2025 Autor: Howard Calhoun | [email protected]. Ostatnio zmodyfikowany: 2025-06-01 07:14
Przemysł obróbki metali na tym etapie rozwoju jest w stanie rozwiązywać złożone zadania cięcia i wiercenia przedmiotów o różnym stopniu twardości. Stało się to możliwe dzięki opracowaniu zupełnie nowych sposobów oddziaływania na materiał, w tym szerokiej grupy metod elektromechanicznych. Jedną z najskuteczniejszych technologii tego typu jest obróbka ultradźwiękowa (UZO), oparta na zasadach promieniowania elektroakustycznego.
Zasady wymiarowego RCD
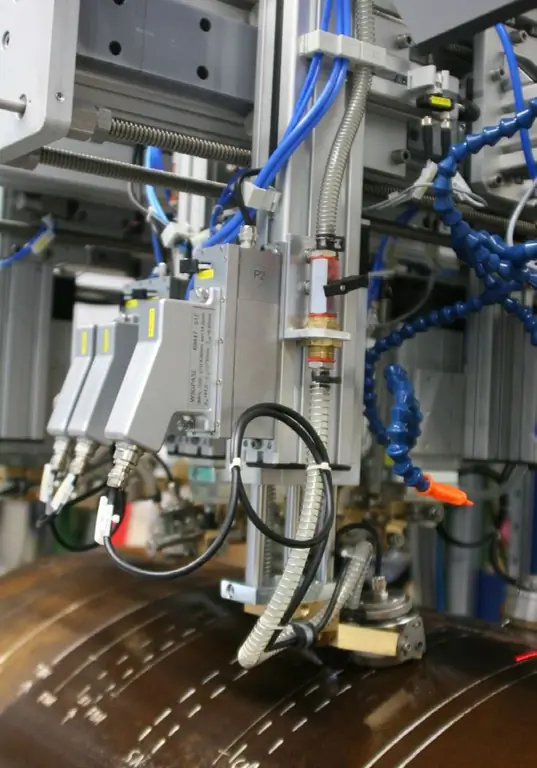
Podczas obróbki wymiarowej zwykłe przecinaki mechaniczne i materiały ścierne działają jako bezpośrednie narzędzie oddziaływania. Kluczowa różnica w tej metodzie polega na źródle energii, które zasila narzędzie. W tej pojemności ultradźwiękowy generator prądu działa na częstotliwościach 16-30 kHz. On prowokujeoscylacje tych samych ziaren ściernych o częstotliwości ultradźwiękowej, co zapewnia charakterystyczną jakość obróbki. Ponadto należy zwrócić uwagę na różnorodność rodzajów działania mechanicznego. To nie tylko zwykłe cięcie i szlifowanie elementów, ale również deformacja konstrukcji przy zachowaniu jej objętości. Co więcej, kalibracja ultradźwiękowa zapewnia, że cząstki obrabianego przedmiotu są utrzymywane na minimalnym poziomie nawet podczas cięcia. Ziarna, które wpływają na materiał, usunęły mikrocząsteczki, które nie wpływają na konstrukcję produktu. W rzeczywistości nie dochodzi do zniszczenia konstrukcji przez pobranie próbek, jednak może dojść do niekontrolowanego rozprzestrzeniania się pęknięć.
Różnice w stosunku do technologii plazmowej
Pod względem jakości obróbki, metody ultradźwiękowe i plazmowe mają wiele podobnych cech, dając możliwość bardzo precyzyjnego cięcia. Ale także między nimi istnieje znacząca różnica w zasadzie pracy. Jeśli więc RCD wiąże się z intensywnym uderzeniem w proszek ścierny od strony obrzynarki przy wsparciu energetycznym generatora fal elektrycznych, to metoda obróbki plazmowej wykorzystuje jako czynnik roboczy zjonizowany gaz naładowany jonami i elektronami. Oznacza to, że technologie przetwarzania ultradźwiękowego i plazmowego w równym stopniu wymagają wsparcia wystarczająco silnego generatora energii. W pierwszym przypadku jest to ultradźwiękowy aparat elektryczny, a w drugim wysokotemperaturowe instalacje gazowe lub izotermiczne zdolne do doprowadzenia reżimu temperaturowego czynnika roboczego do 16 000 °C. Ważnym elementem obróbki plazmowej jest zastosowanie elektrod i plazmysubstancje zapewniające dużą moc prowadzonego łuku przecinaka.
Urządzenia do obróbki ultradźwiękowej
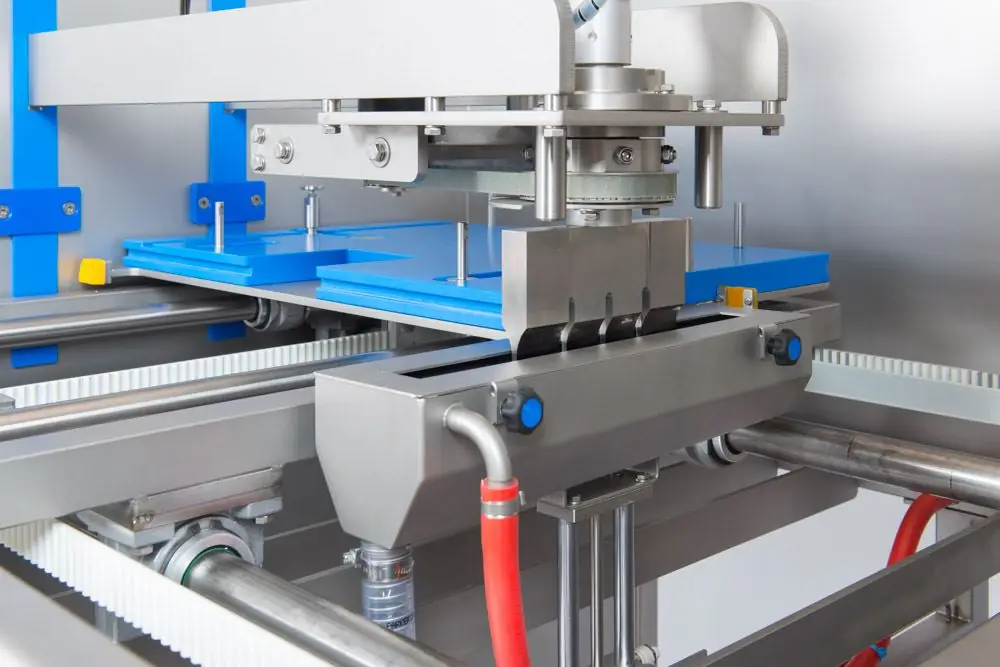
Teraz warto bardziej szczegółowo zastanowić się nad sprzętem używanym przy wdrażaniu RCD. W dużych gałęziach przemysłu do takich celów wykorzystuje się maszyny wyposażone w agregat prądotwórczy do wytwarzania prądu przemiennego o częstotliwości ultradźwiękowej. Wygenerowany prąd kierowany jest do uzwojenia przetwornika magnetycznego, który z kolei wytwarza pole elektromagnetyczne dla korpusu roboczego instalacji. Obróbka ultradźwiękowa zaczyna się od tego, że stempel maszyny zaczyna wibrować, będąc w polu elektromagnetycznym. Częstotliwości tych drgań są ustalane przez generator na podstawie ustawionych parametrów, które są wymagane w konkretnym przypadku.
Przebijak jest wykonany z materiału magnetostrykcyjnego (stopu żelaza, niklu i kob altu), którego wymiary liniowe mogą się zmieniać pod wpływem działania przetwornika magnetycznego. A na końcowym krytycznym etapie stempel działa na proszek ścierny poprzez oscylacje prowadzone wzdłuż kondensatora falowodu. Co więcej, skala i moc przetwarzania mogą być różne. Na rozważanym sprzęcie przemysłowa obróbka metali jest wykonywana z formowaniem masywnych konstrukcji, ale istnieją również kompaktowe urządzenia o podobnej zasadzie działania, na których wykonuje się bardzo precyzyjne grawerowanie.
Technika wymiarowa RCD
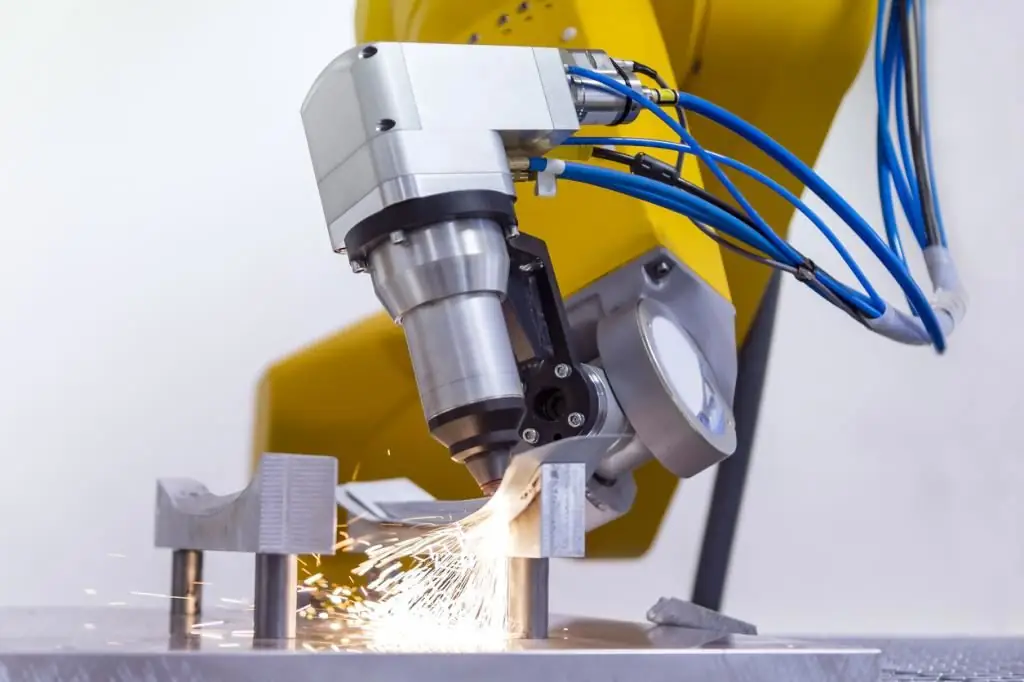
Po zainstalowaniu sprzętu i przygotowaniumateriału docelowego, zawiesina ścierna jest dostarczana do obszaru operacji - to znaczy do przestrzeni między powierzchnią produktu a końcówką oscylacyjną. Nawiasem mówiąc, jako ścierniwo zwykle stosuje się węgliki krzemu lub boru. W liniach zautomatyzowanych woda jest wykorzystywana do dostarczania proszku i chłodzenia. Bezpośrednia obróbka ultradźwiękowa metali składa się z dwóch operacji:
- Udarowe wnikanie cząstek ściernych w zamierzoną powierzchnię przedmiotu obrabianego, w wyniku czego tworzy się sieć mikropęknięć i przebijają się mikrocząstki produktu.
- Obieg materiału ściernego w strefie obróbki - zużyte ziarna zastępowane są strumieniami nowych cząstek.
Ważnym warunkiem skuteczności całego procesu jest utrzymanie wysokiego tempa obu procedur do końca cyklu. W przeciwnym razie zmieniają się parametry obróbki i spada dokładność kierunku ścierniwa.
Charakterystyka procesu
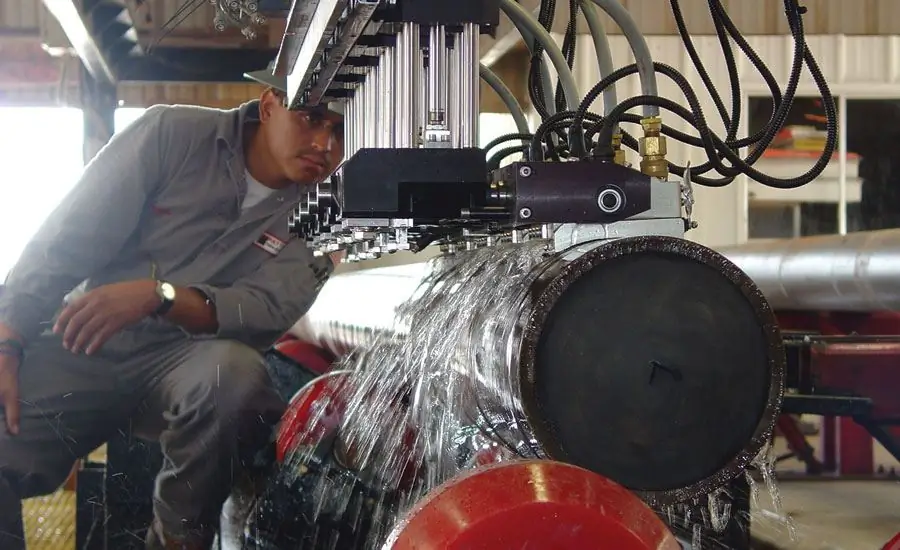
Parametry przetwarzania optymalne dla określonego zadania są wstępnie ustawione. Uwzględnia się zarówno konfigurację działania mechanicznego, jak i właściwości materiału przedmiotu obrabianego. Średnią charakterystykę obróbki ultradźwiękowej można przedstawić w następujący sposób:
- Zakres częstotliwości generatora prądu wynosi od 16 do 30 kHz.
- Amplituda oscylacji stempla lub jego narzędzia roboczego - dolne widmo na początku operacji wynosi od 2 do 10 mikronów, a górny poziom może osiągnąć 60 mikronów.
- Nasycenie zawiesiny ściernej - od 20 do 100 tys.ziarna na 1 cm kostkę.
- Średnica elementów ściernych - od 50 do 200 mikronów.
Zróżnicowanie tych parametrów pozwala nie tylko na indywidualną, wysoce precyzyjną obróbkę liniową, ale także na dokładne tworzenie skomplikowanych rowków i wycięć. Pod wieloma względami praca ze złożonymi geometriami stała się możliwa dzięki doskonałości właściwości stempli, co może wpływać na skład ścierny w różnych modelach z cienką nadbudową.
Gratowanie za pomocą RCD
Ta operacja opiera się na zwiększeniu aktywności kawitacyjnej i erozyjnej pola akustycznego, gdy do strumienia ściernego wprowadzane są bardzo małe cząstki o wielkości od 1 mikrona. Wielkość ta jest porównywalna z promieniem oddziaływania fali uderzeniowej, co umożliwia niszczenie słabych obszarów zadziorów. Proces pracy jest zorganizowany w specjalnym płynnym medium z mieszanką glicerynową. Jako pojemnik służy również specjalny sprzęt - fitomikser, w szklance, w której znajdują się odważone ścierniwa i część robocza. Gdy tylko fala akustyczna zostanie przyłożona do czynnika roboczego, rozpoczyna się przypadkowy ruch cząstek ściernych, które działają na powierzchnię przedmiotu obrabianego. Drobne ziarna węglika krzemu i elektrokorundu w mieszaninie wody i gliceryny zapewniają skuteczne gratowanie do wielkości 0,1 mm. Oznacza to, że obróbka ultradźwiękowa zapewnia dokładne i bardzo precyzyjne usuwanie mikrodefektów, które mogłyby pozostać nawet po tradycyjnym szlifowaniu mechanicznym. Jeśli mówimy o dużych zadziorach, to sensowne jest zwiększenie intensywności procesu poprzez dodanie pierwiastków chemicznych do pojemnikajak niebieski witriol.
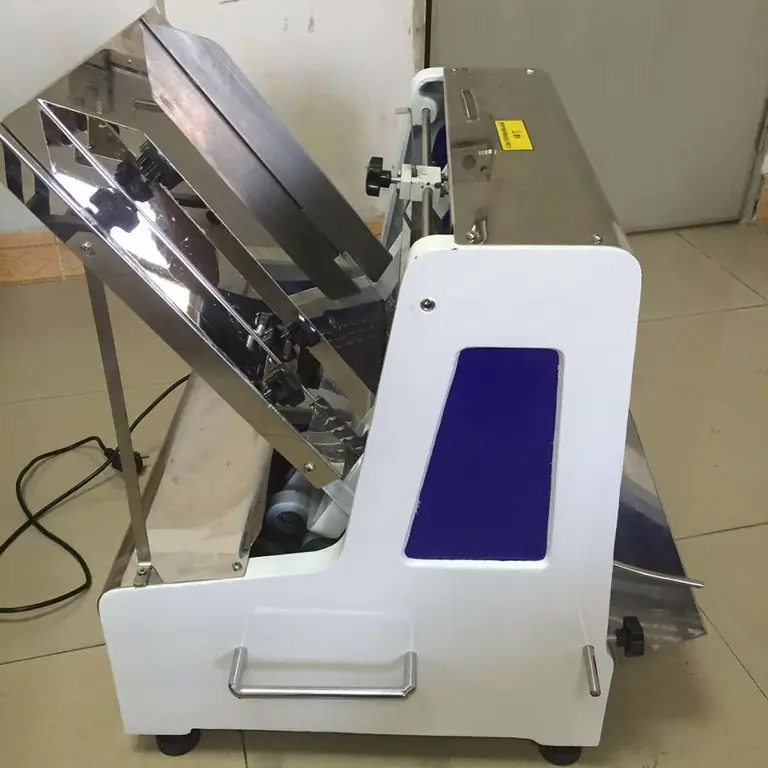
Czyszczenie części za pomocą RCD
Na powierzchniach pracujących metalowych półfabrykatów mogą znajdować się różnego rodzaju powłoki i zanieczyszczenia, których z różnych powodów nie można usunąć za pomocą tradycyjnego czyszczenia ściernego. W tym przypadku stosowana jest również technologia kawitacyjnej obróbki ultradźwiękowej w ciekłym medium, ale z kilkoma różnicami w stosunku do poprzedniej metody:
- Zakres częstotliwości będzie się wahał od 18 do 35 kHz.
- Rozpuszczalniki organiczne, takie jak freon i alkohol etylowy, są używane jako płynne medium.
- W celu utrzymania stabilnego procesu kawitacji i niezawodnego mocowania przedmiotu obrabianego, należy ustawić tryb rezonansowy pracy fitomiksera, w którym słup cieczy będzie odpowiadał połowie długości fali ultradźwiękowej.
Wiercenie diamentowe wspomagane ultradźwiękami
Metoda polega na użyciu obrotowego narzędzia diamentowego, które jest napędzane wibracjami ultradźwiękowymi. Koszty energii w procesie uzdatniania przekraczają wielkość wymaganych zasobów tradycyjnymi metodami działania mechanicznego, osiągając 2000 J/mm3. Ta moc pozwala na wiercenie o średnicy do 25 mm z prędkością 0,5 mm/min. Również ultradźwiękowa obróbka materiałów przez wiercenie wymaga użycia chłodziwa w dużych ilościach do 5 l/min. Przepływy płynów wypłukują również drobny proszek z powierzchni oprzyrządowania i przedmiotu obrabianego,powstały podczas niszczenia ścierniwa.
Kontrola wydajności RCD
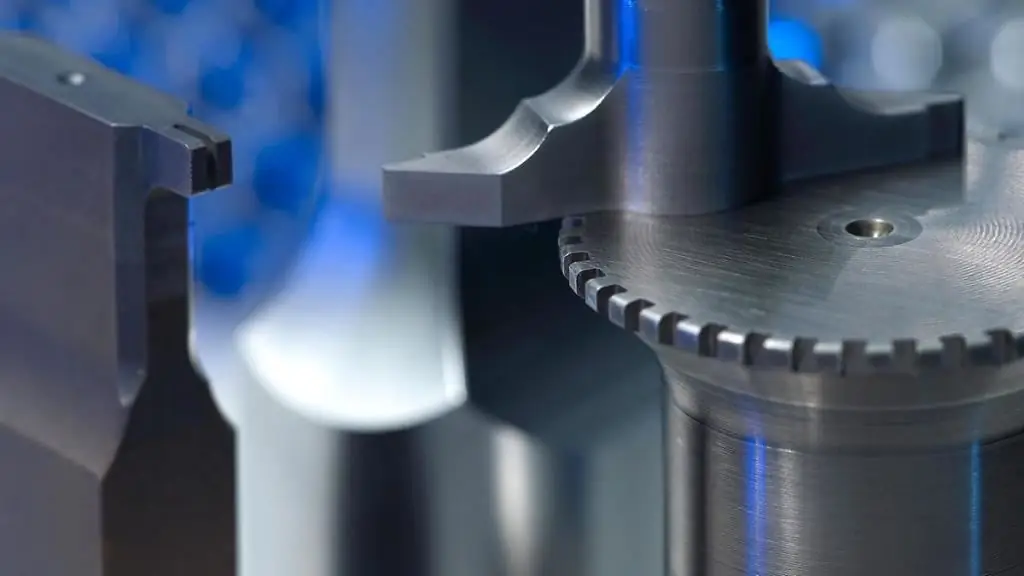
Proces technologiczny jest pod kontrolą operatora, który monitoruje parametry działających drgań. W szczególności dotyczy to amplitudy oscylacji, prędkości dźwięku, a także natężenia dopływu prądu. Za pomocą tych danych zapewniona jest kontrola środowiska pracy i wpływu materiału ściernego na obrabiany przedmiot. Cecha ta jest szczególnie istotna w obróbce ultradźwiękowej instrumentów, gdy w jednym procesie technologicznym można zastosować kilka trybów pracy urządzeń. Najbardziej postępowe metody sterowania polegają na udziale automatycznych środków zmiany parametrów przetwarzania na podstawie odczytów czujników rejestrujących parametry produktu.
Zalety technologii ultradźwiękowej
Zastosowanie technologii RCD zapewnia szereg korzyści, które przejawiają się w różnym stopniu w zależności od konkretnej metody jej wykonania:
- Wydajność procesu obróbki wzrasta kilkakrotnie.
- Zużycie narzędzi ultradźwiękowych jest zmniejszone 8-10 razy w porównaniu z konwencjonalnymi metodami obróbki.
- Podczas wiercenia parametry obróbki zwiększają głębokość i średnicę.
- Zwiększa dokładność działania mechanicznego.
Wady technologii
Szerokie zastosowanie tej metody jest nadal utrudnione przez szereg niedociągnięć. Związane są one głównie ze złożonością technologiczną organizacji.proces. Ponadto obróbka ultradźwiękowa części wymaga dodatkowych operacji, w tym dostarczenia materiału ściernego do obszaru roboczego oraz podłączenia urządzeń do chłodzenia wodą. Czynniki te mogą również zwiększyć koszt pracy. Podczas obsługi procesów przemysłowych wzrastają również koszty energii. Dodatkowe zasoby są wymagane nie tylko do zapewnienia prawidłowego działania jednostek głównych, ale także do działania systemów zabezpieczeń i odbieraków prądu, które przesyłają sygnały elektryczne.
Wniosek
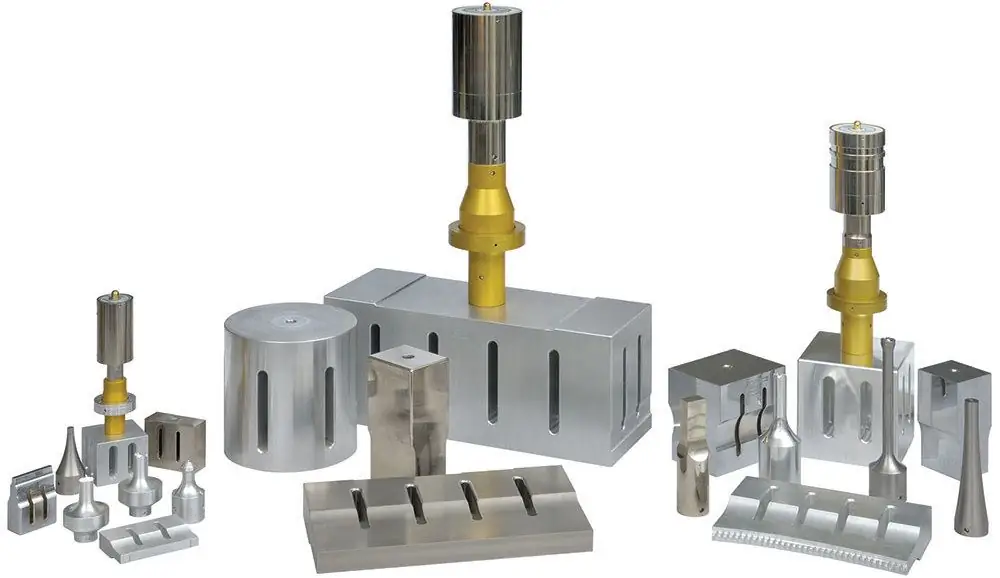
Wprowadzenie ultradźwiękowej technologii ściernej do procesów obróbki metali wynikało z ograniczeń w stosowaniu tradycyjnych metod cięcia, wiercenia, toczenia itp. W przeciwieństwie do konwencjonalnej tokarki, ultradźwiękowa obróbka metali jest w stanie skutecznie radzić sobie z materiałami o podwyższonej twardości. Zastosowanie tej technologii umożliwiło wykonywanie operacji obróbczych na stali hartowanej, stopach tytanowo-węglikowych, produktach zawierających wolfram itp. Jednocześnie gwarantowana jest wysoka dokładność działania mechanicznego przy minimalnym uszkodzeniu konstrukcji znajdującej się w obróbce powierzchnia. Jednak, podobnie jak w przypadku innych innowacyjnych technologii, takich jak cięcie plazmowe, obróbka laserowa i strumieniem wody, nadal istnieją problemy ekonomiczne i organizacyjne przy stosowaniu takich metod obróbki metalu.
Zalecana:
Drewno poddane obróbce cieplnej: główne cechy, technologia produkcji, zalety i wady

Prawie każdy z nas spotkał się z taką koncepcją, jak drewno poddane obróbce cieplnej. Jednak niewielu zastanawiało się, co to naprawdę oznacza. Tymczasem ten materiał można uznać za innowacyjny. Dzięki wysokiej temperaturze - od +150°C do +250°C - materiał jest mocny i trwały
Grawerowanie pleksiglasu: zalety i wady, technologia, wyposażenie
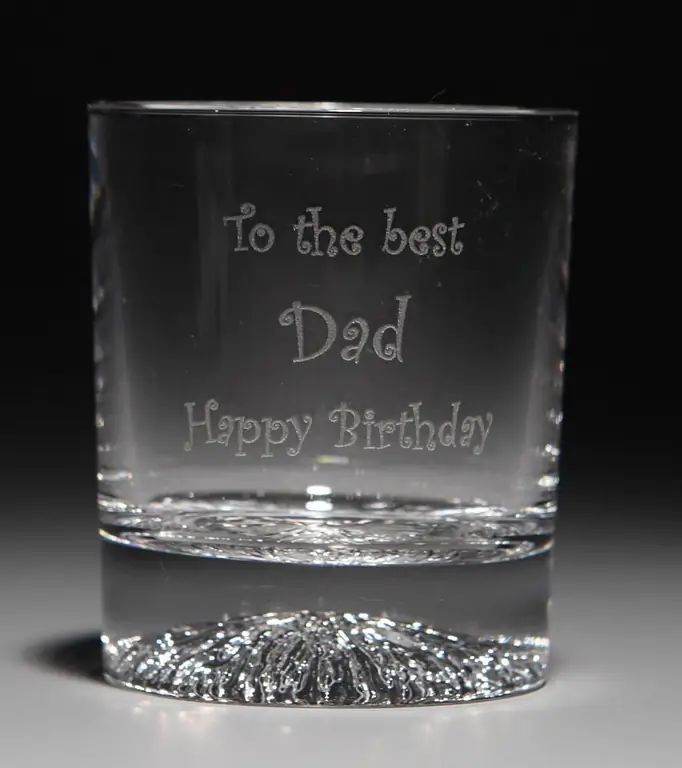
Grawerowanie pleksiglasu jest uważane za rzemiosło malarskie. Pamiątkowa figurka, witraże czy szklany stół, ozdobione wyszukanymi rysunkami, uosabiają delikatny artystyczny gust. Technologie wytrawiania i piaskowania to już przeszłość. Dziś, za pomocą maszyny laserowej, każda osoba może stworzyć bardzo szczegółowy wzór
Letterpress to Technologia druku typograficznego, nowoczesne etapy rozwoju, niezbędny sprzęt, zalety i wady tego typu druku
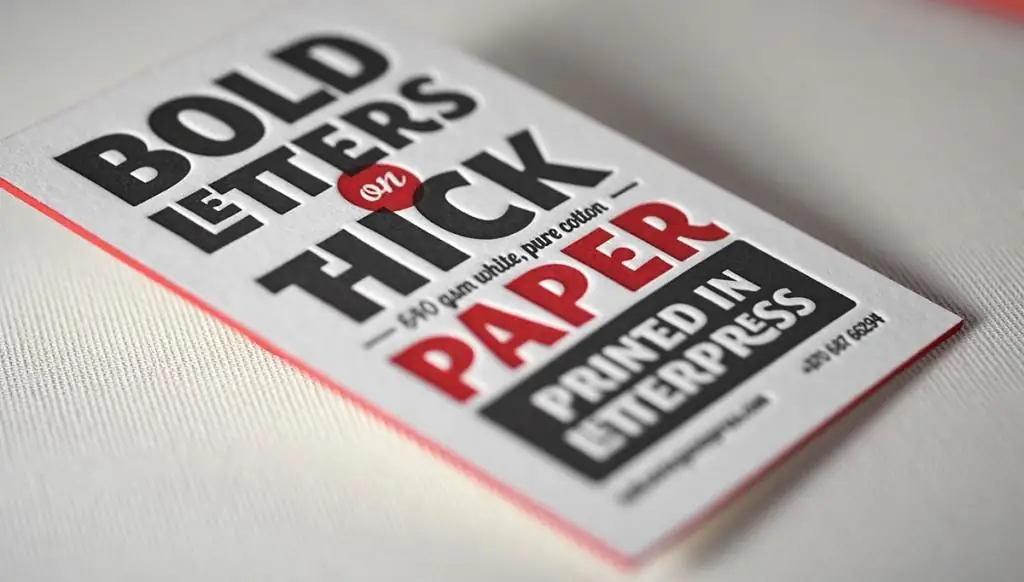
Letterpress to jedna z typowych metod nanoszenia informacji za pomocą matrycy reliefowej. Wystające elementy pokrywa się farbą w postaci pasty, a następnie dociska do papieru. W ten sposób powielane są różne masowe czasopisma, informatory, książki i gazety
Odlewanie traconego wosku: technologia, zalety i wady
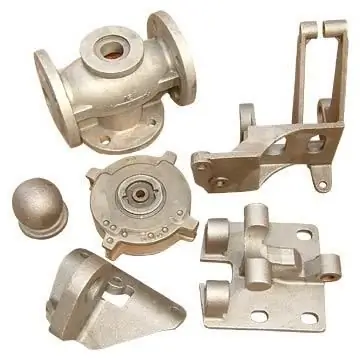
Wykorzystywanie modeli osłaniających jest dość popularną metodą produkcji odlewniczej. Znajduje zastosowanie tam, gdzie konieczne jest dokładne przestrzeganie wymiarów i zapewnienie wysokiej jakości powierzchni części. W ten sposób odlewane są łopatki turbin i wysokowydajne narzędzia, protezy i biżuteria, a także rzeźby o skomplikowanej konfiguracji. Forma do odlewania jest jednoczęściowa, model z materiałów niskotopliwych nie jest usuwany podczas formowania, ale jest wytapiany
Wady i zalety poliestru: opis materiału, zalety aplikacji, recenzje
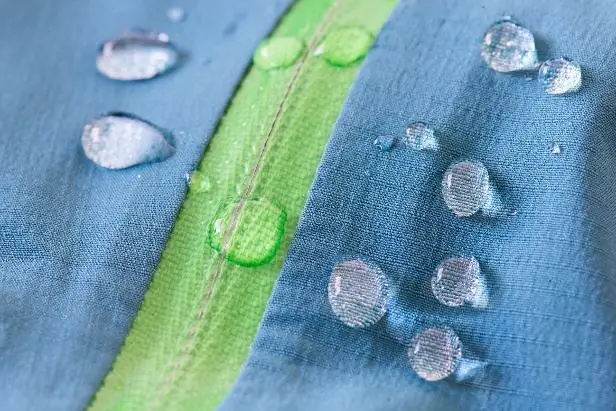
Poliester można znaleźć w składzie niemal każdego elementu, który znajduje się w szafie każdej osoby. Robi się z niego nie tylko ubrania, ale także buty, koce, bieliznę termiczną, dywany. Jakie są cechy każdego rodzaju produktu poliestrowego. W naszym artykule omówiono zalety i wady tych produktów