2025 Autor: Howard Calhoun | [email protected]. Ostatnio zmodyfikowany: 2025-06-01 07:14
W procesach otrzymywania stali o wysokiej wytrzymałości ważną rolę odgrywają operacje stopowe i modyfikacja składu podstawowego. Podstawą takich procedur jest technika dodawania zanieczyszczeń metalicznych o różnych właściwościach, ale niemałe znaczenie ma również regulacja gaz-powietrze. Na tę operację technologiczną ukierunkowana jest praca konwertera tlenowego, który jest szeroko stosowany w metalurgii przy produkcji stopów stali w dużych ilościach.
Projekt konwertera
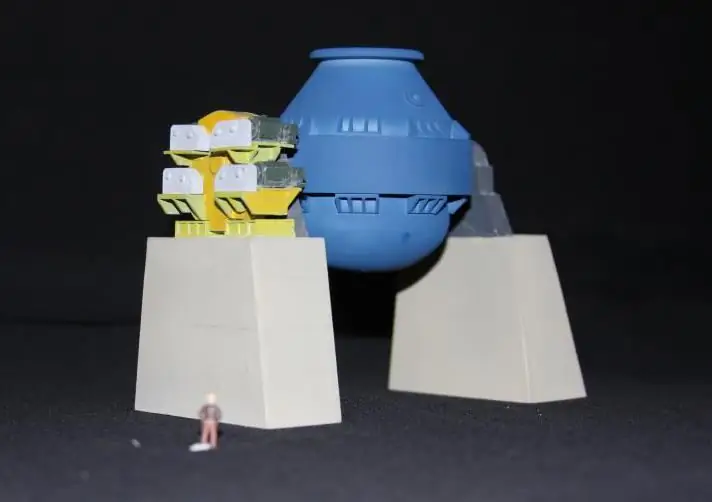
Sprzęt to naczynie w kształcie gruszki, wyposażone w wewnętrzną wyściółkę i otwór spustowy do wytapiania produktów. W górnej części konstrukcji przewidziano otwór z szyjką do dostarczania lancy, złomu, stopionego żelaza, mieszanin stopowych i usuwania gazu. Tonaż waha się od 50 do 400 ton Blacha lub spawana stal średnia jest używana jako materiały do produkcji konstrukcji.około 50-70 mm grubości. Typowy konwerter tlenu przewiduje możliwość odpięcia dna - są to modyfikacje z przedmuchiwaniem dna mieszankami gaz-powietrze. Wśród elementów pomocniczych i funkcjonalnych bloku można wyróżnić silnik elektryczny, infrastrukturę rurociągową do przepływu tlenu, łożyska oporowe, platformę przepustnicy oraz ramę nośną do montażu konstrukcji.
Pierścienie podtrzymujące i czop
Przetwornica jest umieszczona na łożyskach wałeczkowych, które są zamocowane na ramie. Projekt może być stacjonarny, ale to rzadkość. Zwykle na etapie projektowania określa się możliwość transportu lub przemieszczenia jednostki w określonych warunkach. Za te funkcje odpowiada sprzęt w postaci pierścieni nośnych i kołków. Grupa łożysk zapewnia możliwość skręcania sprzętu wokół osi czopów. Poprzednie modele konwertorów zakładały połączenie wyposażenia nośnego i korpusu urządzenia do topienia, ale ze względu na działanie wysokich temperatur i deformację materiałów pomocniczych, to rozwiązanie konstrukcyjne zostało zastąpione bardziej złożonym, ale niezawodnym i trwałym schematem interakcji między jednostka funkcjonalna i zbiornik.
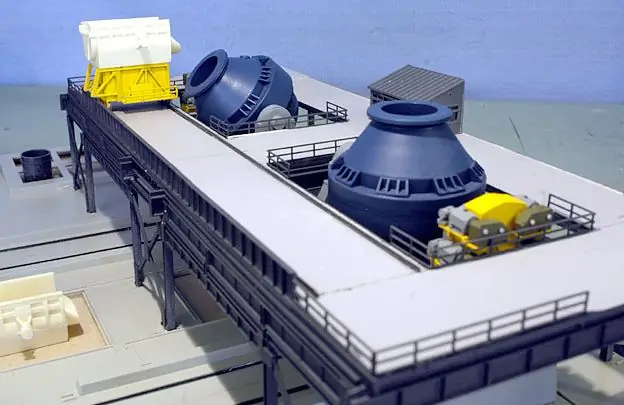
W szczególności nowoczesny konwerter tlenu jest wyposażony w oddzielny pierścień nośny, w którego strukturę wprowadzono również czopy i nieruchomą obudowę. Szczelina technologiczna pomiędzy obudową a podstawą nośną zapobiega negatywnemu wpływowi temperatury na wrażliwe elementy zawieszeń i mechanizmów ruchomych. System mocowania samego konwertera realizowany jest za pomocą przystanków. Sam pierścień nośny jest nośnikiem, na który składają się dwa półpierścienie i płyty czopowe zamocowane w punktach dokowania.
Mechanizm obrotowy
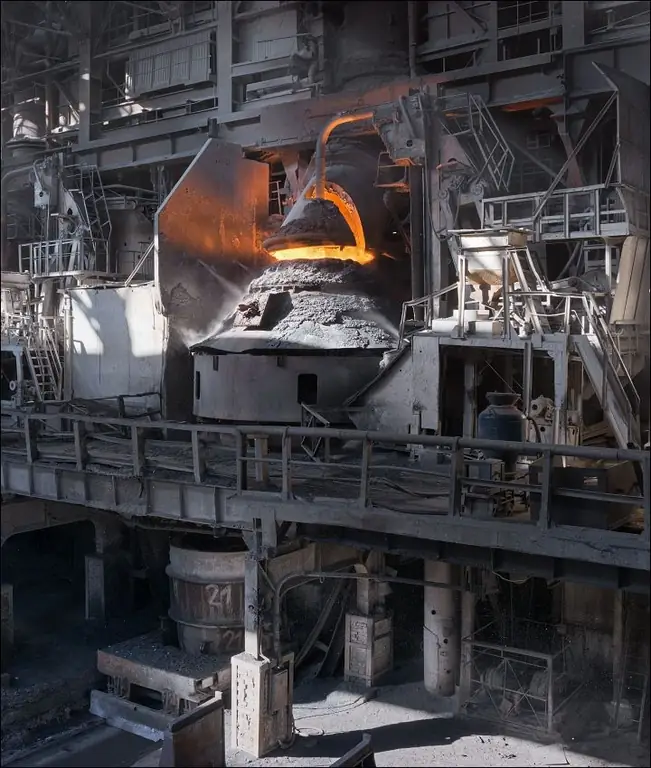
Napęd elektryczny umożliwia obracanie konwertera o 360°. Średnia prędkość obrotowa wynosi 0,1-1 m/min. Sama ta funkcja nie zawsze jest wymagana - w zależności od organizacji operacji technologicznych podczas przepływu pracy. Na przykład, może być wymagany obrót, aby skierować szyjkę bezpośrednio do punktu dostarczania złomu, odlewania żelaza, spuszczania stali itp. Funkcjonalność mechanizmu obrotowego może być inna. Istnieją zarówno systemy jednokierunkowe, jak i dwukierunkowe. Z reguły konwertery tlenu o nośności do 200 ton zakładają skręt tylko w jednym kierunku. Wynika to z faktu, że w takich konstrukcjach wymagany jest mniejszy moment obrotowy podczas przechylania szyjki. Aby wyeliminować zużycie nadmiaru energii podczas pracy sprzętu o dużym obciążeniu, wyposażony jest w dwukierunkowy mechanizm obrotu, który rekompensuje koszt manipulacji szyją. Konstrukcja układu skrętnego obejmuje skrzynię biegów, silnik elektryczny i wrzeciono. Jest to tradycyjny układ napędu stacjonarnego montowanego na wylewce betonowej. Bardziej technologiczne mechanizmy zawiasowe są mocowane na czopie i napędzane przez napędzane koło zębate z systemem łożysk, które są również uruchamiane przez silniki elektryczne poprzez układ wałków.
Wymiary konwertera
Podczas projektowania parametry projektowe muszą być obliczane w oparciu o przybliżoną objętość oczyszczania, z wyłączeniem wyrzucania stopionego materiału, który zostanie wytworzony. W ostatnich latach opracowano jednostki, które przyjmują materiały w ilościach od 1 do 0,85 m3/t. Oblicza się również nachylenie gardła, którego kąt wynosi średnio od 20° do 35°. Praktyka obsługi takich obiektów pokazuje jednak, że przekroczenie nachylenia 26° pogarsza jakość okładziny. W głębokości wymiary konwertera wynoszą 1-2 m, ale wraz ze wzrostem ładowności wysokość konstrukcji może również wzrosnąć. Konwencjonalne konwertery o głębokości do 1 m mogą przyjąć obciążenie nie większe niż 50 t. Jeśli chodzi o średnicę, waha się ona średnio od 4 do 7 m. Grubość szyjki wynosi 2-2,5 m.
Podszewka BOF
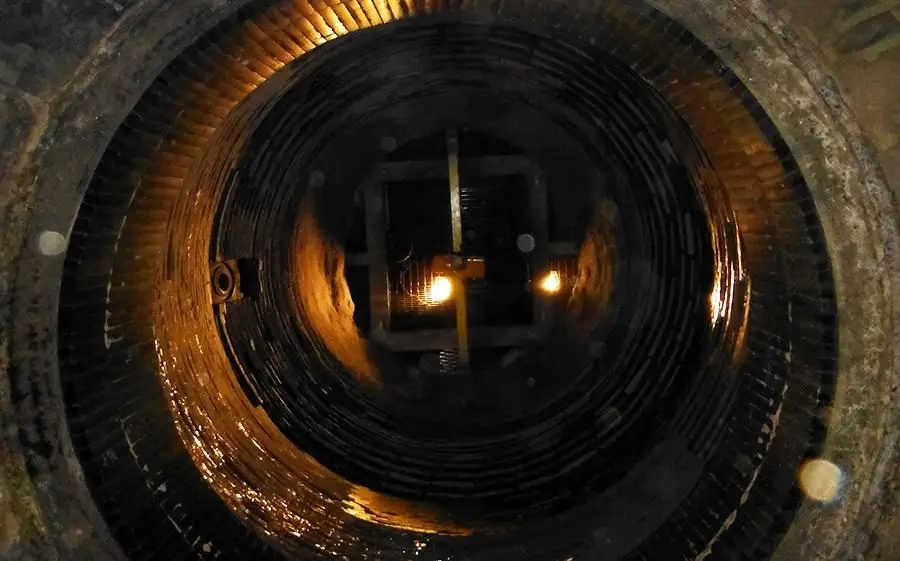
Obowiązkowa procedura technologiczna, podczas której wewnętrzne ściany konwertera pokrywane są warstwą ochronną. Jednocześnie należy wziąć pod uwagę, że w przeciwieństwie do większości pieców hutniczych, konstrukcja ta poddawana jest znacznie większym obciążeniom termicznym, co również decyduje o cechach wyłożenia. Jest to zabieg polegający na ułożeniu dwóch warstw ochronnych - funkcjonalnej i wzmacniającej. Warstwa zbrojenia ochronnego o grubości 100-250 mm przylega bezpośrednio do powierzchni nadwozia. Jej zadaniem jest ograniczanie strat ciepła i zapobieganie wypalaniu wierzchniej warstwy. Zastosowany materiał to cegła magnezytowa lub magnezytowo-chromitowa, która może służyć latami bez odnawiania.
Górna warstwa robocza ma grubość około 500-700 mm i jest dość często wymieniana w miarę zużywania się. Na tym etapie BOF jest poddawany obróbce niepalnymi związkami ogniotrwałymi wiązanymi piaskiem lub żywicą. Materiałem bazowym tej warstwy wykładziny jest dolomit z dodatkami magnezytu. Standardowe obliczenia obciążenia są oparte na wpływie temperatury około 100-500 °C.
Podszewka z betonu natryskowego
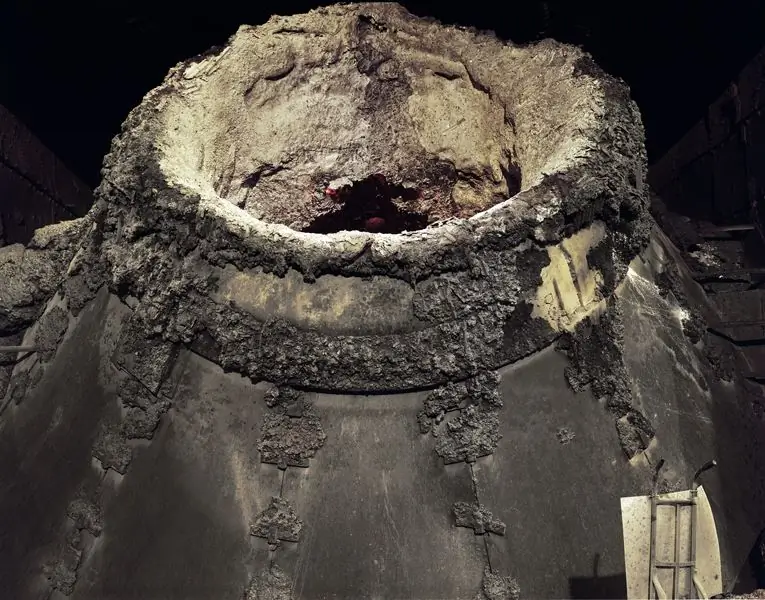
Pod wpływem agresywnych temperatur i wpływów chemicznych wewnętrzne powierzchnie konstrukcji przetwornika szybko tracą swoje właściwości - ponownie dotyczy to zewnętrznego zużycia warstwy roboczej ochrony termicznej. Wykładzina z betonu natryskowego jest stosowana jako operacja naprawcza. Jest to technologia redukcji na gorąco, w której kompozycję ogniotrwałą układa się za pomocą specjalnego sprzętu. Nakłada się go nie w sposób ciągły, ale punktowo na mocno zużyte miejsca podszewki bazowej. Zabieg wykonywany jest na specjalnych maszynach do betonu natryskowego, które podają chłodzoną wodą lancę z masą pyłu koksowego i proszku magnezytowego do uszkodzonego obszaru.
Technologie wytapiania
Tradycyjnie istnieją dwa podejścia do realizacji topienia konwertorowego - Bessemer i Thomas. Jednak nowoczesne metody różnią się od nich niską zawartością azotu w piecu, co poprawia jakość procesu pracy. Technologia realizowana jest w następujących etapach:
- Ładowanie złomu. Około 25-27% całkowitej masy ładunku jest ładowane do nachylonego konwertera za pomocą czerpaków.
- Wypełnianieżeliwo lub stop stali. Ciekły metal o temperaturze do 1450 °C wlewany jest do przechylnego konwertora za pomocą kadzi. Operacja trwa nie dłużej niż 3 minuty.
- Oczyść. W tej części technologia wytwarzania stali w konwertorach tlenowych pozwala na różne podejścia w zakresie dostarczania mieszanki gazowo-powietrznej. Przepływ może być kierowany z góry, z dołu, z dołu lub kombinacją, w zależności od rodzaju konstrukcji urządzenia.
- Odbieranie próbek. Mierzy się temperaturę, usuwa niepożądane zanieczyszczenia i oczekuje się analizy składu. Jeśli jego wyniki spełniają wymagania projektowe, stopiony materiał jest uwalniany, a jeśli nie, wprowadzane są poprawki.
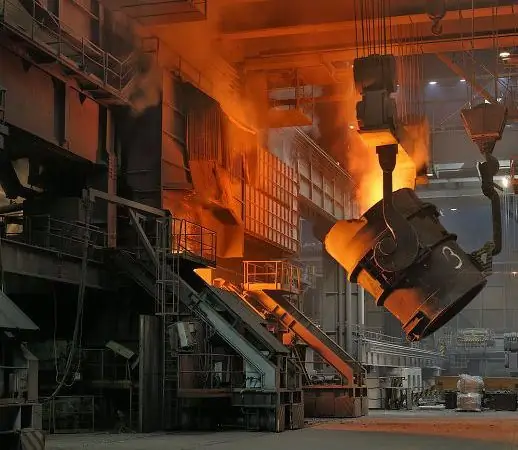
Wady i zalety technologii
Metoda jest ceniona za wysoką wydajność, proste schematy dostarczania tlenu, niezawodność konstrukcji i ogólnie stosunkowo niskie koszty organizacji procesu. Jeśli chodzi o wady, to w szczególności obejmują one ograniczenia w zakresie dodawania osadów i surowców wtórnych. Ten sam złom z innymi wtrąceniami nie może przekraczać 10%, co nie pozwala na modyfikację struktury wytopu w wymaganym zakresie. Ponadto dmuchanie zużywa dużą ilość przydatnego żelaza.
Zastosowanie technologii
Kombinacja plusów i minusów ostatecznie zdeterminowała charakter zastosowania konwerterów. W szczególności zakłady metalurgiczne produkują wysokogatunkową stal niskostopową, węglową i stopową, wystarczającą do wykorzystania tego materiału w przemyśle ciężkim i budownictwie. Odbieranie stali wkonwerter tlenu jest stopowany i poprawia indywidualne właściwości, co rozszerza zakres produktu końcowego. Z otrzymanych surowców wytwarzane są rury, drut, szyny, osprzęt, okucia itp. Technologia ta jest również szeroko stosowana w metalurgii metali nieżelaznych, gdzie miedź konwertorowa jest uzyskiwana przy wystarczającym wdmuchiwaniu.
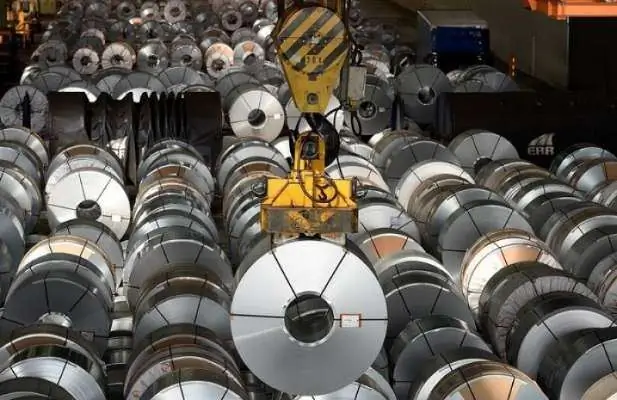
Wniosek
Wytapianie w zakładach konwertorowych jest uważane za technikę moralnie przestarzałą, ale nadal jest stosowana ze względu na optymalne połączenie wydajności i kosztów finansowych procesu. W dużej mierze popyt na technologię ułatwiają także zalety konstrukcyjne zastosowanego sprzętu. Ta sama możliwość bezpośredniego załadunku złomu metalowego, wsadu, szlamu i innych odpadów, choć w ograniczonym zakresie, rozszerza możliwości modyfikacji stopu. Inną rzeczą jest to, że do pełnoprawnego działania wielkogabarytowych konwerterów z możliwością obracania wymagana jest organizacja odpowiedniego pomieszczenia w przedsiębiorstwie. Dlatego wytapianie z oczyszczaniem tlenowym w dużych ilościach jest prowadzone głównie przez duże firmy.
Zalecana:
Spawalność stali: klasyfikacja. Grupy spawalności stali
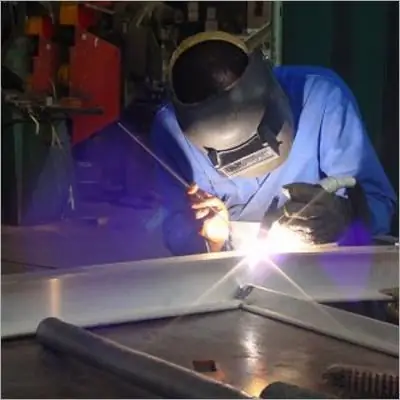
Głównym materiałem konstrukcyjnym jest stal. Jest to stop żelazowo-węglowy zawierający różne zanieczyszczenia. Wszystkie składniki zawarte w jego składzie wpływają na właściwości wlewka. Jedną z właściwości technologicznych metali jest możliwość tworzenia wysokiej jakości połączeń spawanych
Biznesplan produkcji styropianu: etapy otwierania krok po kroku, technologia produkcji, obliczanie dochodów i wydatków
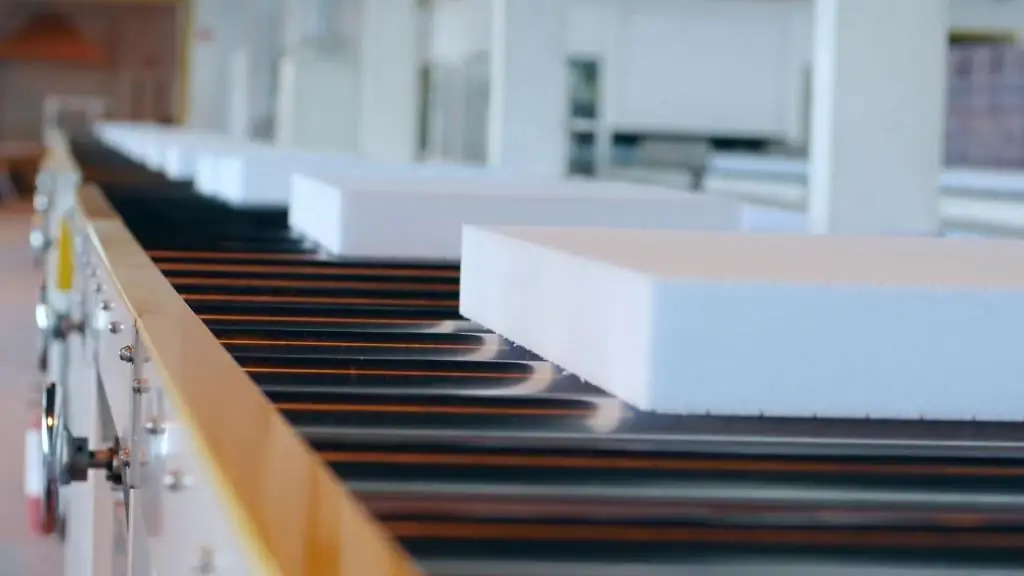
Polifoam można przypisać jednemu z najczęściej używanych materiałów budowlanych. Zapotrzebowanie na nią jest dość duże, ponieważ rozwijają się rynki zbytu, które przy kompetentnym podejściu marketingowym mogą zapewnić stabilne zyski przez długi czas. W tym artykule szczegółowo omówimy biznesplan dotyczący produkcji tworzywa piankowego
Piec koksowniczy - urządzenie hutnicze do produkcji koksu: urządzenie
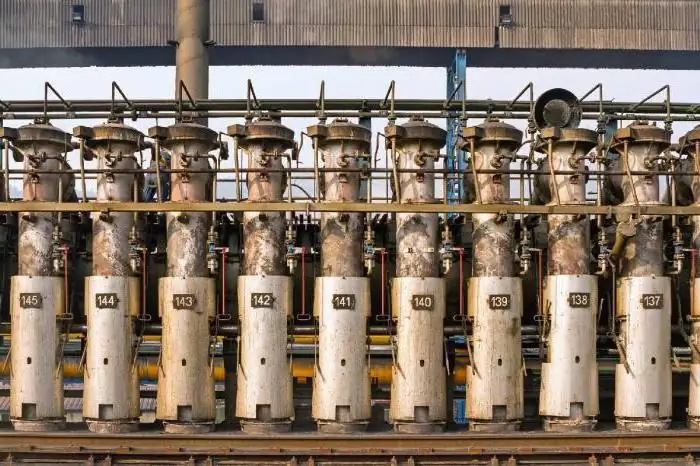
Wprowadzenie do eksploatacji pieców koksowniczych rozpoczęło się w latach 50. ubiegłego wieku. Użyteczna objętość pierwszych typowych pieców wynosiła 21,6 Nm³. W dalszej części artykułu rozważymy urządzenie wymienionego sprzętu
Baterie koksownicze: urządzenie, zasada działania, przeznaczenie. Technologia produkcji koksu
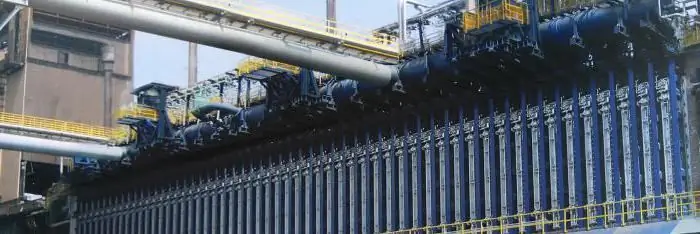
Baterie koksownicze to złożony i ważny obiekt przemysłowy. Porozmawiamy o jego pracy i urządzeniu w artykule
Metody produkcji PCB: technologia produkcji
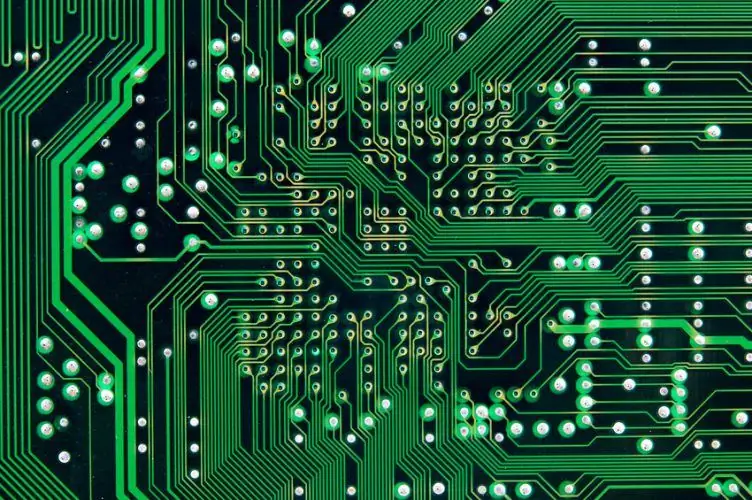
W oprzyrządowaniu i ogólnie w elektronice płytki drukowane odgrywają kluczową rolę jako nośniki połączeń elektrycznych. Od tej funkcji zależy jakość urządzenia i jego podstawowa wydajność. Nowoczesne metody wytwarzania płytek drukowanych kierują się możliwością niezawodnej integracji podstawy elementu o dużej gęstości upakowania, co zwiększa wydajność produkowanego sprzętu