2025 Autor: Howard Calhoun | [email protected]. Ostatnio zmodyfikowany: 2025-06-01 07:14
Wykorzystywanie modeli osłaniających jest dość popularną metodą produkcji odlewniczej. Metodę wyróżnia złożoność procesu technologicznego oraz wysokie koszty pracy przy procesach przygotowawczych. Dlatego znajduje zastosowanie tam, gdzie konieczne jest dokładne obserwowanie wymiarów i zapewnienie wysokiej jakości powierzchni części. W ten sposób odlewane są łopatki turbin i wysokowydajne narzędzia, protezy i biżuteria, a także rzeźby o skomplikowanej konfiguracji. Istotą odlewania woskiem traconym jest to, że forma do odlewania jest jednoczęściowa, model materiałów niskotopliwych nie jest usuwany podczas formowania, ale jest topiony. Zapewnia to dokładne przestrzeganie wymiarów i reliefu. Do wnęki pozostałej po modelu wlewa się metal. Po zakończeniu chłodzenia forma jest niszczona, a produkt usuwany. Przy odlewaniu dużych serii obniża się koszt produktu.
Korzyści z metody
Główną zaletą odlewania metodą traconego wosku jest dokładność przenoszenia formy i niska chropowatość powierzchni. Ponadto dostępne są inne korzyści:
- Dostępna produkcja lekko obrobionych części ze stopów.
- Ogranicza potrzebę dalszej obróbki.
- Produkty są odlewane, które w innym przypadku musiałyby być wykonane w częściach i zmontowane razem.
- Przy dużych seriach osiąga się zmniejszenie określonej pracochłonności (na jeden produkt) i jego kosztu.
- Możliwość mechanizacji i częściowej automatyzacji czynności przygotowawczych samego odlewu.
Te zalety sprawiają, że metoda ta jest jedną z najpopularniejszych i wykorzystywanych we współczesnej metalurgii, zwłaszcza w połączeniu z nowoczesnymi metodami odlewania progresywnego.
Wady odlewania inwestycyjnego
Wydaje się, że niewątpliwe zalety tej metody powinny zapewnić jej dominację wśród innych metod. Jednak pomimo popularności metody odlewania metodą traconego wosku, wady uniemożliwiły jej szerokie zastosowanie. Główną wadą jest złożoność procesu wieloetapowego. Wymaga dość skomplikowanego i drogiego wyposażenia technologicznego do etapów przygotowawczych. W przypadku prostych produktów wytwarzanych w małych partiach ta metoda ma wyższy koszt.
W celu oszczędnego zastosowania odlewania metodą traconego wosku porównuje się zalety i wady metody, podejmuje się decyzję ojego wybór dokonywany jest na podstawie oceny stosunku ceny do jakości. W związku z tym stosuje się go głównie do najbardziej krytycznych i drogich produktów, które trudno uzyskać w inny sposób, takich jak łopatki turbin, rzeźby, narzędzia szybkoobrotowe itp. Kolejnym obszarem zastosowania są odlewy wielkogabarytowe, m.in. którego efekt skali pozwala na osiągnięcie znacznej redukcji kosztów.
Technologia
Technologia odlewania inwestycyjnego to wieloetapowy proces produkcyjny, który jest stosunkowo pracochłonny. W pierwszym etapie powstaje model wzorcowy, który stanie się standardem w produkcji modeli roboczych po przejściu przez wszystkie etapy produktu końcowego. Do wykonania makiety wykorzystuje się zarówno specjalne kompozycje modelowe, jak i tradycyjne - gipsowe lub drewniane. Materiał wzorca powinien łączyć wytrzymałość i łatwość obróbki.
Ponadto technologia odlewania metodą traconego wosku umożliwia stworzenie formy, do której zostaną odlane wszystkie modele robocze. Formy wykonane są z gipsu, gumy, silikonu, rzadziej metalu. Strukturalnie musi być koniecznie odłączany i przeznaczony do wielokrotnego użytku. Formę wypełnia się kompozycją modelową, po stwardnieniu demontuje się ją i wyjmuje kolejny działający model.
W przypadku produkcji unikalnych części lub małych serii, etapy tworzenia układu głównego i formy są pomijane, a układ (lub kilka) jest tworzony przez ręczne formowanie materiału.
Następnym krokiem w procesie odlewania metodą traconego wosku jestprodukcja wokół układu (lub bloku układów) formy odlewniczej. Matryce te są już strukturalnie nierozłączne i jednorazowe, co pozwala na dokładne przestrzeganie wymiarów i chropowatości produktu. We współczesnym przemyśle stosuje się dwa rodzaje form - tradycyjne piaskowo-gliniaste do odlewania w gruncie oraz formy skorupowe - do produkcji precyzyjnych i drogich części.
Po wykonaniu formy, model jest z niej wytapiany przez ogrzewanie lub przedmuchiwanie przegrzaną parą. Formy muszli są dodatkowo wzmacniane przez podgrzanie do 1000 ˚С.
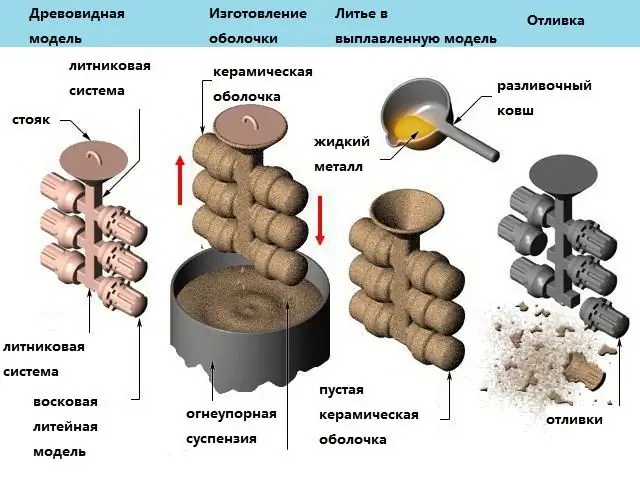
Końcowy etap procesu obejmuje właściwe odlanie produktu, jego schłodzenie w warunkach naturalnych lub specjalną metodą w termostacie, zniszczenie formy i oczyszczenie produktu. Metoda pozwala na uzyskanie wysokiej jakości odlewów o wadze od kilku gramów do kilkudziesięciu kilogramów.
Składy modeli
Materiał do produkcji makiety musi mieć określone właściwości. Powinien mieć właściwości takie jak:
- Plastyczność w fazie stałej. Konieczne jest dokładne powtórzenie kształtu przyszłego produktu i ewentualne poprawienie go.
- Siła. Model musi wytrzymać bez deformacji proces formowania wokół niego kształtu.
- topliwy. Renderowanie modelu nie powinno wymagać dużo czasu i energii.
- Roztopiona płynność. Kompozycja powinna z łatwością wnikać we wszystkie zakamarki i detale reliefu, dokładnie powtarzając zarysy przyszłego detalu.
- Gospodarka. Szczególnie ważne przy produkcji wielkoseryjnej.
W przypadku kompozycji modelowych zwykle stosuje się mieszaninę stearyny i parafiny. Materiały te z powodzeniem uzupełniają swoje parametry, kompensując niewystarczającą temperaturę topnienia parafiny oraz nadmierną lepkość stearyny.
Kompozycje na bazie wosku brunatnego są nie mniej popularne w branży. Jego główne właściwości to odporność na wilgoć, wytrzymałość oraz zdolność do tworzenia bardzo gładkich powłok, co jest szczególnie cenne przy modelowaniu produktów.
Stosowane są również mieszanki składające się z wosku z węgla brunatnego, parafiny i stearyny.
Wykonywanie form
Do produkcji wyjątkowych produktów przygotowywany jest layout poprzez ręczne wycięcie kawałka materiału modelowego lub według szablonów. Modele w postaci korpusów obrotowych są również wykonywane na tokarkach. W ostatnim czasie coraz bardziej rozpowszechniła się metoda drukowania modeli 3D. Nadaje się zarówno do pojedynczych układów, jak i małych serii.
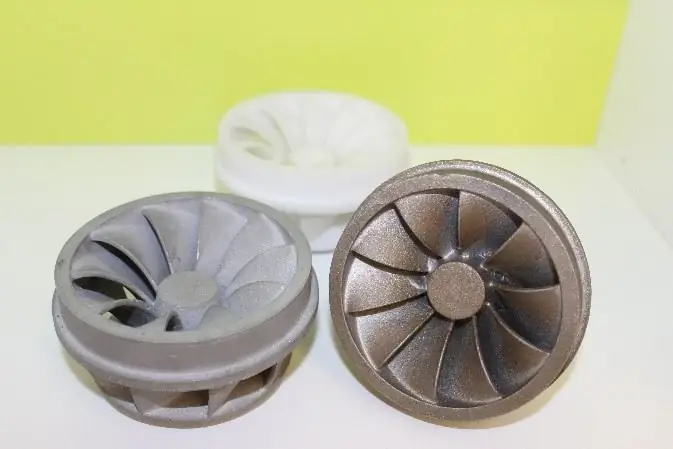
Koszt nowoczesnej przemysłowej drukarki 3D jest nadal wysoki, ale ze względu na łatwość rekonfiguracji z jednego produktu na drugi, może ona stać się skutecznym narzędziem do modelowania w przypadku dużej liczby niejednorodnych, małych serii zamówień.
Aby wykonać dużą liczbę identycznych układów, matrycę wykonuje się z gipsu, gumy, silikonu lub metalu. Z kolei układy robocze powstają poprzez odlewanie w matrycy. Forma z założenia musi być składana, aby zapewnić możliwość wykonania określonej liczby modeli. Wybrany materiał również powinien dawać taką możliwość, dlatego stawiane są mu takie wymagania jak wytrzymałość, gęstość, mała chropowatość, obojętność chemiczna w stosunku do układu. Substancja pleśni musi również mieć minimalną przyczepność do makiety, aby zapewnić łatwe usunięcie gotowych makiet i zachowanie wymiarów. Ważną właściwością formy jest jej wytrzymałość i odporność na zużycie, zwłaszcza w przypadku dużych serii.
Tworzenie modeli i bloków
Powszechnie stosowaną metodą wytwarzania modeli osłaniających jest odlewanie ich pod niskim ciśnieniem do form. Wtrysk płynnej mieszanki odbywa się zarówno ręcznie, za pomocą strzykawek tłokowych, jak i doładowania mechanicznego, hydraulicznego lub pneumatycznego. W przypadku stosowania wosku z węgla brunatnego konieczne jest podgrzanie rurociągów zasilających kompozycję ze względu na jej dużą lepkość. Modele ze styropianu są wytwarzane metodą ekstruzji na zautomatyzowanych maszynach formierskich.
Aby zwiększyć efektywność ekonomiczną i zmniejszyć pracochłonność w przypadku seryjnej produkcji małych odlewów, ich układy łączone są w bloki. Systemy bramkowania są formowane nad blokami poprzez przymocowanie poszczególnych układów do wlewów za pomocą ręcznej lutownicy. W przypadku pojedynczych odlewów lub małych serii modele wykonywane są ręcznie.
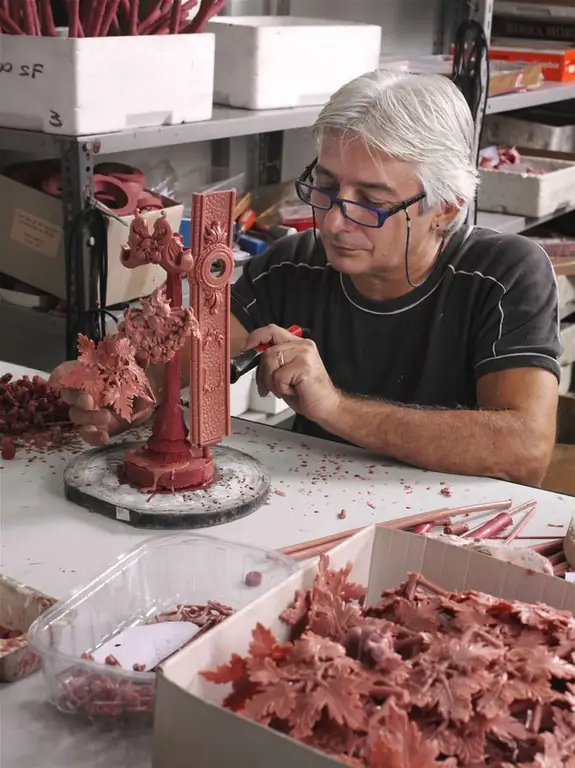
Przy formowaniu systemów bramkowania konieczne jest zapewnienie bezturbulentnego przepływu stopu, równomierne wypełnienie wszystkich elementów matrycy. Wypełniając formularz z PGS, należy również monitorować równomierne wypełnienie wszystkichotwory między wlewkami i zapobiegające uszkodzeniom.
Wykonywanie formy
W rozważanej metodzie odlewania metodą traconego wosku istnieją dwa główne typy form:
- Mieszanki piaskowo-gliniaste (SGM).
- Powłoka.
Formy odlewnicze z wosku płynnego są używane głównie do produkcji małych serii produktów, które nie wymagają bardzo dużej dokładności. Proces ich wytwarzania jest dość pracochłonny i wymaga wysokich, często unikalnych umiejętności modelarzy i formarzy. Częściowa mechanizacja nadaje się tylko do niektórych operacji, takich jak przygotowanie i wypełnienie masy formierskiej, jej ubijanie.
Z drugiej strony formy skorupowe są używane do produkcji części, które wymagają szczególnej precyzji wykonania. Proces ich wytwarzania jest bardziej złożony i długotrwały, ale lepiej nadaje się do mechanizacji.
Odlew naziemny
To najwcześniejsza metoda obróbki metalu opanowana przez ludzkość. Został on opanowany przez naszych przodków jednocześnie z początkiem stosowania wyrobów metalowych jako broni, narzędzi lub naczyń, czyli około 5 tysięcy lat temu. Stopiony metal wlewa się do przygotowanej matrycy z mieszaniny piasku i gliny. Najwcześniejsze miejsca obróbki metali powstały właśnie tam, gdzie w pobliżu znajdowały się złoża metali w postaci bryłek i placerów. Typowym przykładem jest fabryka Kasli na Uralu, znana na całym świecie z odlewania żelaznych koronek.
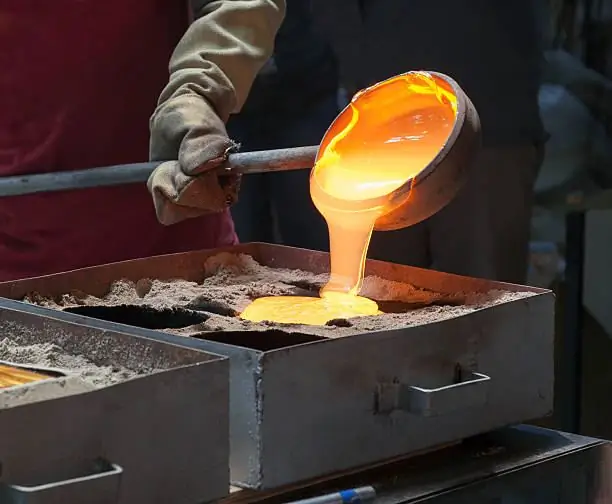
Metoda odlewania metodą traconego wosku jest wykorzystywana do produkcji wyrobów metalowych - zarówno żelaznych, jak ikolorowy. I tylko w przypadku metali wykazujących zwiększoną skłonność do reagowania w fazie ciekłej (takich jak tytan) konieczne jest wykonanie matryc z innych kompozycji.
Proces produkcji odlewów w PGS składa się z następujących faz:
- tworzenie modeli;
- przygotowanie kolby;
- napełnianie i zagęszczanie mieszanki w kolbie;
- odlew metalu;
- usuwanie i czyszczenie odlewu.
Formularz od ASG - jednorazowego użytku. Aby uzyskać gotowy produkt, będzie musiał zostać zepsuty. Jednocześnie większość mieszanki jest dostępna do ponownego wykorzystania.
Kompozycje składające się głównie z piasków kwarcowych o różnym uziarnieniu oraz iłów plastycznych, których zawartość waha się od 3 do 45 procent, są wykorzystywane jako materiały do produkcji ASG. Na przykład odlewy artystyczne są produkowane przy użyciu mieszanki o zawartości gliny 10-20%, w przypadku szczególnie dużych odlewów zawartość gliny jest dostosowywana do 25%.
Wykorzystywane są dwa podtypy:
- Mieszanki licowe. Znajdują się na wewnętrznej powierzchni formy i oddziałują ze stopionym metalem. Muszą być odporne na ciepło, odporne na różnice temperatur i wynikające z nich naprężenia. Te mieszanki mają drobną ziarnistość, aby dokładnie oddać szczegóły powierzchni. Bardzo istotna jest również zdolność mieszaniny do przepuszczania gazu.
- Mieszanki wypełniające. Służą do zasypywania między warstwą licową a ściankami puszki. Muszą wytrzymać ciężar wylanego metalu, zachować kształt produktu i przyczynić się do terminowego i całkowitego usunięcia gazów. Produkowany z tańszych gatunków piasku,wielokrotnego użytku.
Jeżeli gazy odlewnicze nie wydostaną się przez masę piasku formierskiego, ale przez system wlewowy, w odlewie pojawią się wady prowadzące do małżeństwa.
Tradycyjna technologia odlewania w ziemi została szczegółowo zilustrowana w filmie A. Tarkowskiego „Andrei Rublev”. W opowiadaniu „Dzwon” młody człowiek Boriska, syn zmarłego mistrza, kieruje artelem odlewniczym i odlewa dzwon kościelny.
Odlewanie powłoki
Metoda odlewania metodą traconego wosku w formach skorupowych charakteryzuje się najlepszym transferem wymiarów produktu oraz niską chropowatością powierzchni. Model wykonany jest z materiałów topliwych, takich jak wosk z węgla brunatnego. Odlewnie również szeroko stosują skład stearyny parafinowej w równych proporcjach. W przypadku odlewów o dużych rozmiarach w materiale modelowym zawarte są sole, które chronią model przed deformacją. Zanurzając się w roztworze, model pokrywa się 6-10 warstwami wysokotemperaturowej zawiesiny.
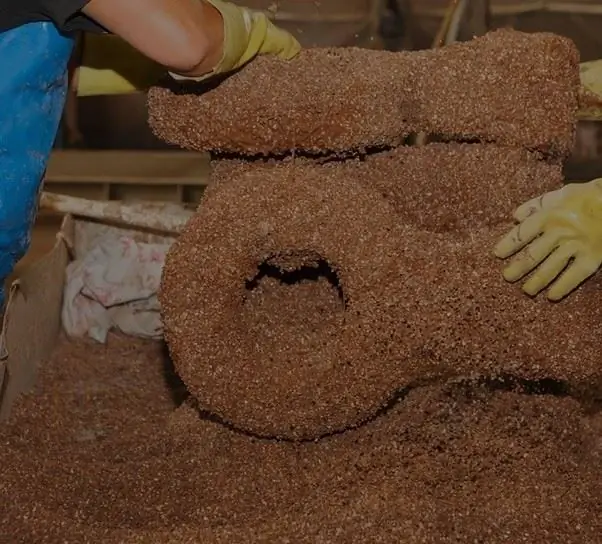
Hydrolizowane krzemiany działają jak spoiwo, kryształy elektrokorundu lub kwarcu są traktowane jako żaroodporne zraszanie. Materiały do form skorupowych charakteryzują się wysoką wytrzymałością, niską higroskopijnością i doskonałą przepuszczalnością gazów.
Układ jest suszony w atmosferze gazowego amoniaku. W kolejnym etapie forma jest podgrzewana do 120˚C w celu usunięcia modelu parafinowego. Pozostałości mieszaniny usuwa się przegrzaną parą pod wysokim ciśnieniem. Następnie forma jest wypalana w temperaturze do 1000 ˚С, co prowadzi do jej ostatecznego utrwalenia i usunięcia substancji,które mogą być uwalniane jako gazy podczas procesu odlewania.
Pocisk umieszczony jest w rodzaju kolby, która jest pokryta śrutem stalowym. Pomaga to zachować konfigurację podczas napełniania formy wytopem i jednocześnie poprawia warunki chłodzenia odlewu. Stop wlewa się do form ogrzanych do 1000 ˚С. Po schłodzeniu produktu według specjalnego programu w termostacie forma ulega zniszczeniu, odlew jest usuwany i czyszczony.
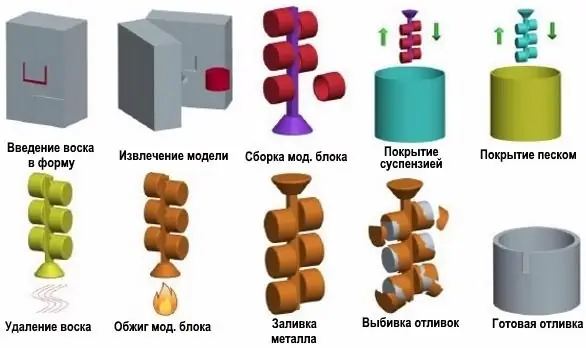
Główną zaletą tej metody odlewania jest wysoka dokładność wymiarowa i niska chropowatość powierzchni.
Dodatkowe zalety metody:
- Odlewanie części ze stopów trudnych do obróbki.
- Odlewanie elementów, które w innym przypadku musiałyby zostać odlane na części, a następnie złożone z powrotem.
Wadami tej metody odlewania metodą traconego wosku są niskie wykorzystanie metalu i zwiększona pracochłonność.
Odlewanie precyzyjne
Precyzyjne odlewanie metodą traconego wosku - to nazwa nadana zarówno technologii, jak i samemu produktowi końcowemu. Wysoką dokładność odlewania zapewnia fakt, że podczas przygotowania formy nie ma potrzeby wydobywania z niej modelu produktu. Przy zastosowaniu metody tradycyjnej produkcja matrycy odlewniczej jest złożonym i bardzo czasochłonnym procesem wieloetapowym. Jest to szczególnie prawdziwe w przypadku części odlewniczych o złożonej konfiguracji, z wgłębieniami, zagłębieniami i wewnętrznymi wnękami.
Na przykład, odlewając wazon z żeliwa lub miedzi o zmiennej krzywiźnie powierzchni, musisz użyć wielu sztuczek. Tak, po pierwszedolna połowa kolby jest wypchana, następnie model jest wyjmowany, odwracany, a górna połowa jest staranowana. Model musi być wykonany z kompozytu, uchwyty wazonu zbudowane są z dwóch elementów, wysuwane są przez wnękę modelu w dwóch etapach - najpierw dolny, potem górny. Wszystkie te liczne toczenia i przeciągania nie mogą mieć pozytywnego wpływu na integralność powierzchni formy i ostatecznie na dokładność zachowania wymiarów odlewu i jakości jego powierzchni. Poza tym pozostaje problem dokładnego dopasowania części kolb i bezpiecznego połączenia ich ze sobą.
Produkcja odlewów metodą traconego wosku pozbawiona jest tych mankamentów, nie wymaga tak wysoko wykwalifikowanych modelarzy oraz znacznie zmniejsza pracochłonność operacji prefabrykacji. Jest to szczególnie widoczne przy dużych seriach odlewów.
Metoda umożliwia osiągnięcie 2-5 klasy dokładności zgodnie z GOST 26645-85. Umożliwia to odlewanie produktów o wysokiej precyzji, takich jak łopatki turbin, narzędzia skrawające, w tym wysokowydajne frezy i wiertła, krytyczne mocno obciążone wsporniki, małe obciążone części pojazdów, obrabiarki i inne złożone mechanizmy.
Wysoka dokładność wymiarowa i wysoka klasa powierzchni minimalizują potrzebę dalszej obróbki odlewu, co oszczędza metal i obniża koszty produkcji.
Sprzęt
Wymagany sprzęt do odlewania metodą traconego wosku jest zróżnicowany i złożony. Przedsiębiorstwa łączą je w jeden i dobrze skoordynowany kompleks,zorganizowana jako strona, warsztat lub oddzielna produkcja.
Skład kompleksu zależy od skali produkcji, wielkości, konfiguracji i obiegu odlewów.
Tak więc w produkcji protez i biżuterii sprzęt będzie obejmował:
- tabela modeli;
- piec muflowy z termostatem;
- zestaw skalpeli i szpatułek do korekcji kształtu modelu;
- płyta formująca;
- kolba;
- zbiorniki do przechowywania i przygotowywania piasku formierskiego;
- zestaw narzędzi do ubijania piasku;
- tygiel do topienia metalu;
- kleszcze;
- młotkiem do rozbicia formy.
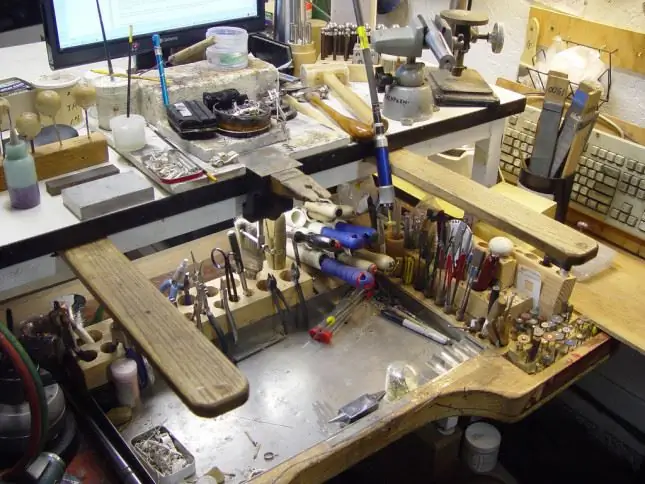
Ten kompleks produkcyjny z łatwością mieści się na jednym stole i w jednej szafce. Jeżeli planowana jest masowa produkcja np. odlewów aluminiowych - części urządzenia, wówczas sprzęt będzie wymagany do:
- kształtowanie i wylewanie form ceramicznych;
- suszenie form;
- topienie materiału modelowego i nałożenie warstwy żaroodpornej;
- czyszczenie odlewów z materiału do formowania.
I wreszcie właściwe wyposażenie kompleksu odlewniczego, przeznaczone do uzyskania wytopu i wlania go do formy. Może to być sprzęt odlewniczy:
- pod niskim ciśnieniem;
- odśrodkowa;
- w zwykły sposób grawitacyjny.
Maszyny do formowania wtryskowego i odlewania odśrodkowego są odrębnymi, wysoce zmechanizowanymi i zautomatyzowanymikompleks produkcyjny, odizolowany od atmosfery sklepu. Minimalizują pracę fizyczną i narażenie ludzi na szkodliwe warunki. Uszczelnione komory, w których zlokalizowane są kompleksy, zapewniają całkowite wychwytywanie i oczyszczanie spalin, co znacznie zwiększa przyjazność dla środowiska przedsiębiorstwa.
Odlewanie traconego wosku ma dość wysoki potencjał rozwoju, zwłaszcza w połączeniu z zaawansowanymi technikami wytwarzania form i odlewania.
Zalecana:
Drewno poddane obróbce cieplnej: główne cechy, technologia produkcji, zalety i wady

Prawie każdy z nas spotkał się z taką koncepcją, jak drewno poddane obróbce cieplnej. Jednak niewielu zastanawiało się, co to naprawdę oznacza. Tymczasem ten materiał można uznać za innowacyjny. Dzięki wysokiej temperaturze - od +150°C do +250°C - materiał jest mocny i trwały
Ciągłe odlewanie stali: zasada działania, niezbędny sprzęt, zalety i wady metody
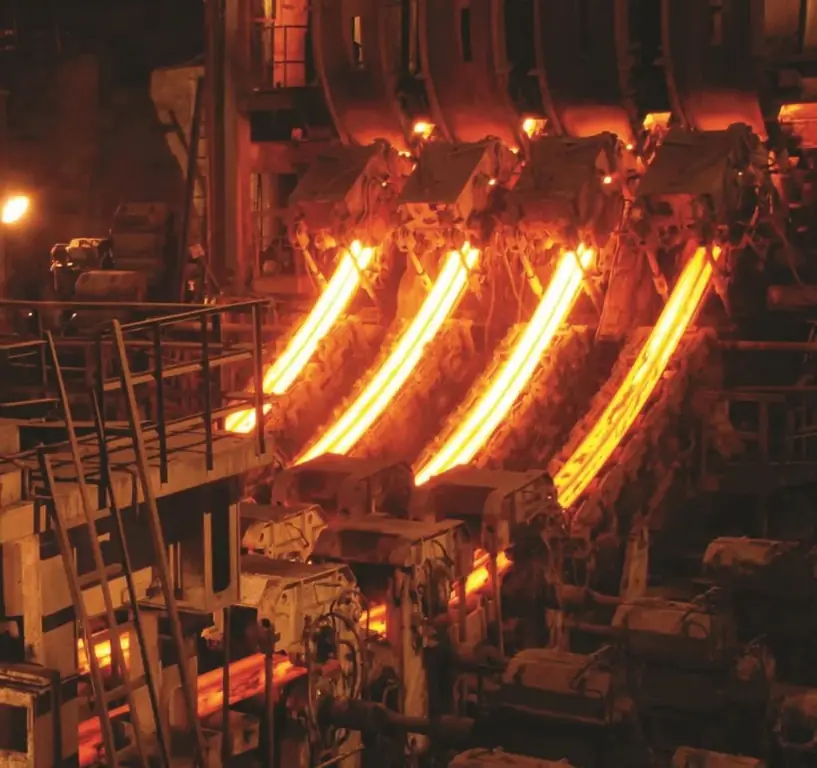
W dzisiejszych czasach ogromna ilość różnych rzeczy, części itp. jest wykonana ze stali.Oczywiście wymaga to dużej ilości materiału źródłowego. Dlatego zakłady od dawna stosują metodę ciągłego odlewania stali, charakteryzującą się najważniejszą cechą – wysoką wydajnością
Grawerowanie pleksiglasu: zalety i wady, technologia, wyposażenie
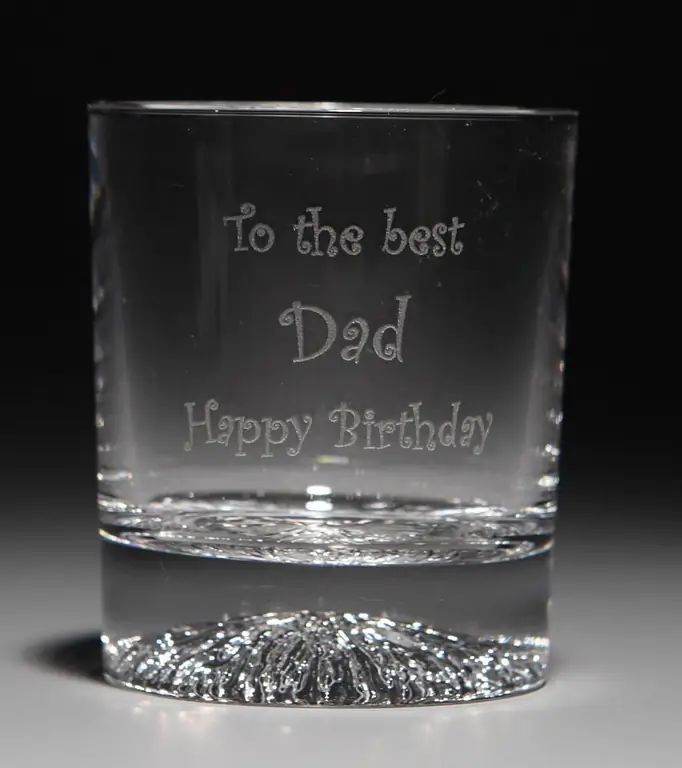
Grawerowanie pleksiglasu jest uważane za rzemiosło malarskie. Pamiątkowa figurka, witraże czy szklany stół, ozdobione wyszukanymi rysunkami, uosabiają delikatny artystyczny gust. Technologie wytrawiania i piaskowania to już przeszłość. Dziś, za pomocą maszyny laserowej, każda osoba może stworzyć bardzo szczegółowy wzór
Odlewanie w formie silikonowej: sprzęt. Odlewanie próżniowe w formach silikonowych
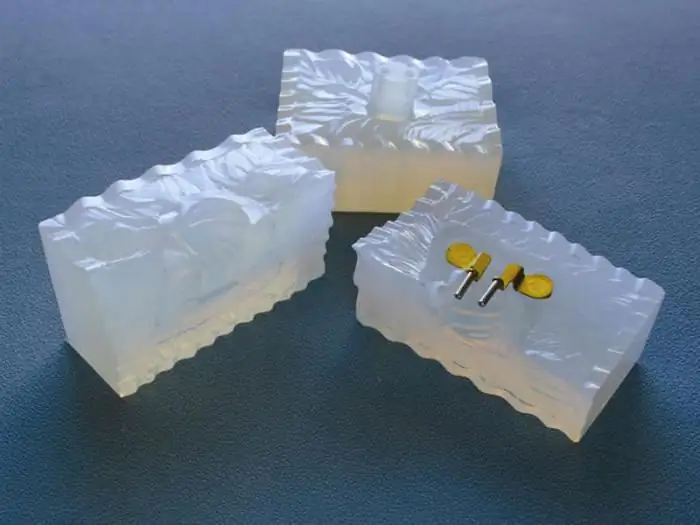
Do produkcji niewielkiej liczby wykrojów z tworzywa sztucznego najczęściej stosuje się odlewanie próżniowe do form silikonowych. Ta metoda jest dość ekonomiczna (wykonanie metalowej formy wymaga więcej czasu i pieniędzy). Ponadto formy silikonowe są wykorzystywane wielokrotnie, co również znacznie obniża koszty produkcji
Wady i zalety poliestru: opis materiału, zalety aplikacji, recenzje
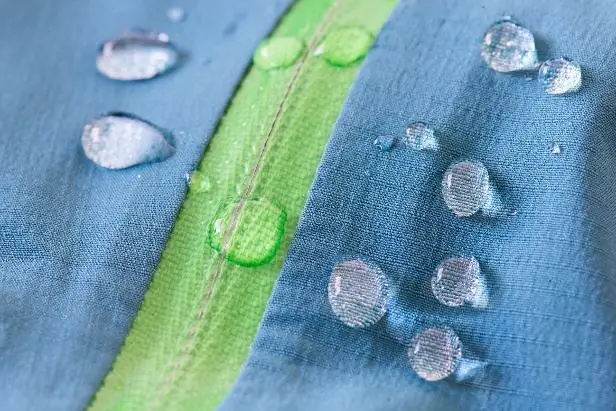
Poliester można znaleźć w składzie niemal każdego elementu, który znajduje się w szafie każdej osoby. Robi się z niego nie tylko ubrania, ale także buty, koce, bieliznę termiczną, dywany. Jakie są cechy każdego rodzaju produktu poliestrowego. W naszym artykule omówiono zalety i wady tych produktów