2025 Autor: Howard Calhoun | [email protected]. Ostatnio zmodyfikowany: 2025-01-24 13:23
Wiercenie jest jednym z rodzajów obróbki materiałów metodą cięcia. Ta metoda wykorzystuje specjalne narzędzie tnące - wiertło. Dzięki niemu możesz wykonać otwór o różnych średnicach, a także głębokościach. Ponadto możliwe jest tworzenie otworów wielościennych o różnych przekrojach.
Przypisanie operacji
Wiercenie jest operacją niezbędną, jeśli chcesz wykonać otwór w wyrobie metalowym. Najczęściej powodów do wiercenia jest kilka:
- wymagane do wykonania otworu do gwintowania, pogłębiania, rozwiercania lub wytaczania;
- konieczne do umieszczenia kabli elektrycznych, elementów mocujących w otworach, przełożenia przez nie śrub kotwiących itp.;
- pusta separacja;
- osłabienie zapadających się struktur;
- w zależności od średnicy otworu może być nawet używany do podkładania materiałów wybuchowych, na przykład podczas wydobywania kamienia naturalnego.
Ta lista może być kontynuowana przez długi czas, ale już teraz możemy stwierdzić, że operacja wiercenia jestjedna z najprostszych, a jednocześnie dość potrzebnych i pospolitych rzeczy.
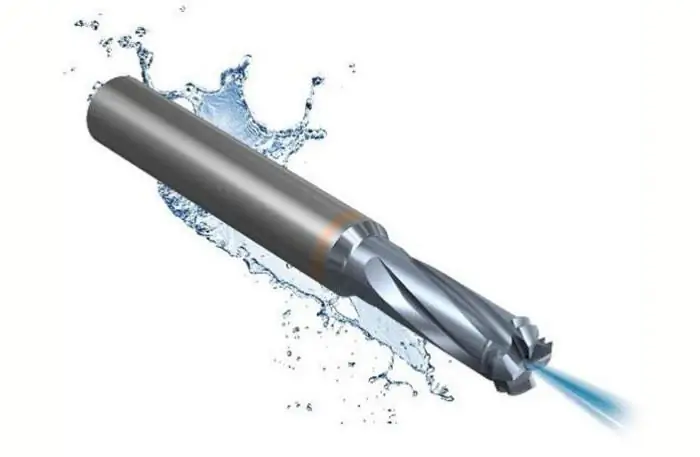
Materiały eksploatacyjne
Oczywiście, aby przeprowadzić proces wiercenia, niezbędne jest posiadanie wierteł. W zależności od tego materiału eksploatacyjnego zmieni się średnica otworu, a także liczba jego powierzchni. Mogą być okrągłe lub wielopłaszczyznowe - trójkątne, kwadratowe, pięciokątne, sześciokątne itp.
Ponadto wiercenie to operacja, podczas której wiertło nagrzewa się do wysokich temperatur. Z tego powodu konieczne jest precyzyjne dobranie jakości tego elementu, w oparciu o wymagania materiału, z którym ma być obrabiany.
- Dość powszechnym materiałem do produkcji uchwytów wiertniczych jest stal węglowa. Elementy z tej grupy są oznaczone następująco: U8, U9, U10 itd. Głównym przeznaczeniem tego typu materiałów eksploatacyjnych jest wiercenie otworów w drewnie, plastiku, miękkich metalach.
- Następne są wiertła wykonane ze stali niskostopowej. Przeznaczone są do wiercenia w tych samych materiałach, co węglowe, ale ich różnica polega na tym, że elementy tej marki mają podwyższoną wartość odporności cieplnej do 250 stopni Celsjusza, a także zwiększoną prędkość wiercenia.
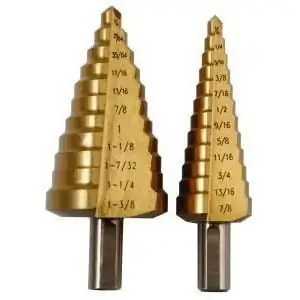
Ulepszone ćwiczenia
Istnieje kilka rodzajów wierteł przeznaczonych do materiałów wyższej jakości:
- Pierwszy typ wiertła jest wykonany ze stali szybkotnącej. Odporność cieplna tych materiałów eksploatacyjnych jest znacznie wyższa- 650 stopni Celsjusza i są przeznaczone do wiercenia dowolnych materiałów konstrukcyjnych w stanie nieutwardzonym.
- Następną grupą są wiertła z węglików spiekanych. Służą do wykonywania otworów w dowolnych stalach konstrukcyjnych niehartowanych, a także w metalach nieżelaznych. Cechą jest to, że używane jest wiercenie z dużymi prędkościami. Z tego samego powodu odporność na ciepło została zwiększona do 950 stopni Celsjusza.
- Jednym z najtrwalszych elementów są wiertła Borazon. Stosowany do pracy z żeliwem, stalami, szkłem, ceramiką, metalami nieżelaznymi.
- Ostatnia grupa to wiertła diamentowe. Służy do wiercenia w najtwardszych materiałach, szkle, ceramice.
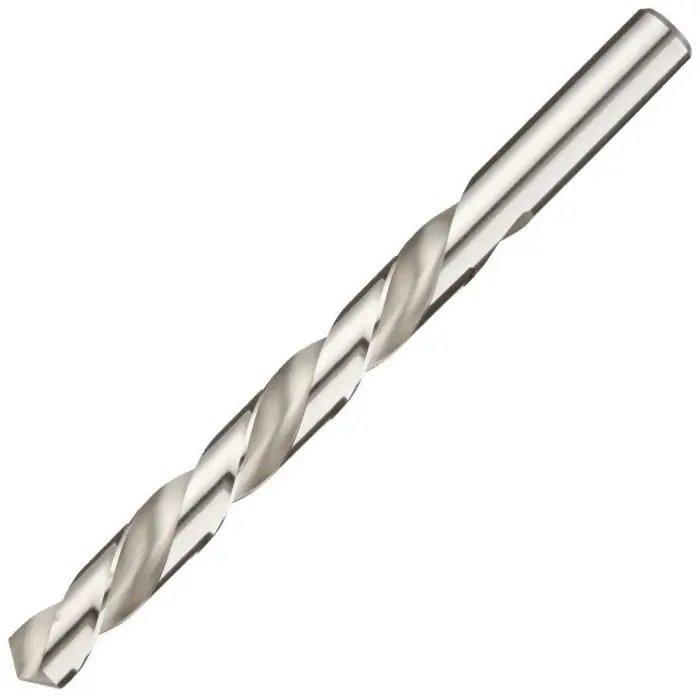
Rodzaje wiertarek
Do wykonania operacji wiercenia można używać następujących typów wiertarek:
- Urządzenia do wiercenia pionowego i poziomego. Wiercenie otworów dla takich maszyn to główna operacja.
- Stosowane są wytaczarki pionowe i poziome. Wiercenie jest uważane za czynności pomocnicze dla tych urządzeń.
- Frezarki pionowe, poziome i uniwersalne. W przypadku tych jednostek wiercenie jest również operacją drugorzędną.
- Tokarki i tokarki. W urządzeniach pierwszego typu wiertło jest częścią stałą, a sam przedmiot się obraca. W przypadku drugiego typu urządzenia wiercenie nie jest główną operacją, a wiertło jest elementem stałym, tak jak w pierwszymsprawa.
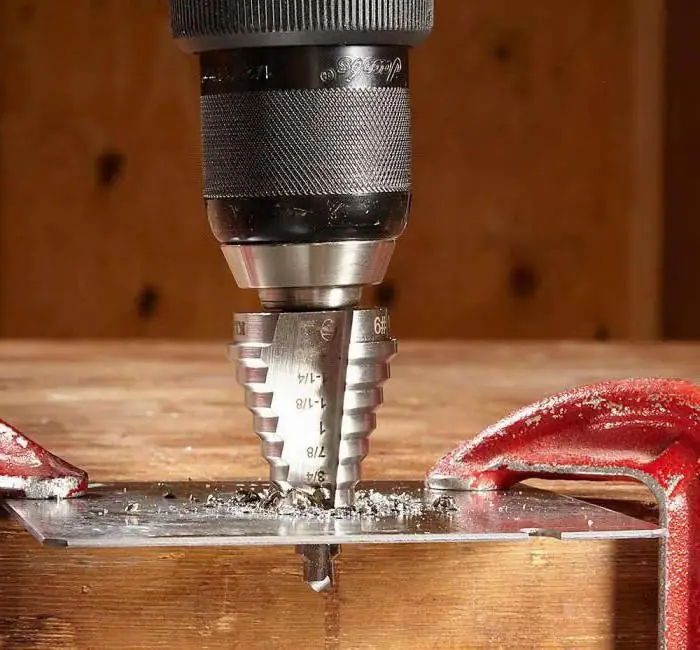
Są to wszystkie typy wiertarek, które mogą wykonać wszystkie wymagane operacje.
Narzędzia ręczne i operacje pomocnicze
W celu ułatwienia procesu wiercenia stosuje się kilka operacji pomocniczych. Należą do nich:
- Chłodzenie. Podczas wiercenia używane są różne płyny obróbkowe. Należą do nich np. woda, emulsje, kwas oleinowy. Można również stosować substancje gazowe, takie jak dwutlenek węgla.
- Ultradźwięki. Wibracje ultradźwiękowe wytwarzane przez wiertło są wykorzystywane do zwiększenia produktywności procesu, a także do poprawy łamania wiórów.
- Podgrzewany. W celu usprawnienia wiercenia w metalu o dużej gęstości jest on wstępnie podgrzewany.
- Strajk. Niektóre powierzchnie, takie jak beton, wymagają zastosowania obrotowych ruchów udarowych w celu zwiększenia wydajności.
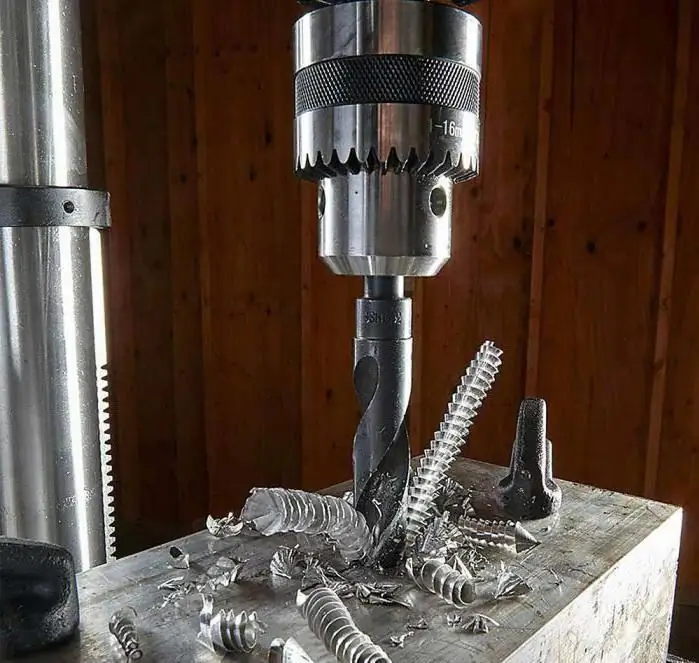
Tę procedurę można przeprowadzić nie tylko na maszynach w trybie automatycznym, ale także na urządzeniach ręcznych. Wiercenie ręczne wiąże się z użyciem narzędzi takich jak:
- Wiertarka mechaniczna. Wiercenie wykorzystuje ludzką siłę mechaniczną.
- Wiertarka elektryczna. Może wykonywać wiercenie konwencjonalne i udarowo-obrotowe. Zasilany energią elektryczną.
Rodzaje obróbki i chłodzenia
Istnieje kilka podstawowych rodzajów wiercenia - są towykonywanie otworów cylindrycznych, wielościennych lub owalnych, a także wiercenie istniejących otworów cylindrycznych w celu zwiększenia ich średnicy.
Głównym problemem, który pojawia się w procesie wiercenia metalu, jest silne nagrzewanie się elementu eksploatacyjnego, czyli wiertła, a także miejsca pracy. Temperatura materiału może osiągnąć 100 stopni Celsjusza lub więcej. Jeśli osiągnie określone wartości, może nastąpić spalanie lub topienie. Należy tutaj zauważyć, że wiele stali używanych do produkcji wierteł traci twardość po podgrzaniu, co tylko zwiększa tarcie, więc element będzie niestety szybciej się zużywał.
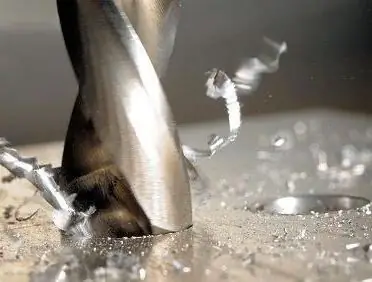
Aby zwalczyć tę wadę, stosuje się różne chłodziwa. Najczęściej przy pionowym wierceniu na maszynie można zorganizować dopływ chłodziwa bezpośrednio do miejsca pracy. Jeśli odbywa się to za pomocą narzędzi ręcznych, to po pewnym czasie należy przerwać proces i zanurzyć wiertło w cieczy.
Esencja wiercenia
Technologia wiercenia otworów to proces formowania rowków poprzez usuwanie wiórów w litym materiale za pomocą narzędzia skrawającego. Element ten wykonuje jednocześnie ruchy obrotowe i translacyjne lub rotacyjno-translacyjne, tworząc otwór.
Wykorzystanie tego rodzaju obróbki materiałów służy do:
- uzyskać niekrytyczne otwory o niskim stopniu dokładności i chropowatości używanej do mocowania śrub, nitów itp.;
- zdobądź otwory do gwintowania, rozwiercania itp.
Opcje przetwarzania
Za pomocą procedury głębokiego wiercenia lub rozwiercania można uzyskać otwory, które będą charakteryzować się 10 lub 11 stopniem chropowatości powierzchni. Jeżeli konieczne jest uzyskanie lepszego otworu, to po zakończeniu procesu obróbki należy go dodatkowo pogłębić i rozwiercić.
Aby zwiększyć dokładność pracy, w niektórych przypadkach można odwołać się do dokładnej regulacji położenia maszyny, odpowiednio naostrzonych materiałów eksploatacyjnych. Stosowana jest również metoda, w której praca jest wykonywana za pomocą specjalnego urządzenia zwiększającego dokładność. To urządzenie nazywa się dyrygentem. Istnieje również podział ćwiczeń na kilka klas. Istnieją wiertła kręte z prostym rowkiem, wiertła łopatkowe używane do wiercenia głębokiego lub rdzeniowego oraz wiertła do nakiełków.
Opis konstrukcji wiertła
Najczęściej do pracy używane jest konwencjonalne wiertło kręte. Oferty specjalne są używane znacznie rzadziej.
Spiralny element to dwuzębna część tnąca, która składa się tylko z dwóch głównych części - trzpienia i części roboczej.
Jeśli mówimy o części roboczej, można ją podzielić na cylindryczną i kalibrującą. Na pierwszej części wiertła znajdują się naprzeciw siebie dwa spiralne rowki. Głównycelem tej części jest usuwanie wiórów, które są uwalniane podczas pracy. Należy tutaj zaznaczyć, że rowki mają prawidłowy profil, co zapewnia prawidłowe ukształtowanie krawędzi tnących wiertła. Dodatkowo powstaje niezbędna przestrzeń, która jest niezbędna do usunięcia wiórów z otworu.
Technologia wiercenia
Tutaj ważne jest poznanie kilku szczegółowych zasad. Bardzo ważne jest, aby kształt rowków, a także kąt nachylenia pomiędzy kierunkiem osi wiertła a styczną do pasa, zapewniały łatwe odprowadzanie wiórów bez osłabiania przekroju zębów. Warto jednak tutaj zauważyć, że ta technologia, a zwłaszcza wartości liczbowe, będą się znacznie zmieniać w zależności od średnicy wiertła. Chodzi o to, że zwiększenie kąta nachylenia prowadzi do osłabienia działania wiertła. Ta wada jest tym bardziej wyraźna, im mniejsza jest średnica elementu. Z tego powodu musisz dostosować kąt wiertła. Im mniejsze wiertło, tym mniejszy kąt i odwrotnie. Całkowity kąt rowków wynosi od 18 do 45 stopni. Do wiercenia w stali niezbędne jest użycie wierteł o kącie nachylenia od 18 do 30 stopni. Jeśli otwory są wykonane w kruchych materiałach, takich jak mosiądz lub brąz, kąt zmniejsza się do 22-25 stopni.
Zasady pracy
W tym miejscu ważne jest, aby zacząć od tego, że w zależności od materiału narzędzia zmieni się również prędkość skrawania. Na przykład:
- Jeżeli wiercenie odbywa się przy użyciu elementów ze stali narzędziowej, minimalna prędkość wynosi 25 m/min, a maksymalna 35m/min.
- Jeżeli obróbka odbywa się za pomocą wierteł HSS, minimalna prędkość wynosi 12 m/min, a maksymalna 18 m/min.
- Jeśli używane są wiertła z węglików spiekanych, wartości wynoszą 50 m/min i 70 m/min.
Należy tutaj zauważyć, że technologia wiercenia polega na doborze szybkości zabiegu w zależności od średnicy samego elementu i niskim posuwie (wraz ze wzrostem średnicy prędkość również rośnie).
Charakterystyczną cechą pracy jest zastosowanie standardowego kąta na górze wiertła, który wynosi 118 stopni. W przypadku konieczności pracy z surowcami charakteryzującymi się dużą twardością stopu należy zwiększyć kąt do 135 stopni.
Bezpieczeństwo wiertarek
Jednym z ważnych zadań w tego typu obróbce było zachowanie właściwości skrawania materiałów eksploatacyjnych. Bezpieczeństwo tych parametrów zależy bezpośrednio od wybranej metody pracy i tego, czy była odpowiednia dla tego materiału. Na przykład, w celu wyeliminowania złamania wiertła w przejściu, konieczne jest znaczne zmniejszenie posuwu w momencie wyciągania wiertła z otworu.
Szczególną uwagę należy zwrócić na technologię wiercenia w sytuacjach, w których głębokość otworu przekracza długość spiralnego rowka materiału eksploatacyjnego. W momencie wkładania wiertła nadal będą się formować wióry, ale podczas wyjścia już ich nie będzie. Z tego powodu wiertła bardzo często się psują. Jeśli nie ma wyjścia z sytuacji, trzeba okresowo wyjmować wiertło i ręcznie czyścić je z niepotrzebnych elementów, czyliwióry.
Wiertła
Aby zrobić dziurę w określonej powłoce, konieczne jest użycie koron. Jednak muszą być również prawidłowo dobrane, w oparciu o określone parametry. Obecnie do tworzenia koron stosuje się trzy główne rodzaje materiałów - są to diamenty, węgliki wolframu i wolframu. Cechą korony diamentowej jest to, że wykonuje wiercenie bez wstrząsów. W takim przypadku uzyskuje się bardziej poprawną geometrię otworu.
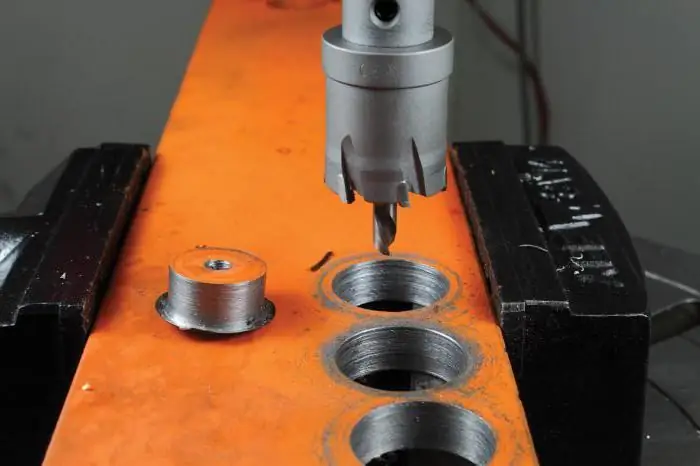
Główne zalety dysz diamentowych to: możliwość cięcia materiałów żelbetowych, niski poziom hałasu i zapylenia, brak uszkodzeń konstrukcji konstrukcji, ponieważ technologia nie wykorzystuje siły uderzenia.
Zalecana:
Wiercenie otworów w metalu, drewnie. Wiercenie dużych otworów w ścianie
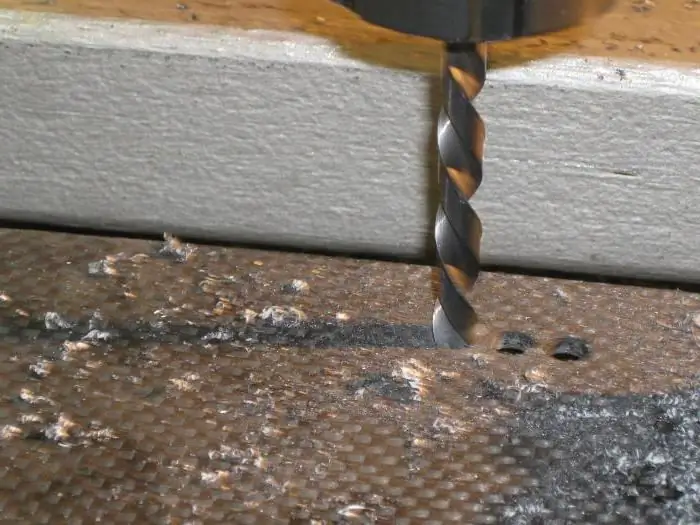
Artykuł dotyczy wiercenia. Rozważane są operacje tworzenia otworów w drewnie, materiałach metalowych i ścianach
Prędkość skrawania do frezowania, toczenia i innych rodzajów obróbki mechanicznej części
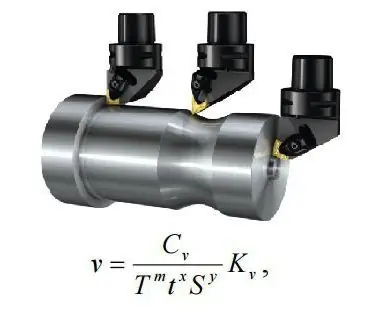
Obliczanie warunków skrawania to najważniejszy krok w produkcji każdej części. Bardzo ważne jest, aby same obliczenia były racjonalne. Wynika to z faktu, że dla różnych operacji mechanicznych konieczne jest indywidualne dobranie prędkości skrawania, prędkości obrotowej wrzeciona, posuwu, a także głębokości skrawania. Tryb racjonalny to taki, w którym koszty produkcji będą minimalne, a jakość powstałego produktu możliwie najdokładniejsza
Technologia wiercenia diamentowego i kluczowe korzyści
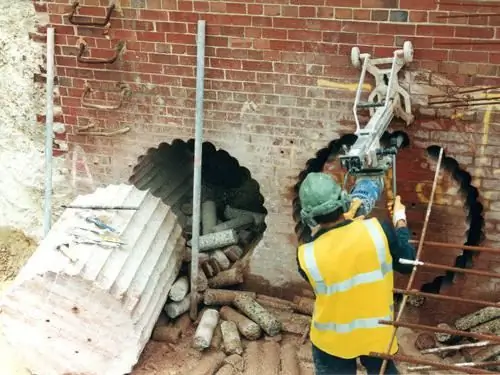
Każdego roku wiercenie diamentowe i wiercenie betonu zastępują inne technologie. Na przykład dziurkacz ma wiele wad, w przeciwieństwie do tej metody. Są to drgania, wysoki poziom hałasu itp. Najczęściej takie wiercenie stosuje się podczas prac budowlanych lub naprawczych. Porozmawiajmy na ten temat i zobaczmy, jakie są plusy i minusy wiercenia diamentowego
HDD - technologia wiercenia. Wiercenie kierunkowe poziome
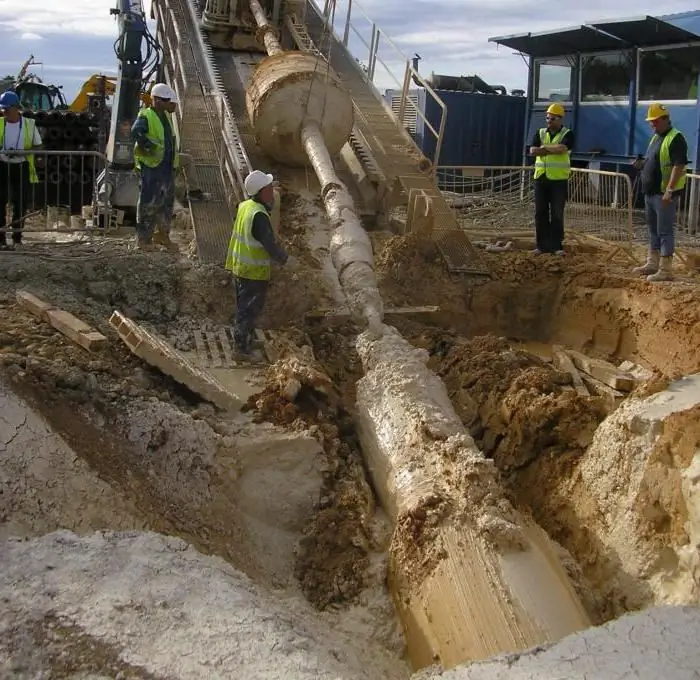
Artykuł poświęcony jest technologii poziomego wiercenia kierunkowego. Uwzględniane są cechy metody, niuanse jej realizacji itp
Wyżarzanie stali jako rodzaj obróbki cieplnej. Technologia metalowa
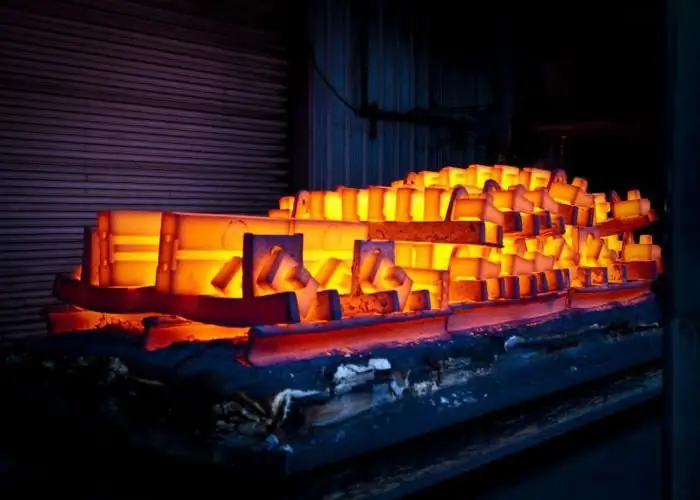
Tworzenie nowych materiałów i kontrolowanie ich właściwości to sztuka technologii metalowej. Jednym z jego narzędzi jest obróbka cieplna. Ta wiedza pozwala zmienić charakterystykę, a tym samym obszary zastosowania stopów. Wyżarzanie stali jest szeroko stosowaną opcją eliminacji wad produkcyjnych w produktach, zwiększając ich wytrzymałość i niezawodność