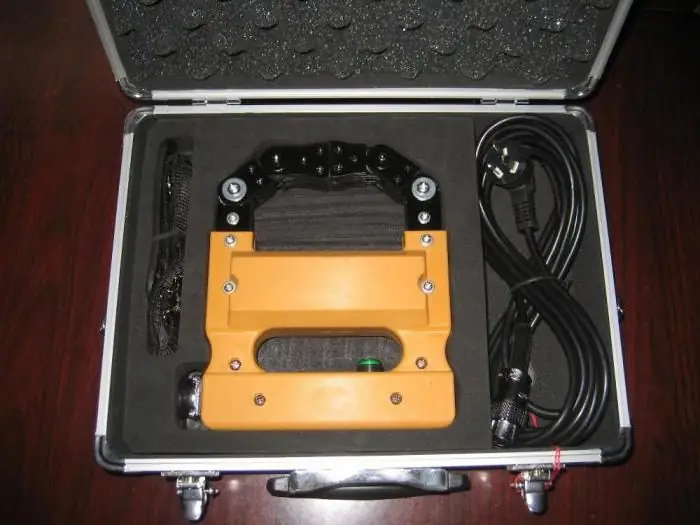
Defektoskopy magnetyczne i wiroprądowe
Za pomocą urządzeń magnetograficznych operator może wykryć wady produktu na głębokości od 1 do 18 mm. I znowu, docelowymi oznakami odchyleń w konstrukcji są nieciągłości i wady połączeń spawanych. Do cech techniki badań wiroprądowych należy analiza oddziaływania pola elektromagnetycznego z falami generowanymi przez prądy wirowe, które są podawane na przedmiot kontroli. Najczęściej defektoskop wiroprądowy służy do badania produktów wykonanych z materiałów przewodzących prąd elektryczny. Urządzenia tego typuwykazują bardzo dokładny wynik podczas analizy części o aktywnych właściwościach elektrofizycznych, ale ważne jest, aby wziąć pod uwagę, że pracują na małej głębokości - nie większej niż 2 mm. Co do charakteru defektów, metoda prądów wirowych umożliwia wykrycie nieciągłości i pęknięć.
Defektoskopy cząstek magnetycznych
Takie urządzenia skupiają się również głównie na wadach powierzchniowych, które można naprawić na głębokości do 1,5-2 mm. Jednocześnie możliwość badań pozwala na ujawnienie szerokiego zakresu wad - od parametrów zgrzewu po wykrycie śladów rozwarstwień i mikropęknięć. Zasada działania takiego sprzętu do badań nieniszczących opiera się na działaniu cząstek proszku. Pod wpływem prądu elektrycznego są one skierowane w kierunku niejednorodności drgań magnetycznych. Pozwala to naprawić niedoskonałości powierzchni docelowego obiektu badań.
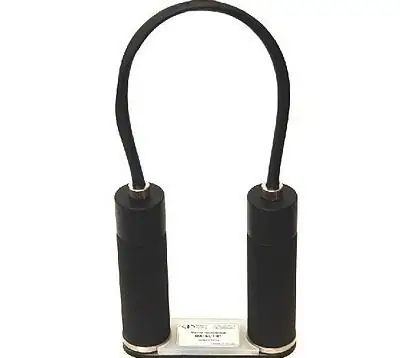
Najwyższa dokładność w określaniu uszkodzonych obszarów tą metodą będzie zapewniona, jeśli płaszczyzna uszkodzonego obszaru tworzy kąt 90 stopni z kierunkiem strumienia magnetycznego. Gdy odbiegamy od tego kąta, zmniejsza się również czułość instrumentu. W procesie pracy z takimi urządzeniami wykorzystywane są również dodatkowe narzędzia do naprawy parametrów defektów. Na przykład defektoskop magnetyczny „Magest 01” w podstawowej konfiguracji jest wyposażony w podwójną lupę i latarkę ultrafioletową. Oznacza to, że operator przeprowadza bezpośrednie określenie skazy na powierzchni przez kontrolę wzrokową.
Przygotowanie do pracy
Zajęcia przygotowawcze można podzielić na dwie grupy. Pierwszy będzie obejmował bezpośrednie przygotowanie powierzchni roboczej, a drugi - ustawienie urządzenia. Jeśli chodzi o pierwszą część, część należy oczyścić z rdzy, różnego rodzaju smarów, plam olejowych, brudu i kurzu. Wynik wysokiej jakości można uzyskać tylko na czystej i suchej powierzchni. Następnie ustawiany jest defektoskop, w którym kluczowym etapem będzie kalibracja z weryfikacją względem standardów. Te ostatnie to próbki materiałów z defektami, które można wykorzystać do oceny poprawności wyników analizy urządzenia. Ponadto, w zależności od modelu, można ustalić zakres głębokości roboczej i czułość. Wskaźniki te zależą od zadań wykrywania defektów, właściwości badanego materiału oraz możliwości samego urządzenia. Nowoczesne, zaawansowane technologicznie defektoskopy umożliwiają również automatyczną regulację zgodnie z określonymi parametrami.
Namagnesowanie części
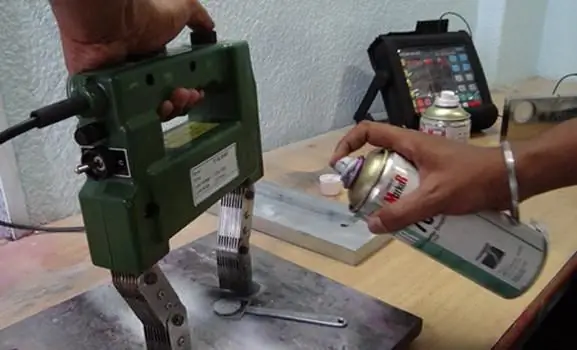
Pierwszy etap operacji roboczych, podczas którego następuje namagnesowanie badanego obiektu. Początkowo ważne jest prawidłowe określenie kierunku przepływu i rodzaju namagnesowania parametrami czułości. Na przykład metoda proszkowa pozwala na wykonanie uderzeń słupowych, kołowych i kombinowanych na część. W szczególności magnesowanie kołowe odbywa się poprzez przepuszczanie prądu elektrycznego bezpośrednio przez produkt, przez główny przewodnik, przez uzwojenie lub przez oddzielny odcinek elementu z podłączeniem styczników elektrycznych. WW trybie działania biegunowego defektoskopy magnetyczne zapewniają namagnesowanie za pomocą cewek, w medium solenoidowym, za pomocą przenośnego elektromagnesu lub za pomocą magnesów trwałych. Odpowiednio, metoda łączona pozwala na połączenie dwóch metod poprzez podłączenie dodatkowego wyposażenia w procesie magnesowania przedmiotu obrabianego.
Zastosowanie wskaźnika magnetycznego
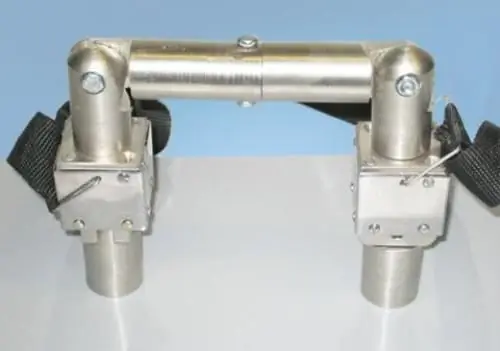
Materiał wskaźnikowy jest nakładany na wstępnie przygotowaną i namagnesowaną powierzchnię. Pozwala zidentyfikować wady części pod wpływem pola elektromagnetycznego. Zostało już powiedziane, że w tym charakterze można stosować proszki, ale niektóre modele działają również z zawiesinami. W obu przypadkach przed przystąpieniem do pracy należy wziąć pod uwagę optymalne warunki użytkowania urządzenia. Np. defektoskop magnetyczny „MD-6” zaleca się stosować w temperaturach od -40 do 50 °C i przy wilgotności powietrza do 98%. Jeśli warunki spełniają wymagania dotyczące działania, możesz rozpocząć stosowanie wskaźnika. Puder nakłada się na całą powierzchnię - dzięki czemu zapewnione jest również niewielkie pokrycie obszarów nieprzeznaczonych do nauki. Zapewni to dokładniejszy obraz wady. Zawiesinę nanosi się strumieniem za pomocą węża lub aerozolu. Istnieją również metody zanurzania części w pojemniku z mieszanką wskaźnika magnetycznego. Następnie możesz przejść bezpośrednio do rozwiązywania problemów z produktem.
Kontrola części
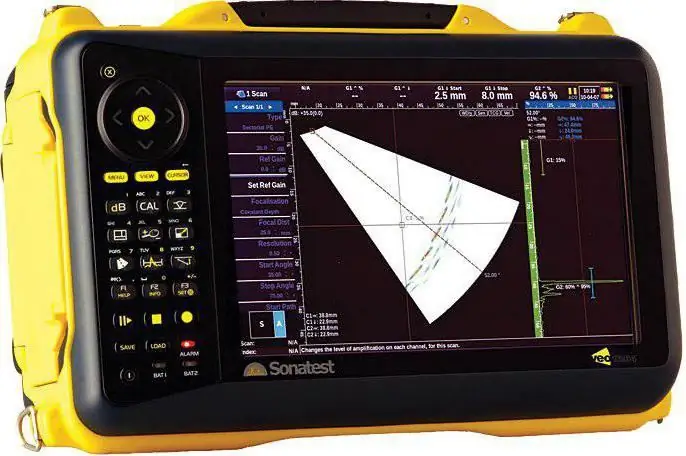
Operator musi poczekać, aż aktywność wskaźnika się zakończy,czy to cząstki proszku, czy zawiesina. Produkt sprawdzany jest wizualnie z w/w urządzeniami w postaci przyrządów optycznych. W takim przypadku moc powiększania tych urządzeń nie powinna przekraczać x10. Ponadto, w zależności od wymagań dotyczących badania, operator może już robić zdjęcia w celu dokładniejszej analizy komputerowej. Wielofunkcyjne stacje defektoskopów magnetycznych posiadają w swoim podstawowym wyposażeniu sprzęt do dekodowania replik z osadami proszkowymi. Rysunki uzyskane w trakcie sortowania są następnie porównywane ze standardowymi próbkami, co pozwala na wyciągnięcie wniosków co do jakości produktu i jego dopuszczalności do zamierzonego zastosowania.
Wniosek
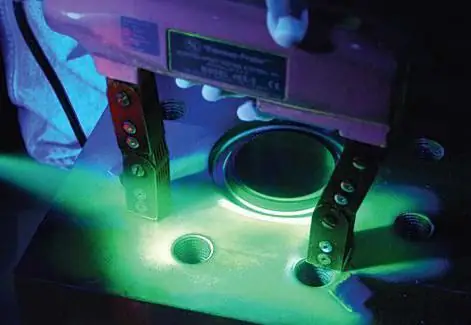
Przyrządy do wykrywania wad magnetycznych są szeroko stosowane w różnych dziedzinach. Ale mają też wady, które ograniczają ich zastosowanie. W zależności od warunków pracy są to wymagania dotyczące warunków temperaturowych, aw niektórych przypadkach niedokładności. Jako uniwersalny środek kontroli eksperci zalecają stosowanie wielokanałowego defektoskopu magnetycznego, który może również wspierać funkcję analizy ultradźwiękowej. Liczba kanałów może osiągnąć 32. Oznacza to, że urządzenie będzie w stanie utrzymać optymalne parametry wykrywania wad dla tej samej liczby różnorodnych zadań. Zasadniczo kanały rozumiane są jako liczba trybów pracy skoncentrowanych na określonych cechach materiału docelowego i warunkach środowiskowych. Takie modele nie są tanie, ale zapewniająpoprawność wyników przy wykrywaniu różnego rodzaju wad powierzchniowych i struktury wewnętrznej.
Zalecana:
Piec szklany: rodzaje, urządzenie, specyfikacje i praktyczne zastosowanie
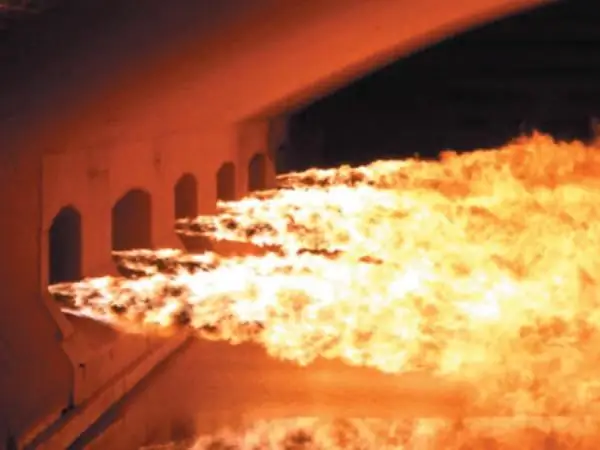
W dzisiejszych czasach ludzie aktywnie używają szkła do różnych celów. Sam proces wytwarzania szkła to topienie surowców lub wsadu. Do topienia materiału stosuje się piece do topienia szkła. Występują w różnych typach i są klasyfikowane według kilku kryteriów
Mobilna stacja benzynowa: opis, urządzenie, zasada działania, zastosowanie
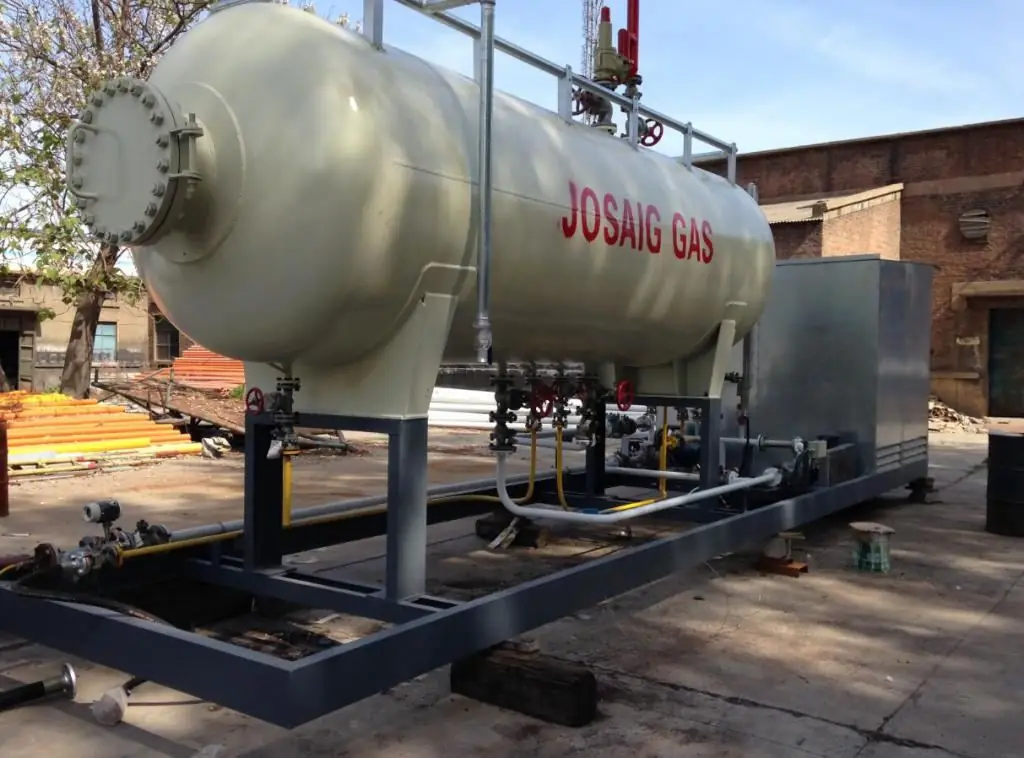
Mobilna stacja benzynowa to obecnie dość popularny pomysł na biznes. Dlatego osiągnięcie jakiegokolwiek sukcesu w tej dziedzinie jest możliwe tylko wtedy, gdy zwrócisz maksymalną uwagę na różne kluczowe punkty opisane w tym artykule
Co to są badania radiograficzne? Radiograficzna kontrola spoin. Kontrola radiograficzna: GOST
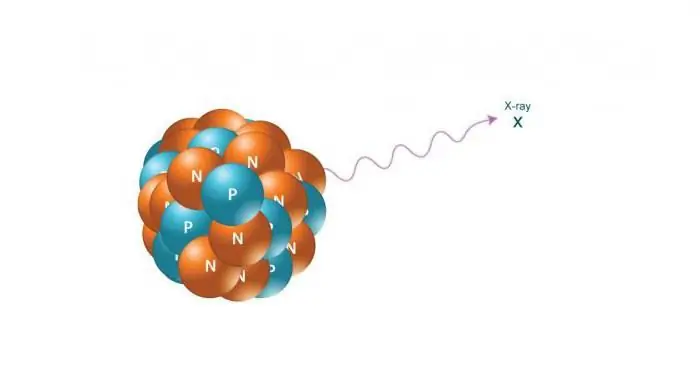
Fizyczne podstawy metod kontroli promieniowania. Cechy kontroli radiograficznej. Główne etapy radiograficznej kontroli spoin. Środki ostrożności w produkcji kontroli radiograficznej. Dokumentacja normatywna i techniczna
Piec koksowniczy - urządzenie hutnicze do produkcji koksu: urządzenie
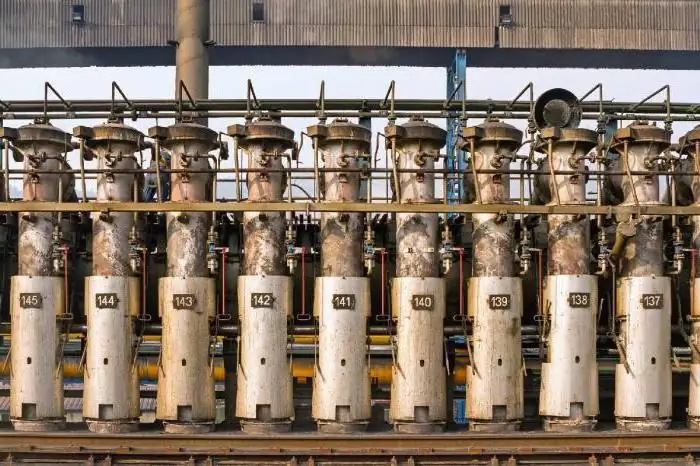
Wprowadzenie do eksploatacji pieców koksowniczych rozpoczęło się w latach 50. ubiegłego wieku. Użyteczna objętość pierwszych typowych pieców wynosiła 21,6 Nm³. W dalszej części artykułu rozważymy urządzenie wymienionego sprzętu
Cylinder "Rockwool" (Rockwool): opis, urządzenie, zasada działania, zastosowanie, zdjęcie
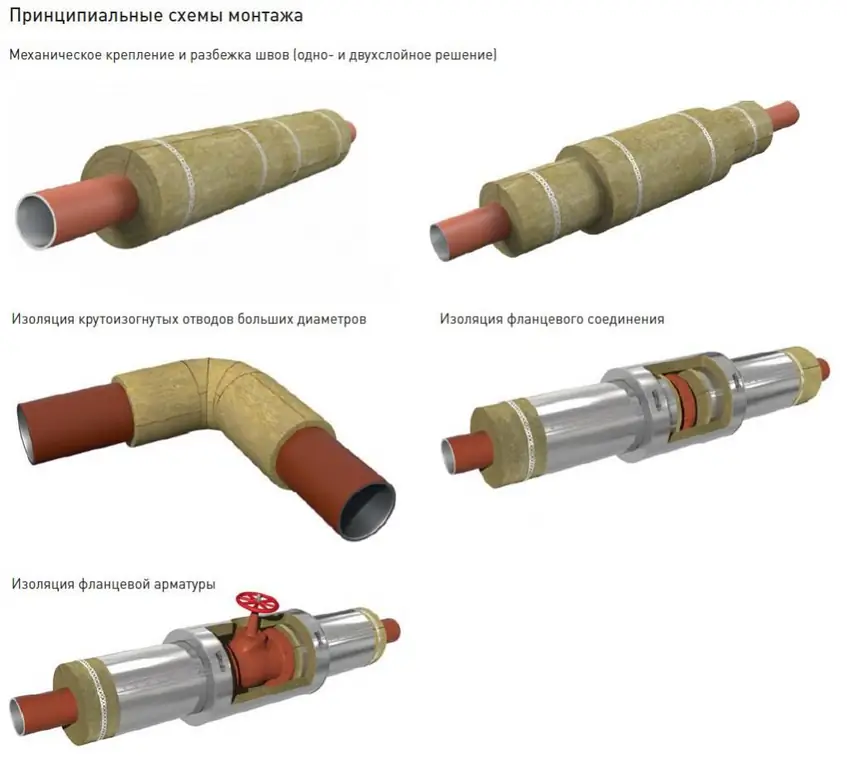
Żywotność rur jest skrócona ze względu na ich użytkowanie w warunkach niskich temperatur i wysokiej wilgotności. Problem ten można jednak rozwiązać stosując nowoczesne materiały ochronne wykonane z wełny mineralnej. Wśród ogromnej różnorodności propozycji na rynku butle Rockwool nie są ostatnie. Firma rozpoczęła swoją działalność ponad sto lat temu w Danii. W czasie swojego istnienia zdobył uznanie konsumentów