2025 Autor: Howard Calhoun | [email protected]. Ostatnio zmodyfikowany: 2025-01-24 13:23
Wraz z udoskonalaniem technologii spawania zmniejsza się ryzyko różnego rodzaju wad i odchyleń od standardowych parametrów. Niemniej jednak nawet automatyczne i zrobotyzowane spawarki nie pozwalają całkowicie wyeliminować ryzyka uzyskania złej jakości połączeń. Dlatego niezależnie od zastosowanej technologii wykonania operacji spawalniczych, po jej wykonaniu, wdrażana jest procedura kompleksowej kontroli jakości spawów. Metoda kontroli wizualnej jest pierwszym krokiem w całym procesie kontroli spawania.
Podstawy
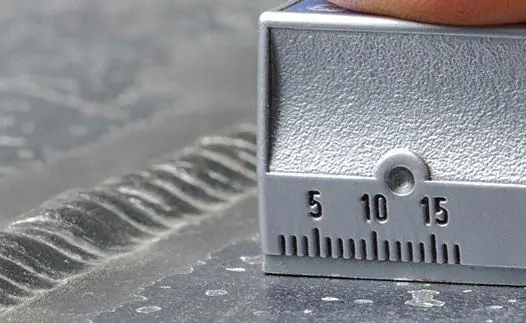
Kontrolę połączeń spawanych należy rozumieć jako procedurę technologiczną, którą można wykonać na różnych etapach procesu produkcyjnego, ale w każdym przypadku należy ją przeprowadzić zgodnie z wytycznymi regulacyjnymi. Do podstawowych zasad tej operacjiobejmują:
- Kontrola jest przeprowadzana na częściach, półfabrykatach i gotowych produktach w celu określenia zgodności tego obiektu z cechami projektu.
- Podczas wykonywania kontroli należy uwzględnić aktualny stan przedmiotu badań, cechy parametrów konstrukcyjnych i wymiarowych.
- Tylko wykwalifikowany personel zaznajomiony z technicznymi zasadami kontroli wizualnej zgodnie z GOST R EN 13018-2014 może dokonywać kontroli. Dodatkowo wizja bezpośrednich uczestników testu musi spełniać wymagania normy ISO 9712.
- Podczas czynności kontrolnych obiekt docelowy nie może być narażony na zniszczenie i naprężenia mechaniczne, które w zasadzie mogą prowadzić do zmian w strukturze materiału i jego wydajności.
Zasady i cele metody
Istotą tej metody kontroli jest badanie powierzchni obiektów docelowych przez inspekcję zewnętrzną. Na początkowym poziomie operator bada strefę spawania własnym wzrokiem, ale można również zastosować specjalne urządzenia techniczne. Na przykład przyrządy optyczne umożliwiają badanie powierzchni pod kątem zbliżania się i akcentowania strefy za pomocą promieniowania świetlnego. Umożliwia to nie tylko kontrolę wizualną, ale także naprawę pewnych parametrów już zidentyfikowanej wady.
W wyniku oględzin należy sporządzić mapę defektologiczną wskazującą miejsca uszkodzeń, wad i odchyleń w miejscu złącza spawanego. Na podstawie uzyskanych danych szew jest finalizowany lub usuwanyszczegóły w zależności od możliwości przywrócenia witryny.
Namierz defekty do wykrycia
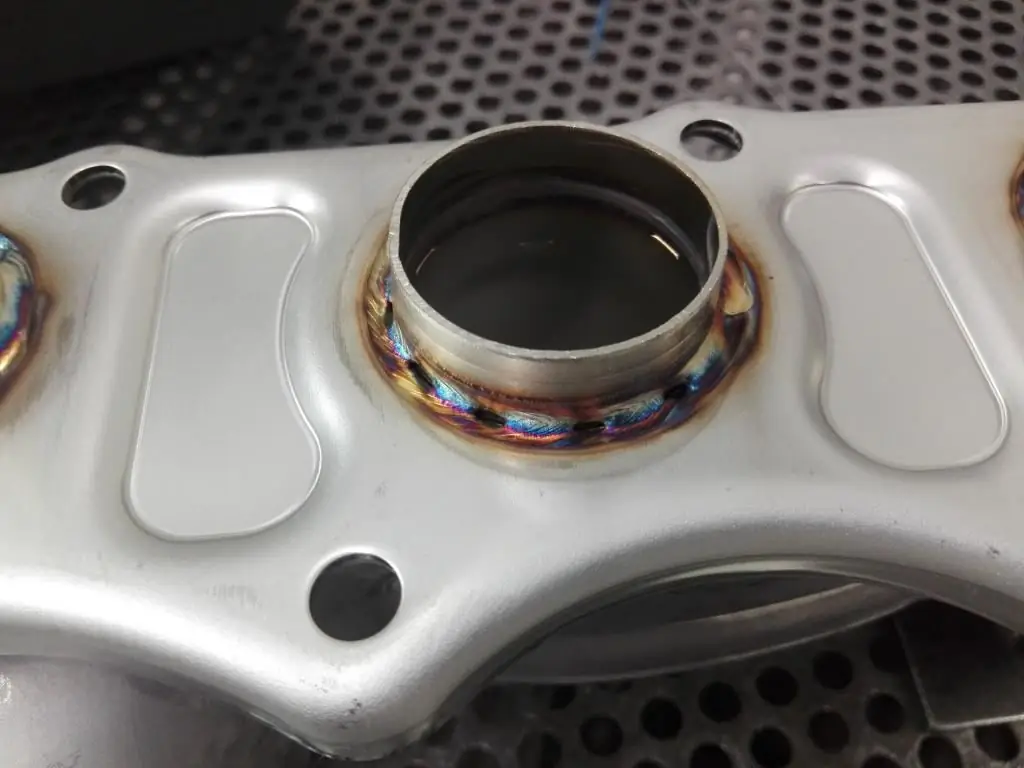
Główne wady i odchylenia spoiny, które są wykrywane podczas kontroli zewnętrznej, obejmują:
- Brak penetracji. Wyciek lub częściowa niewspółosiowość powierzchni dwóch części z powodu niewystarczająco stopionych krawędzi.
- Wklęsłości. Wręcz przeciwnie, dopuszczono nadmierne wtopienie grani spoiny, w wyniku czego struktura podstawy uległa deformacji. W takim przypadku oględziny tylko naprawiają fakt obecności defektu, a jego cechy ujawniają wewnętrzne nieniszczące metody badawcze.
- Podcięcia. Wcięcie podążające za linią stopu. Dozwolone ze względu na nieprawidłowy kierunek łuku podczas spawania lub ze względu na zewnętrzne uszkodzenia mechaniczne.
- Uderzenia. Zwykle powstają w wyniku niewłaściwego dostarczania mieszaniny gazów ochronnych lub z naruszeniem reżimu temperaturowego podczas topienia.
Stosowany instrument kontroli
Na poziomie podstawowym używane są najprostsze narzędzia do kontroli wizualnej, w tym lupy, suwmiarki, linijki i kwadraty. Wiroprądowe i ultradźwiękowe mierniki grubości, które dają wyobrażenie o parametrach wymiarowych defektów, można przypisać specjalistycznym urządzeniom do profesjonalnego testowania.
Szeroko stosowane do oględzin i szablonów, dzięki którym, nawet bez określonych pomiarów, możliwe jest określenie odchyleń właściwości szwu od wartości standardowych. W ten sposób porównano kształty szczelin, krawędzi izmontowane części do późniejszego połączenia. Szczególnie do określania stopnia falistości i chropowatości powierzchni stosuje się profilery-profilometry.
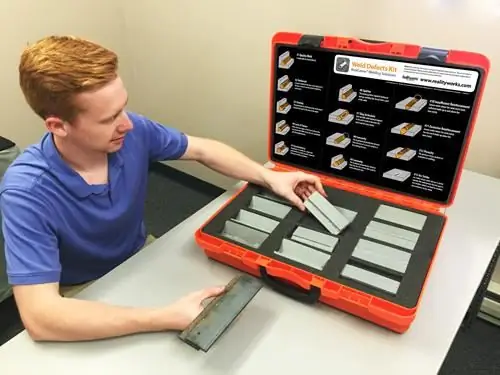
Cechy laserowej inspekcji wizualnej
Zarówno widzenie człowieka, jak i możliwości instrumentów optycznych mają swoje ograniczenia podczas badania powierzchni z większą dokładnością obserwacji. Najskuteczniejszym narzędziem do dogłębnej wizualnej kontroli złączy spawanych jest system skanowania laserowego z bardzo precyzyjną kamerą. Takie urządzenia umożliwiają wykonanie trójwymiarowych obrazów graficznych stanowisk obserwacyjnych z natychmiastową kalkulacją błędów spoin. Czyli w trybie analizy operacyjnej tworzy mapę defektów w postaci modelu komputerowego.
Ponadto urządzenie nie tylko zapewnia niezbędną listę początkowych parametrów do późniejszej analizy, ale w zależności od algorytmów przetwarzania danych potrafi samodzielnie klasyfikować połączenie na podstawie wskaźników geometrycznych, rodzaju wady itp. moduł skanujący z mikroprocesorem podejmuje decyzję o możliwościach dalszego wykorzystania części, biorąc pod uwagę stopień wykrytych odchyleń od normy.
Przygotowanie miejsca inspekcji
Zgodnie z przepisami prace prowadzone są na terenie stacjonarnym, wyposażonym w specjalne podesty, stojaki i stoły do pomieszczenia badanego obiektu i sprzętu. Często kontrola odbywa się w obszarze produkcji, co wynika z minimalizacji kosztów logistyki przy przeprowadzceczęści z bezpośredniego miejsca spawania do strefy kontrolnej. W tym przypadku szczególną uwagę zwraca się na ogrodzenia z terenu, na którym wykonywane są operacje technologiczne. Miejsce do badań dobierane jest również z uwzględnieniem sytuacji sanitarno-środowiskowej, co dotyczy zwłaszcza przedsiębiorstw z branży chemicznej i metalurgicznej.
Im lepiej oświetlony jest obszar roboczy, tym dokładniejsze będą wyniki kontroli wizualnej spoin. Oświetlenie powinno być wystarczająco jasne, aby zapewnić wiarygodne badanie kontrolowanej powierzchni, ale nie może przekraczać 500 Lx pod względem natężenia światła.
Przygotowanie do inspekcji
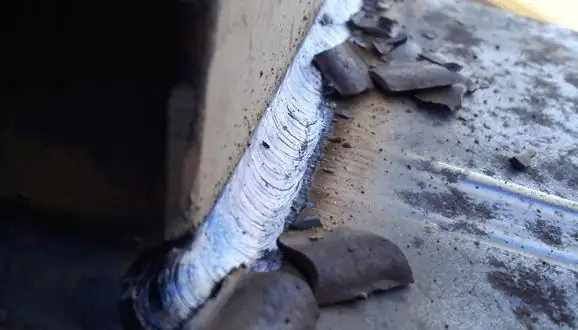
Bez względu na rodzaj i cechy badanego obiektu, jego powierzchnie muszą być odpowiednio oczyszczone. Wszelkie obce powłoki, które nie są częścią naturalnej struktury szwu, podlegają usunięciu. Dotyczy to zgorzeliny, farby, brudu, śladów rdzy i żużlu pozostawionego po spawaniu. Nie zawsze można kontrolować obiekty, których powierzchnie mają zabarwione kolory. Jeżeli kontrolowana powierzchnia jest częścią wyposażenia operacyjnego, urządzenie należy zatrzymać na czas trwania badania.
Z reguły dotyczy to urządzeń technologicznych, które zostały naprawione przez spawanie. Mowa o systemach wentylacyjnych, układach chłodzenia, agregatach sprężarkowych itp. Podczas przygotowań szczególną uwagę zwraca się na zestaw narzędzi do kontroli wizualnej oraz materiały eksploatacyjne, które będą wykorzystywane w trakcie pracy. Narzędzia muszą byćprawidłowo skonfigurowane, skalibrowane, przetestowane pod kątem wydajności i dokładności.
Procedura kontroli przychodzącej
Pierwszy etap kontroli zewnętrznej w procesie produkcyjnym, który ma na celu sprawdzenie półfabrykatów i części przed operacjami montażu. Na tym etapie wykrywane są pęknięcia, zachody słońca, wyszczerbienia, rozwarstwienia i skorupy spoin, które są niezgodne z wymaganiami dalszych operacji technologicznych. Zgodnie z instrukcją oględzin na etapie kontroli wjazdowej długość odcinków, które można sprawdzić bez wyposażenia pomocniczego, nie może przekraczać 100 mm.
W przeciwnym razie stosuje się przyrządy pomiarowe, które pozwalają na ustalenie parametrów geometrycznych defektów w trybie strumieniowym. Nawiasem mówiąc, oprócz bezpośrednio spawanych szwów, na tym etapie można ocenić stan krawędzi części, które będą jeszcze montowane przez spawanie.
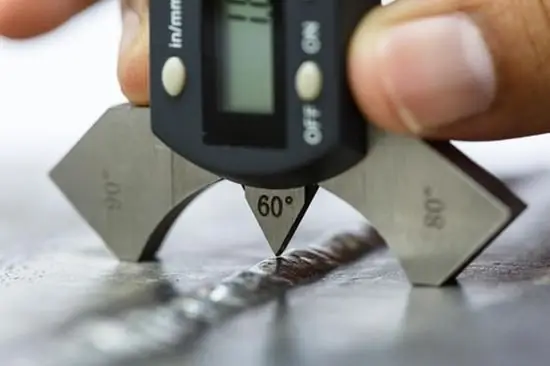
Rozliczanie kontrolowanych parametrów po spawaniu
Główny etap prac nad oględzinami części, które są przeprowadzane po zakończeniu montażu konstrukcji metodą zgrzewania termicznego. Głównym przedmiotem badań jest napawanie w postaci gotowej spoiny. Z reguły przeprowadza się wizualną kontrolę spoin warstwa po warstwie z utrwaleniem wad powierzchniowych. W przypadku braku możliwości dokładnej identyfikacji i oceny parametrów przetok, pęknięć i oznak zniszczenia ściegu spoiny, przeprowadza się analizę wewnętrzną konstrukcji z podłączeniem aparatury radiacyjnej lub ultradźwiękowej.
Parametry mierzone podczas kontroli
Z punktu widzenia wymagań dotyczących montażu technologicznego części i konstrukcji metalowych, ważniejsze jest nie naprawienie samego faktu obecności wady, ale jej wskaźników wymiarowych. Zgodnie z instrukcją kontroli wizualnej i pomiarowej podczas kompleksowego badania należy zarejestrować następujące wartości:
- Szerokość, długość i głębokość szwu.
- Rozmiar wybrzuszenia szwu.
- Parametry dla wiórów, pęknięć i muszli.
- Głębokość cięcia.
- Cięcie spoiny pachwinowej.
- Długość nieciągłości.
Indywidualnie, zgodnie z wymaganiami projektowymi, można również sporządzić mapę względnego położenia szwów. Na przykład zachowanie pewnej odległości między punktami połączeń jest często warunkiem zapewnienia niezawodności całej konstrukcji, dlatego uwzględnienie luk jest uważane za jedną z nadrzędnych wartości kontrolnych.
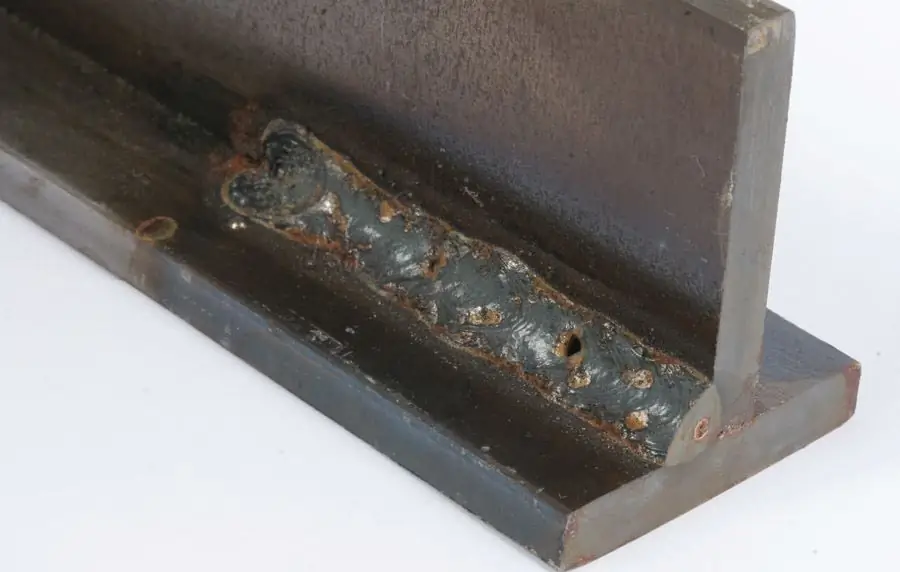
Kontrola działań naprawczych
W procesie naprawy wadliwych szwów i przywracania uszkodzonej struktury części metalowych wykonywane są również operacje kontrolne, których cele obejmują:
- Śledzenie kompletności wady.
- Identyfikacja nowych defektów spowodowanych użyciem środków do korekcji struktury szwu.
- Sprawdzenie ogólnego kształtu uszkodzonego obszaru.
- Monitorowanie czystości obiektu - w szczególności śledzenie zanieczyszczenia złącza olejem, produktami korozji, pyłami przemysłowymi itp.
Równieżwizualna metoda kontroli pozwala na zachowanie w granicach normatywnych parametrów operacji mechanicznych niezbędnych do skorygowania struktury złącza spawanego. W szczególności kontrolowana jest głębokość próbkowania wadliwego szwu, szerokość strefy zdzierania, ilość krawędzi tnących, kąty ukosowania itp.
Zarejestruj wyniki
Dane kontrolne są rejestrowane w specjalnym rejestrze, po czym sporządzana jest dokumentacja w formie aktu, protokołu lub wniosku na podstawie wyników badania. Gdy przeprowadzana jest wizualna kontrola jakości, na powierzchni obszaru docelowego umieszczany jest również znak wskazujący wyniki kontroli. Na przykład może to być stempel z dostępem do dalszych operacji technologicznych w procesie produkcyjnym. W przeciwnym razie puste miejsce jest wysyłane do naprawy lub rewizji.
Wniosek
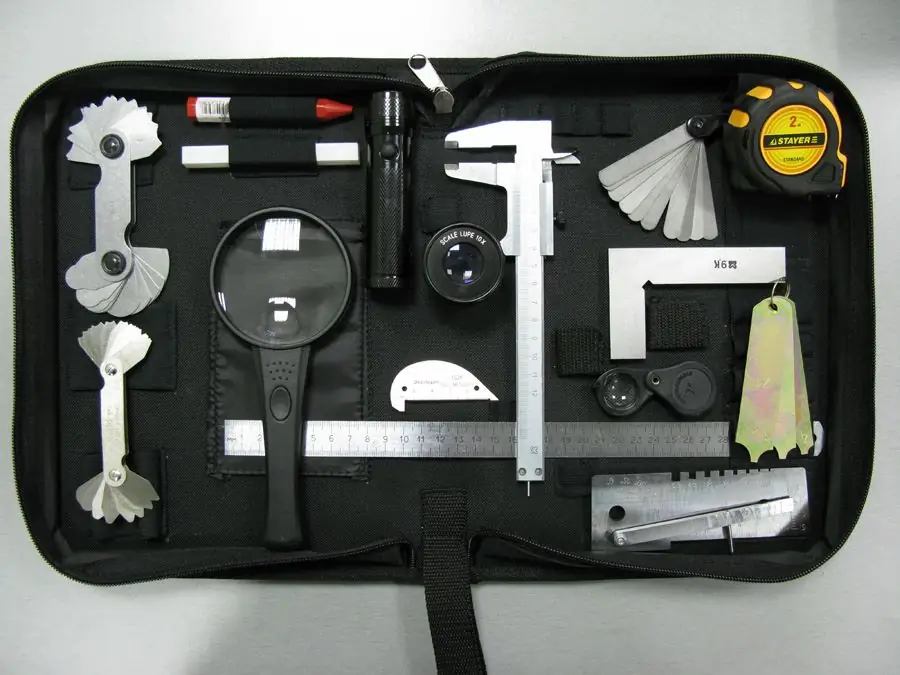
Technologie organizowania i przeprowadzania czynności kontrolnych i weryfikacyjnych w odniesieniu do części stałych i materiałów są stale udoskonalane, co pozwala na wykrycie jego najmniejszych wad bez uszkodzenia przedmiotu badań. Niemniej jednak nadal aktywnie wykorzystywane są najprostsze metody oględzin, które są znacznie ograniczone w możliwościach kontroli punktowej.
Ta praktyka jest naprawdę nieporównywalna pod względem wydajności z nowoczesnymi metodami nieniszczącej analizy wewnętrznej tych samych spoin. Ale, jak zauważono w instrukcjach kontroli wizualnej i pomiarowej, badanie zewnętrzne dotyczy tylko najbardziej wyraźnych wad.powierzchnie, z których część można wyeliminować bez użycia specjalistycznych urządzeń i materiałów eksploatacyjnych. Innymi słowy, przy minimalnych kosztach organizacji kontroli i środków technicznych ujawnia się najbardziej brutalne małżeństwo. Następnie obrabiany przedmiot kierowany jest do kolejnych etapów dokładniejszej kontroli, co wymaga użycia specjalistycznych urządzeń magnetycznych, rentgenowskich i ultradźwiękowych, które nie nadają się do zastosowania w pierwotnej kontroli oczywistych wad powierzchni.
Zalecana:
Zasady wypełniania zaświadczenia 2 podatek dochodowy od osób fizycznych: instrukcje krok po kroku, wymagane formularze, terminy i procedura dostawy
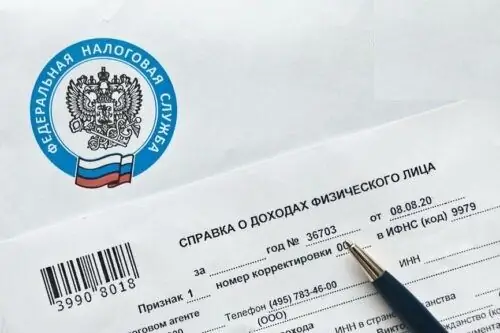
Osoby fizyczne są zobowiązane do przekazywania podatków naliczonych od ich dochodów do środków budżetu państwa. Aby to zrobić, wypełniane jest zaświadczenie o 2 podatku dochodowym od osób fizycznych. Ten dokument przedstawia dane o dochodach i odliczeniach podatkowych osób fizycznych. Pracodawca jest zobowiązany do corocznego przekazywania tej dokumentacji właściwym organom regulacyjnym w miejscu jego rejestracji. Instrukcje i zasady wypełniania zaświadczenia 2 podatku dochodowego od osób fizycznych zostaną omówione w artykule
Rejestracja po otrzymaniu TRP: wykaz dokumentów, procedura postępowania, warunki
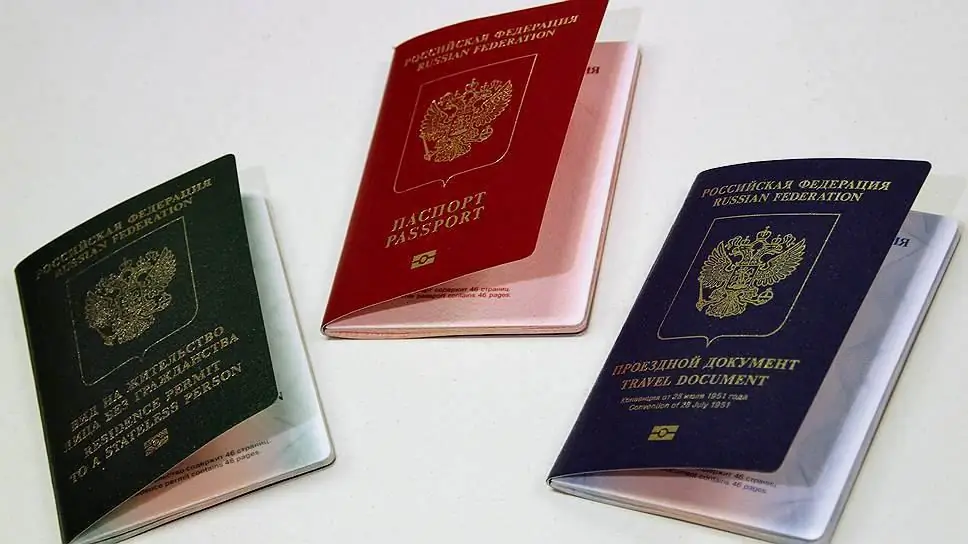
Po otrzymaniu TRP rejestracja w dowolnej nieruchomości jest procesem obowiązkowym dla każdego cudzoziemca. Artykuł opisuje ramy czasowe rejestracji, a także jakie dokumenty są do tego potrzebne
Jak rozpocząć sprzedaż mieszkania: przygotowanie dokumentów, procedura postępowania, wskazówki od pośredników
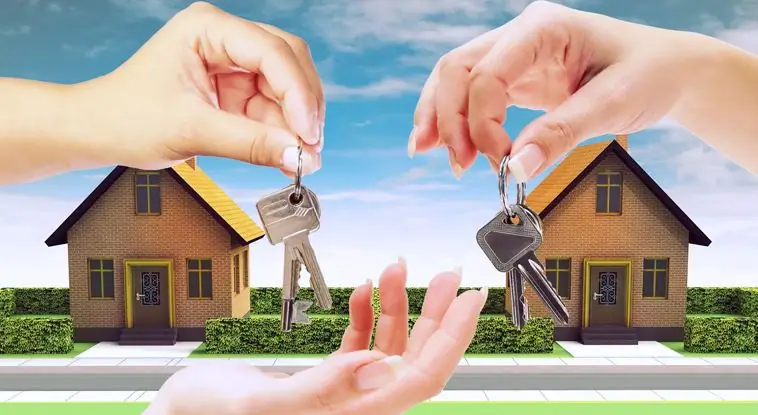
W życiu każdego człowieka może być konieczna sprzedaż jakiejkolwiek nieruchomości. A jeśli używane przedmioty, takie jak meble, sprzęt AGD czy samochód, można bez problemu sprzedać za pośrednictwem gazet lub tablic ogłoszeniowych, to sprzedaż mieszkania to zupełnie inna sprawa. Gdzie zacząć? Jakie dokumenty są potrzebne? Jak zawrzeć umowę, aby uniknąć problemów w przyszłości?
Zatrudnienie nieletniego pracownika: procedura krok po kroku, dokumenty
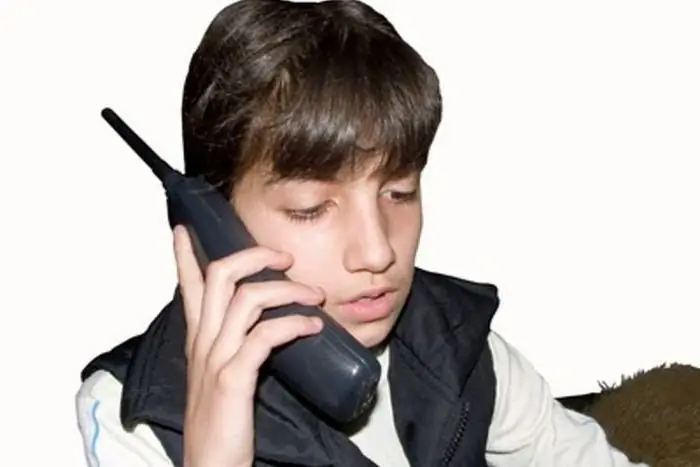
Obecne prawodawstwo przewiduje normy gwarantujące ochronę pracy dzieci i młodzieży. W Kodeksie pracy w szczególności istnieje szereg przepisów regulujących zatrudnianie małoletniego pracownika
Co to są badania radiograficzne? Radiograficzna kontrola spoin. Kontrola radiograficzna: GOST
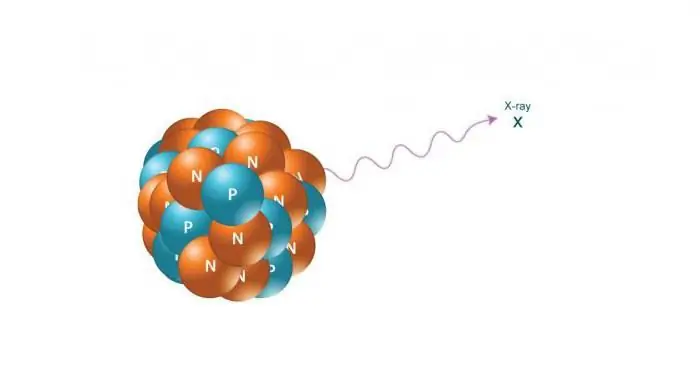
Fizyczne podstawy metod kontroli promieniowania. Cechy kontroli radiograficznej. Główne etapy radiograficznej kontroli spoin. Środki ostrożności w produkcji kontroli radiograficznej. Dokumentacja normatywna i techniczna